GB battery watering systems automate electrolyte maintenance in lead-acid batteries using valve-regulated ports and float sensors. They monitor fluid levels and dispense deionized water only when needed, preventing overfilling and sulfation. Commonly used in forklift batteries, these systems reduce maintenance labor by 80% while extending battery lifespan through precise pH and density control. How to Access the Battery on a Toyota Forklift
How do GB watering systems function?
GB systems use gravity-fed valves and dual-stage sensors to regulate water flow. When electrolyte levels drop, float valves open, releasing water until sensors detect optimal levels. Pro Tip: Always use deionized water—minerals in tap water accelerate plate corrosion.
Designed for flooded lead-acid batteries, GB systems connect via manifolds to each cell. The reservoir’s elevation creates gravitational pressure, ensuring uniform distribution. For instance, a typical 48V forklift battery requires a 12-valve manifold adjusted to 1–1.5 psi. Transitional components like pressure-relief vents prevent airlocks. But what if sensors fail? Built-in redundancies include mechanical shutoffs when water exceeds maximum levels. Practically speaking, these systems are like automated irrigation for battery cells—delivering hydration on demand without manual checks.
Wholesale lithium golf cart batteries with 10-year life? Check here.
What are the key components?
Core parts include polyethylene manifolds, needle valves, and multi-stage float sensors. The manifold’s port spacing must match battery cell spacing (usually 2.75–4 inches for industrial batteries).
Want OEM lithium forklift batteries at wholesale prices? Check here.
Manifold tubing is chemically resistant to acidic environments, rated for 10+ years of service. Needle valves allow flow adjustment per cell—critical since end cells often require 15% more water. Sensors combine magnetic reed switches and buoyant floats; when fluid dips, the float drops, triggering valve activation. Ever wonder why some systems have dual sensors? Redundant sensors prevent underfill if one fails. For example, Tesla’s GB-style systems in Megapack installations use titanium sensors for harsh environments. Pro Tip: Replace O-rings annually—hardened seals cause leaks that corrode terminals.
Component | Function | Failure Impact |
---|---|---|
Float Sensor | Detects electrolyte level | Overfilling or dry cells |
Manifold | Distributes water | Uneven watering |
Needle Valve | Controls flow rate | Flooding or slow refill |
Why choose GB over manual watering?
GB systems eliminate human error and provide pH-optimized hydration. Manual watering risks under/overfilling, causing thermal runaway or stratification.
In a study by Battery Council International, GB-equipped batteries lasted 1,200 cycles vs. 900 for manually maintained ones. Automation ensures watering occurs at the ideal charge state (50% SoC), when plates are fully submerged but not overpressurized. Think of it as cruise control for battery maintenance—consistent precision beyond manual capability. Plus, OSHA reports cite 60% fewer acid spills with automated systems. Transitioning to GB can cut monthly maintenance hours from 10 to 2.
How to maintain GB systems?
Inspect valve seals quarterly and flush reservoirs biannually. Use conductivity meters to verify water purity below 5 μS/cm.
Maintenance starts with visual checks—cracked tubing or stuck floats demand immediate replacement. Flushing removes mineral buildup: disconnect the manifold, circulate 10% vinegar solution, then rinse with deionized water. A real-world example: Amazon warehouses schedule GB maintenance during battery rotations, synchronizing it with terminal cleaning. But how often is too often? Over-flushing degrades valve seats—stick to biannual unless water hardness exceeds 120 ppm. Pro Tip: Log all maintenance—manufacturers require proof of care for warranty claims.
Task | Frequency | Tool Required |
---|---|---|
Seal Inspection | Quarterly | Flashlight |
Reservoir Flush | Biannually | Vinegar solution |
Sensor Test | Annually | Multimeter |
Are GB systems universal?
No—manifold designs vary by battery voltage and cell spacing. Forklift batteries need 24–80V compatibility and corrosion-resistant materials.
GB kits are tailored for battery dimensions. A 36V system with 18 cells requires a 18-port manifold, while 48V setups use 24-port. Material matters too: polyethylene suits mild environments, but stainless steel fittings are needed for marine applications. For example, Johns Hopkins Hospital uses titanium GB components in disinfection-prone areas. Always verify CE or UL certifications—uncertified manifolds may leak under vibration. Forklift Battery Charging Station: A Comprehensive Guide
Redway Battery Expert Insight
FAQs
Typically every 10–15 charge cycles, depending on usage. High-drain applications (e.g., cold storage) may need weekly refills.
Can GB systems retrofit older batteries?
Yes, if cell spacing matches the manifold. Measure center-to-center distances before purchasing—adjustable manifolds suit 2.75–4″ ranges.
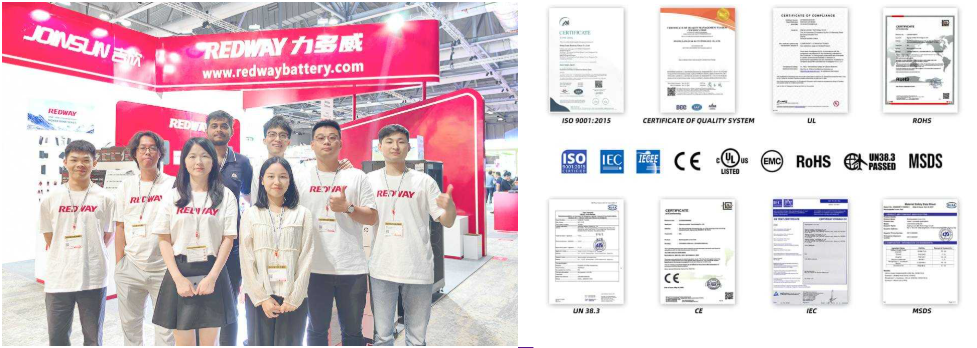