Forklift batteries are specialized power sources designed for material handling equipment, typically using lead-acid or lithium-ion chemistries. Voltage ranges from 24V to 80V, with capacity (100–1200Ah) determining runtime. Regular maintenance—like electrolyte checks and terminal cleaning—is critical. Charging protocols vary: lead-acid requires water replenishment, while lithium-ion uses CC-CV cycles. Always match battery specs to forklift OEM requirements.
How Much Do Different Forklift Batteries Weigh by Type?
What types of forklift batteries are common?
Two primary types dominate: flooded lead-acid (FLA) and lithium-ion (LiFePO4). FLA offers affordability but demands frequent maintenance. Lithium-ion provides faster charging, longer lifespan, and zero maintenance. Niche options include nickel-iron for extreme temperatures. Pro Tip: Choose lithium-ion if operational uptime is critical—they recharge during breaks without damage.
Wholesale lithium golf cart batteries with 10-year life? Check here.
Forklift batteries aren’t one-size-fits-all. Lead-acid models dominate due to lower upfront costs ($2,000–$8,000) but require weekly watering and 8-hour cooldowns. Lithium-ion packs ($12,000–$25,000) eliminate watering and handle partial charges, boosting productivity. For example, a 48V 600Ah LiFePO4 battery can recharge 80% in 1.5 hours vs. 8+ hours for FLA. Battery weight also varies: a 36V 600Ah FLA weighs ~2,200 lbs, while lithium-ion equivalents are 30% lighter. Always verify forklift chassis compatibility—exceeding weight limits risks stability issues. Transitional tech like hydrogen fuel cells exist but remain rare in warehouses.
Type | Cycle Life | Energy Density |
---|---|---|
Lead-Acid | 1,500 cycles | 30–40 Wh/kg |
LiFePO4 | 3,000–5,000 cycles | 90–120 Wh/kg |
How long do forklift batteries last?
Lifespan depends on chemistry and usage. Lead-acid lasts 3–5 years (1,500 cycles), while lithium-ion exceeds 10 years (3,000+ cycles). Deep discharges below 20% SOC accelerate degradation. Pro Tip: Track cycle counts via BMS—replace when capacity drops below 80%.
Want OEM lithium forklift batteries at wholesale prices? Check here.
Imagine your forklift battery as a car engine—regular oil changes (maintenance) prolong its life. Lead-acid batteries degrade faster if discharged below 50% frequently, while lithium-ion tolerates 80% DoD. For instance, a warehouse running two shifts might kill a lead-acid battery in 2 years, whereas lithium-ion lasts 5+. Key factors: ambient temperature (ideal: 77°F), charging patterns, and voltage consistency. Equalization charges every 10 cycles for FLA prevent sulfation. But why does heat matter? High temps increase lead-acid water loss and corrode plates. Lithium-ion handles heat better but still suffers above 113°F.
How to charge forklift batteries correctly?
Use OEM-approved chargers with voltage matching the battery. Lead-acid requires full charges to prevent stratification; lithium-ion thrives on partial top-ups. Always cool batteries pre-charging to avoid thermal runaway.
Charging a forklift battery isn’t like plugging in a phone. Lead-acid needs an 8-hour absorption charge after reaching 80% to mix electrolytes. Interrupting this causes stratification—sulfuric acid settles, reducing capacity. Conversely, lithium-ion’s BMS manages charge curves, allowing opportunity charging during lunch breaks. For example, a 48V lithium pack can charge from 30% to 80% in 45 minutes. But what if you use a lead-acid charger on lithium? Overvoltage triggers BMS shutdowns, halting operations. Always verify charger-battery compatibility. Pro Tip: Install infrared thermometers on charging ports—abnormal temp spikes signal cell failures.
Forklift Battery Charging Station: A Comprehensive Guide
What maintenance ensures battery longevity?
Monthly cleaning of terminals, electrolyte checks (FLA), and SOC monitoring. Lithium-ion needs firmware updates and occasional cell balancing.
Think of forklift battery maintenance like dental care—skip it, and you’ll pay painfully later. For FLA: check water levels weekly (use distilled only), clean vents, and inspect for cracks. Terminal corrosion—a white/green powder—increases resistance, causing voltage drops. Apply anti-corrosion spray after cleaning. Lithium-ion systems need less hands-on work but require BMS software updates to optimize charge algorithms. A real-world example: A logistics center reduced FLA replacement costs by 40% after implementing monthly voltage logging. Transitionally, some fleets use telematics for real-time health tracking—predictive alerts cut downtime by 15%.
Task | Lead-Acid | Lithium-Ion |
---|---|---|
Watering | Weekly | Never |
Cleaning | Monthly | Quarterly |
What safety risks exist with forklift batteries?
Hydrogen gas (explosive) from FLA charging, acid spills, and improper handling causing arc flashes. Lithium-ion risks include thermal runaway if punctured.
Why do warehouses forbid smoking near charging stations? FLA batteries emit hydrogen—a spark can cause explosions. Ventilation systems must exchange air 12+ times per hour. Acid spills require immediate neutralization with baking soda. Lithium-ion hazards differ: physical damage to cells can trigger fires reaching 1,800°F. A pallet mishap in a Texas warehouse once pierced a lithium pack, activating sprinklers. Always use approved PPE—gloves and face shields during maintenance. Pro Tip: Store backup spill kits near charging areas—response time matters.
Redway Battery Expert Insight
FAQs
Lead-acid electrolytes freeze below -40°F, cracking cases. Lithium-ion operates down to -4°F but loses 20% capacity.
How often should I water lead-acid batteries?
Check weekly—top up with distilled water post-charging to avoid overflows. Never expose plates.
Are forklift batteries recyclable?
Yes—98% of lead-acid components are recycled. Lithium-ion recovery rates exceed 70% through specialty programs.
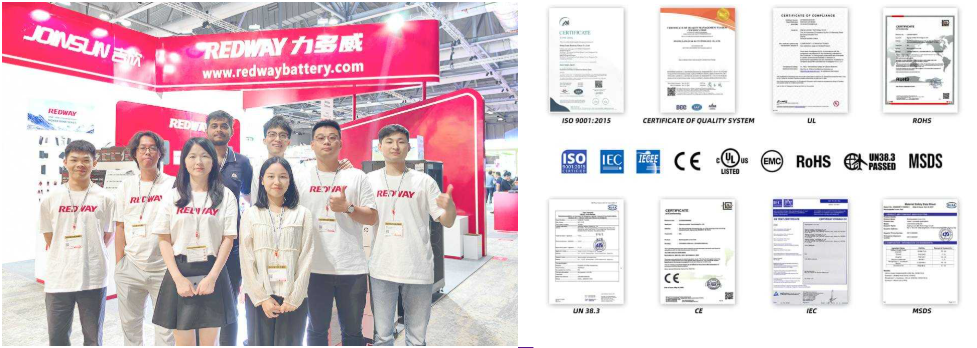