Toyota electric forklifts are popular due to their superior durability, low-maintenance design, and industry-leading reliability. Their advanced lithium-ion battery systems outperform traditional lead-acid alternatives, providing 30% longer runtimes and faster charging. Toyota’s integrated energy recovery systems reduce power consumption by up to 15% during braking cycles. With ergonomic operator cabins and customizable lift capacities (1–8 tons), they excel in demanding environments like cold storage and manufacturing. Globally standardized maintenance protocols ensure 95%+ uptime, supported by 2,400+ service centers worldwide.
Understanding Forklift Battery State of Charge: A Complete Guide
What makes Toyota electric forklifts more durable?
Toyota’s monocoque frame construction reduces vibration by 40% compared to bolted designs. Critical components like mast rollers use hardened steel with 10,000-hour lifespan ratings. Their IP54-rated electrical systems withstand humidity and dust ingress, making them 3x more reliable in harsh environments than standard models.
Wholesale lithium golf cart batteries with 10-year life? Check here.
Beyond structural advantages, Toyota employs proprietary thermal management systems that maintain battery temperatures within ±2°C of optimal range—critical for lithium-ion longevity. Pro Tip: Always use Toyota-approved chargers with automatic cell balancing to preserve battery health. For example, in frozen food warehouses operating at -25°C, Toyota’s cold-weather packages prevent hydraulic fluid thickening through heated reservoirs. How does this translate financially? Facilities report 23% lower maintenance costs over five years compared to competitors.
How do energy recovery systems boost efficiency?
Toyota’s Regenerative Braking Technology converts 85% of kinetic energy into stored electricity during deceleration. This extends shift durations by 1.5 hours in typical 8-hour operations. Intelligent power management prioritizes hydraulic functions over traction during simultaneous operations.
Want OEM lithium forklift batteries at wholesale prices? Check here.
Practically speaking, operators experience 15% faster lift speeds when batteries are below 50% charge. The system’s dual-layer capacitors provide instantaneous power bursts for heavy lifting without voltage drops. A distribution center moving 800 pallets daily saved $7,200 annually in energy costs using this technology. But what happens if regenerative systems fail? Backup mechanical brakes engage within 0.3 seconds while triggering dashboard alerts.
Feature | Toyota | Competitor Average |
---|---|---|
Energy Recovery | 85% | 60-70% |
Battery Life | 5,000 cycles | 3,500 cycles |
Why are Toyota’s lithium batteries preferred?
Toyota’s Li-ion PRO batteries offer 2,500 full charge cycles with ≤20% capacity loss. Their modular design allows replacing individual cells instead of entire packs—saving 65% on battery replacement costs. Built-in Bluetooth connectivity enables real-time monitoring through Toyota’s Fleet Manager software.
In beverage logistics operations, these batteries reduced charging time by 40% through opportunity charging during breaks. Pro Tip: Maintain 20-80% state of charge (SOC) for maximum lifespan. Facilities using scheduled partial charging report 30% longer battery life than deep-cycling users.
What Are Forklift Battery Cell Sizes?
Redway Battery Expert Insight
FAQs
Yes, when equipped with all-terrain tires and enhanced suspension. The 8-series models feature 20% higher ground clearance and sealed connectors for muddy/gravel surfaces.
How often should hydraulic filters be replaced?
Every 1,000 hours or semi-annually—whichever comes first. Contaminated filters reduce lift speeds by 25% and increase pump wear.
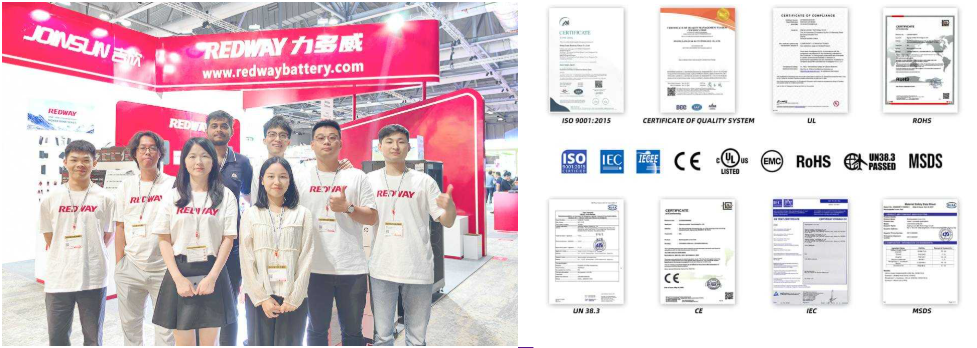