Forklifts for metal foundries are ruggedized, heat-resistant vehicles engineered to handle extreme temperatures (up to 120°C), molten metal splashes, and heavy industrial loads. Key brands like Hyster, Yale, and Toyota offer models with enclosed compartments, explosion-proof certifications (e.g., UL 1203), and specialized non-conductive tires. These forklifts prioritize durability, with stainless steel components and advanced cooling systems for continuous operation in hazardous foundry environments. Pro Tip: Always verify temperature ratings match your furnace zones to prevent hydraulic fluid degradation.
What Are Forklift Battery Cell Sizes?
What defines a foundry-grade forklift?
Foundry forklifts feature heat-shielded engines, Class III explosion-proofing, and reinforced steel frames. Unlike standard models, they resist temperatures above 100°C and molten debris via enclosed electrical systems and ceramic thermal coatings.
Wholesale lithium golf cart batteries with 10-year life? Check here.
Foundry environments demand forklifts that won’t ignite combustible dust or warp under radiant heat. For instance, Hyster’s H16XM-ED includes a liquid-cooled engine compartment reducing internal temps by 30% versus air-cooled units. Pro Tip: Insist on IP67-rated seals to prevent molten metal ingress into critical components. Hydraulic hoses should withstand 150°C+—check for PTFE linings and stainless steel braiding. One real-world example: A 10-ton Yale ERP45VF-ACEA moves cast iron molds at 950°C furnaces daily, using zinc-plated forks to resist warping. But why risk standard tires? Foundries require non-marking, heat-resistant rubber (e.g., Viton) to prevent melting near crucibles.
What design features prevent foundry forklift failures?
Critical designs include enclosed brake systems, spark-resistant alternators, and liquid-cooled hydraulics. These prevent ignition risks and ensure functionality amid airborne particulates and high humidity.
Want OEM lithium forklift batteries at wholesale prices? Check here.
Beyond heat management, foundry forklifts use positive-pressure cabins with HEPA filtration to protect operators from metal fumes. Take the Toyota 8FGCU25: Its triple-sealed mast bearings block abrasive foundry sand, extending service intervals by 200 hours. Pro Tip: Opt for drum instead of disc brakes—less prone to warping from thermal shock. An analogy? Think of these forklifts as industrial-grade “armored vehicles,” combining fire resistance (like ceramic bulkheads) with impact protection (4x thicker chassis plating). Transitioning to components, stainless steel piston rods in lift cylinders outperform standard chrome rods when exposed to sulfurous gases.
Feature | Standard Forklift | Foundry Forklift |
---|---|---|
Temperature Rating | 40°C max | 120°C sustained |
Tire Material | Standard rubber | Viton/Non-marking |
Electrical Safety | IP54 | IP67/Explosion-proof |
How do load capacities differ in foundry forklifts?
Foundry models support 8,000–36,000 lbs loads, using reinforced mast channels and dual stabilizer bars. Standard forklifts often cap at 10,000 lbs and lack lateral reinforcement for uneven mold handling.
High-capacity foundry forklifts like the Cat FC45Z integrate box-section carriages that resist torsional stress when lifting irregular ingots. Practically speaking, overloads here aren’t just about weight—it’s load stability. Pro Tip: Specify 48” fork spreads for wide molds; standard 36” setups risk tipping. Consider the Crown RC 5500: Its 24,000 lb capacity handles 2-ton crucibles, but adding a sideshifter adds 18% stability. Did you know? Foundry forklifts often include dual rear wheels—a 20% larger contact patch prevents sinkage in soft slag floors.
Why are power sources critical in foundry forklifts?
Explosion-proof diesel engines dominate due to high torque and heat tolerance. Electric models require ATEX-certified batteries with thermal runaway prevention—seldom used near open furnaces.
Internal combustion engines (ICEs) thrive here, as lithium-ion batteries risk thermal events above 60°C. For example, Cummins’ QSL9 diesel in Clark CMP50 units delivers 325 HP, crucial for moving 30-ton ladles uphill. But what about emissions? Many foundries retrofit ICEs with diesel particulate filters (DPFs) meeting EPA Tier 4 norms. Pro Tip: Avoid LPG—propane tanks risk explosions if radiant heat exceeds 80°C. Transitioning to electric? Only consider Toshiba’s SCiB titanium batteries with 120°C operating limits, paired with pressurized battery compartments.
Power Type | Advantages | Foundry Limitations |
---|---|---|
Diesel | High torque, heat-resist | Emissions scrubbing needed |
Electric | Low noise | Battery cooling challenges |
LPG | Clean burn | Tank explosion risks |
Redway Battery Expert Insight
FAQs
Rarely—retrofitting costs exceed 70% of new units. Foundry specs require factory-integrated thermal shielding and explosion-proof wiring harnesses.
Are explosion-proof certifications mandatory?
Yes—OSHA mandates NEC 495/ATEX compliance for equipment within 10m of molten metal. Fines exceed $50k for violations.
Which tire type suits foundry floors?
Non-marking, solid Viton tires—avoid pneumatics. Michelin’s XHA2 compound resists melting up to 150°C, lasting 2x longer near furnaces.
How Much Does a Forklift Battery Weigh?
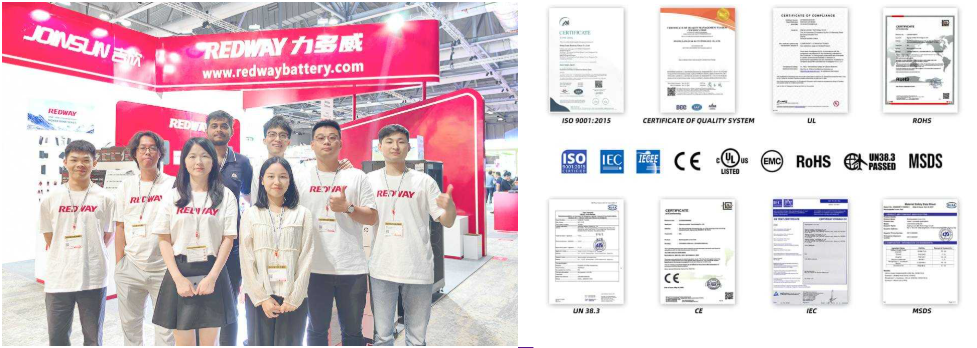