Forklift battery data covers types (lead-acid, lithium-ion), capacities (100–1,200Ah), maintenance protocols, charging cycles, safety standards (OSHA, UL), and lifespan factors. Lead-acid dominates for cost, while lithium offers 3x cycle life and faster charging. Voltages range from 24V (pallet jacks) to 80V (heavy lifts). Always prioritize thermal monitoring in lithium packs and equalize lead-acid monthly. Proper watering schedules and SOC management prevent sulfation.
How Much Do Different Forklift Batteries Weigh by Type?
What Are the Common Types of Forklift Batteries?
Lead-acid (FLA/VRLA) and lithium-ion (LiFePO4/NMC) dominate. Flooded lead-acid (FLA) requires watering but offers 1,500+ cycles at 50% DoD. VRLA (AGM/gel) reduces maintenance. Lithium packs hit 3,000–5,000 cycles with 95% efficiency. NiCd batteries persist in cold storage but face phaseouts.
Wholesale lithium golf cart batteries with 10-year life? Check here.
FLA batteries use 24V–48V configurations with specific gravities of 1.265–1.280. Their 18–24 month lifespan hinges on equalization charging to prevent stratification. Lithium-ion variants, however, operate at 25.6V–51.2V (nominal) with built-in Battery Management Systems (BMS) for cell balancing. Pro Tip: Deploy lithium in multi-shift operations—30-minute fast charging slashes downtime. For example, a 48V 600Ah lithium pack delivers 28.8kWh, powering 8-hour shifts in 3,000kg capacity forklifts.
Beyond chemistry, battery compartments must align with forklift weight limits. Did you know a 36V 800Ah lead-acid battery weighs ~1,100kg versus 550kg for lithium? Tables often clarify this:
Want OEM lithium forklift batteries at wholesale prices? Check here.
Type | Cycle Life | Energy Density |
---|---|---|
FLA | 1,500 | 30–40 Wh/kg |
LiFePO4 | 3,500 | 90–120 Wh/kg |
How Do Forklift Battery Capacities Impact Performance?
Higher Ah ratings extend runtime but add weight. A 600Ah battery at 48V provides 28.8kWh, lasting 6–8 hours under 400A loads. Oversizing increases initial cost but reduces daily charge cycles. Undersized packs force partial State of Charge (SoC), degrading lead-acid twice as fast.
Capacity needs depend on load weight, shift duration, and charging windows. A 1,000kg forklift moving pallets 6 hours/day typically needs 48V 500Ah. Lithium handles partial charges better—topping up during breaks without memory effect. But what happens if you pair a 300Ah battery with a 2,000kg lift? Voltage sags below 20% SoC strain motors. Pro Tip: Match Ah to ampere-hour throughput—calculate (Shift Hours × Avg Current) + 20% buffer. For example, 400A average over 5 hours requires 2,000Ah + 400Ah buffer. Transitional phases matter too: Cold storage (-20°C) slashes lead-acid capacity by 30% but only 15% in lithium.
What Maintenance Practices Extend Forklift Battery Life?
Lead-acid needs weekly watering, terminal cleaning, and monthly equalization. Lithium requires BMS updates, firmware checks, and avoiding storage at 100% SoC. Both types need ambient temperatures below 40°C and post-operation cooldowns.
For FLA, use distilled water only—tap minerals corrode plates. Check electrolyte levels after charging when fluid expands. VRLA batteries shouldn’t be watered but need vent cleaning to prevent thermal runaway. Practically speaking, a missed equalization cycle can cause stratification, where acid concentration varies vertically. Lithium’s BMS automates cell balancing, but manual capacity tests every 500 cycles spot degradation. Did you know 70% of premature failures stem from improper charging? Always use chargers with temperature sensors—overheating during charging reduces life by 30%.
How Does Charging Protocol Affect Battery Efficiency?
CC-CV charging optimizes lithium, while lead-acid needs bulk/absorption/float stages. Fast-charging lithium at 1C (1 hour) cuts cycles by 15% versus 0.5C (2 hours). Lead-acid requires 8+ hours to avoid gassing.
Fast-charging lithium-ion at high currents (200A+) demands liquid cooling—a 48V 600Ah pack hits 45°C otherwise. Lead-acid chargers must taper voltage after 80% SoC to minimize water loss. For example, a 48V FLA battery charges at 58V bulk, 56V absorption, then 54V float. Pro Tip: Use opportunity charging for lithium—partial top-ups extend daily uptime. But what if you use a lithium charger on lead-acid? Overvoltage corrodes plates in weeks. Transitioning to smart chargers with chemistry detection prevents this. Table below contrasts protocols:
Parameter | Lead-Acid | Lithium |
---|---|---|
Charge Time | 8–10h | 1–3h |
Efficiency | 70–80% | 95–98% |
Understanding Forklift Battery State of Charge
Redway Battery Expert Insight
FAQs
Usually yes, but check compartment dimensions and weight limits—lithium is 50% lighter, potentially altering forklift balance.
How often should lead-acid batteries be watered?
Every 5–10 cycles, post-charging, to cover plates by 1/4 inch. Underwatering exposes plates, causing irreversible sulfation.
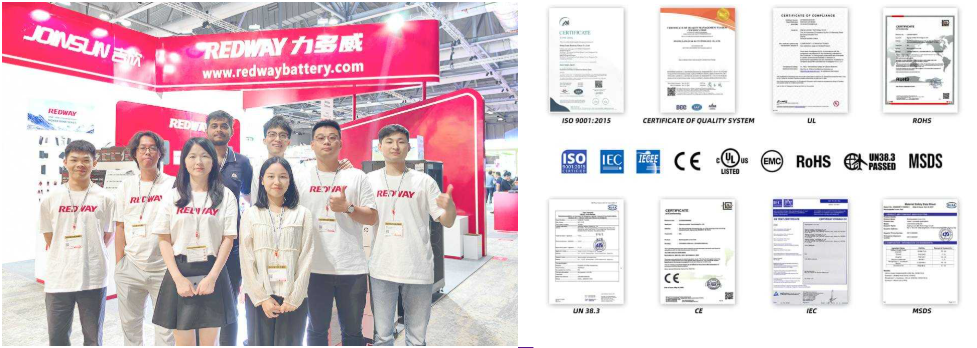