Forklift battery chargers are devices designed to restore energy to lead-acid or lithium-ion batteries powering industrial forklifts. They operate on CC-CV (constant current-constant voltage) principles, tailored to battery chemistry and capacity. Key features include thermal sensors, voltage regulation, and compatibility with 24V to 80V systems. Proper charging preserves battery lifespan—overcharging lithium packs beyond 4.2V/cell accelerates degradation. Modern chargers integrate smart protocols for adaptive charging cycles, reducing energy waste by 15–20%.
How to Access the Battery on a Toyota Forklift
What are the main types of forkllift battery chargers?
Forklift chargers include traditional ferroresonant, high-frequency, and smart chargers. Ferroresonant units use magnetic saturation for voltage control, while high-frequency models leverage IGBT transistors for 90%+ efficiency. Smart chargers dynamically adjust current based on temperature and SoC (state of charge), preventing sulfation in lead-acid batteries. Lithium-ion variants require precise CC-CV staging with BMS integration.
Wholesale lithium golf cart batteries with 10-year life? Check here.
Traditional ferroresonant chargers dominate legacy fleets due to ruggedness, but they waste 10–15% energy as heat. High-frequency chargers, conversely, reduce AC/DC conversion losses, ideal for multi-shift operations. Smart chargers shine in mixed fleets—they detect battery type and apply optimal profiles. For example, a 48V 600Ah lead-acid pack needs a 70A charger (≈8 hours), while a lithium pack with 1C rating charges in 1 hour. Pro Tip: Use automatic equalization modes monthly for lead-acid to prevent stratification.
Type | Efficiency | Charge Time (48V/600Ah) |
---|---|---|
Ferroresonant | 80–85% | 10–12h |
High-Frequency | 90–94% | 7–8h |
Smart | 92–96% | 5–6h |
How does battery capacity impact charging time?
Charging duration scales with Ah capacity and charger output. A 30A charger replenishes a 300Ah battery in ≈10h (C/10 rate). Higher currents (e.g., 100A) shorten times but risk overheating if not monitored. Lithium batteries tolerate 1C (300A for 300Ah), enabling 1-hour fast charges. Lead-acid cells degrade if charged beyond 0.2C regularly.
Want OEM lithium forklift batteries at wholesale prices? Check here.
Beyond raw capacity, temperature plays a hidden role. Cold batteries (below 10°C) require reduced current to avoid plating in lead-acid units. Conversely, lithium batteries below 0°C shouldn’t charge at all—internal resistance spikes can cause dendrites. For a 500Ah lithium pack at 25°C, a 150A charger achieves 80% charge in 40 minutes. Pro Tip: Install ambient heaters in cold storage facilities to maintain 15–25°C charging zones.
What safety protocols prevent charger hazards?
Key protocols include ground-fault detection, ventilation for hydrogen off-gassing (lead-acid), and spark-proof connectors. Chargers in Class I Div 2 areas must meet ATEX/IECEx standards. Lithium systems require fail-safe BMS communication—interrupted data lines should halt charging instantly. Water-cooled chargers minimize explosion risks in dusty environments.
Practically speaking, operators must check cable insulation weekly—frayed wires can short 80V+ systems. Hydrogen sensors are non-negotiable in enclosed spaces; concentrations over 4% become explosive. Did you know a single lead-acid battery charge cycle releases 0.45m³ of hydrogen? Redway’s chargers integrate gas dispersion fans, cutting peak levels by 60%. Always wear PPE—thermal runaway events can reach 800°C in seconds.
What Is Standard Forklift Fork Spacing?
Redway Battery Expert Insight
FAQs
No—forklift batteries demand higher current (100A+) and specialized algorithms. Car chargers lack hydrogen venting controls, risking explosions in industrial settings.
Is overnight charging safe?
Only with auto-shutoff chargers. Lead-acid systems left on trickle charge over 12h suffer water loss. Lithium BMS systems mitigate risks, but periodic monitoring is advised.
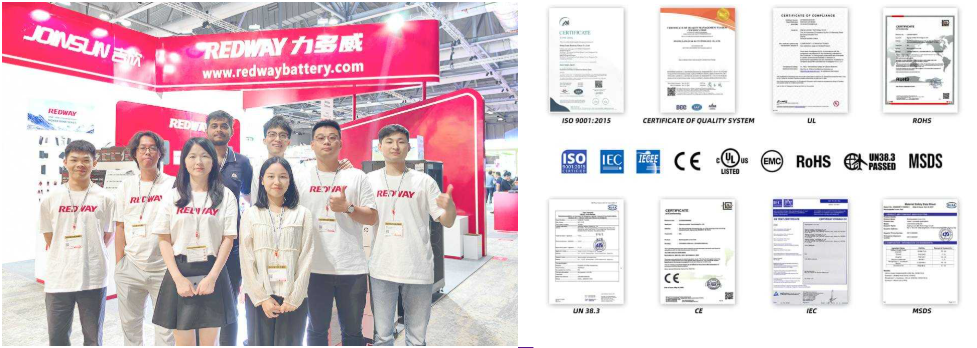