The most economical forklift batteries are lead-acid (flooded or AGM) due to lower upfront costs (40-50% cheaper than lithium), while lithium-ion (LiFePO4) offers long-term savings via 3-4x longer lifespan and zero maintenance. Lead-acid suits low-usage operations (≤6 hours/day), whereas lithium excels in multi-shift applications. Pro Tip: Factor in energy efficiency—lithium’s 95% charge efficiency saves $200+/year vs. lead-acid’s 70%.
Forklift Battery Charging Station: A Comprehensive Guide
What’s the cost difference between lead-acid and lithium forklift batteries?
Lead-acid costs $3,000–$6,000 upfront vs. lithium’s $8,000–$20,000. However, lithium lasts 10–15 years (vs. 3–7 for lead-acid) with minimal maintenance. Energy savings (15–30% less charging) and labor reductions (no watering) offset higher initial costs in 2–4 years for high-use cases.
Wholesale lithium golf cart batteries with 10-year life? Check here.
Let’s break it down: A 48V 600Ah lead-acid battery costs ~$6,000 but requires $1,200/year in maintenance and replacement every 5 years. Comparatively, lithium at $15,000 lasts 12 years with $200/year savings. Over a decade, lithium’s TCO is $17,400 vs. lead-acid’s $18,000. Pro Tip: Use lithium if daily runtime exceeds 8 hours—lead-acid deep cycles degrade 2x faster beyond 50% DoD. For example, Amazon warehouses saved $4.2M annually by switching 200 forklifts to lithium.
Type | Upfront Cost | Lifespan |
---|---|---|
Flooded Lead-Acid | $3,000–$5,000 | 3–5 years |
AGM Lead-Acid | $4,000–$6,500 | 5–7 years |
LiFePO4 | $10,000–$20,000 | 10–15 years |
How does battery lifespan impact economy?
Longer lifespan reduces replacement costs. Lead-acid requires 2–3 replacements to match lithium’s single lifespan, adding $9,000–$15,000 in cumulative costs. Lithium also maintains 80% capacity after 3,000 cycles vs. lead-acid’s 1,200 cycles. Fast charging (1–2 hours for lithium) further reduces downtime costs.
Want OEM lithium forklift batteries at wholesale prices? Check here.
Practically speaking, forklift operators lose $50–$100/hour during battery swaps. Lithium’s opportunity costs are 75% lower due to rapid charging and no watering. Pro Tip: Use lithium’s state-of-charge monitoring to avoid partial charging—lead-acid suffers sulfation if not fully charged weekly. A real-world example: Coca-Cola’s bottling facility reduced 300 weekly labor hours by eliminating lead-acid watering. But what if your fleet operates only 2–3 hours daily? Lead-acid’s lower initial investment might still dominate.
Do maintenance requirements affect long-term costs?
Yes—lead-acid needs weekly watering, equalization, and terminal cleaning, costing $1,000–$3,000/year per forklift. Lithium requires no maintenance, with sealed designs and automatic BMS. AGM batteries cut watering costs but still need monthly voltage checks.
Beyond labor, consider acid spills and ventilation. Lead-acid charging emits hydrogen, requiring $5,000–$10,000 in ventilation systems. Lithium’s closed-loop charging works in confined spaces. Pro Tip: Train staff on proper watering—underfilled lead-acid cells lose 30% capacity prematurely. For example, Walmart cut maintenance costs by 62% post-lithium adoption, but small warehouses with infrequent use still find lead-acid manageable.
When is each battery type most cost-effective?
Lead-acid suits single-shift operations (≤6 hours) with stable budgets. Lithium dominates multi-shift, high-intensity environments. Nickel-cadmium (NiCd) remains niche for extreme temperatures (-40°C to +60°C), though 40% pricier than lithium.
Seasonal businesses, like holiday warehouses, benefit from lead-acid’s flexibility. Conversely, e-commerce fulfillment centers running 24/7 achieve ROI on lithium in 18 months. Pro Tip: Lease lead-acid batteries if cash flow is tight—$100–$300/month vs. lithium’s $400–$800. But what about peak shifts? Lithium’s 15-minute opportunity charging handles demand spikes without downtime, whereas lead-acid needs 8-hour cooldowns.
Scenario | Optimal Battery | Annual Cost per Truck |
---|---|---|
Single shift (5 days/week) | Lead-acid | $3,200 |
Multi-shift (24/5) | Lithium | $5,100 |
Freezer storage (-30°C) | NiCd | $8,700 |
How do government incentives affect battery economics?
Tax credits (e.g., U.S. ITC) and EV subsidies can slash lithium costs by 20–30%. California’s LCFS offers $500–$1,000 per ton of CO2 reduced. Lead-acid rarely qualifies due to lower efficiency. Always check local programs—Canada’s SGIP grants cover 35% of lithium upgrades.
Pro Tip: Partner with vendors offering incentive-assisted leasing—Redway Battery’s program reduces lithium’s upfront cost by 50% in eligible regions. For instance, a Texas logistics firm secured $12,000/unit rebates for 50 lithium forklifts. But aren’t incentives temporary? Yes—lock in rates before programs expire, as seen with the 2023 EU Battery Directive phaseouts.
Redway Battery Expert Insight
Redway Battery prioritizes LiFePO4 for heavy-duty forklifts due to 10,000+ cycle lifespans and modular designs enabling easy capacity upgrades. Our batteries integrate ISO 13849-certified BMS for thermal safety and adaptive charging curves that extend cell life by 20% vs. industry standards, delivering ROI within 18 months for high-throughput operations.
FAQs
Only if daily use exceeds 4 hours—otherwise, lead-acid’s lower TCO suffices. Lithium’s break-even point is ~800 cycles/year.
Can I retrofit lithium into older forklifts?
Only with voltage-matched BMS (e.g., 48V LiFePO4 for 48V systems). Never force 48V lithium into 36V trucks—motor burnout risks are high.
Are lithium forklift batteries safer?
Yes—no acid leaks or hydrogen emissions. Redway’s LiFePO4 batteries include UL-recognized flame-retardant casings and short-circuit protection.
Can Forklift Batteries Be Used for Home Solar?
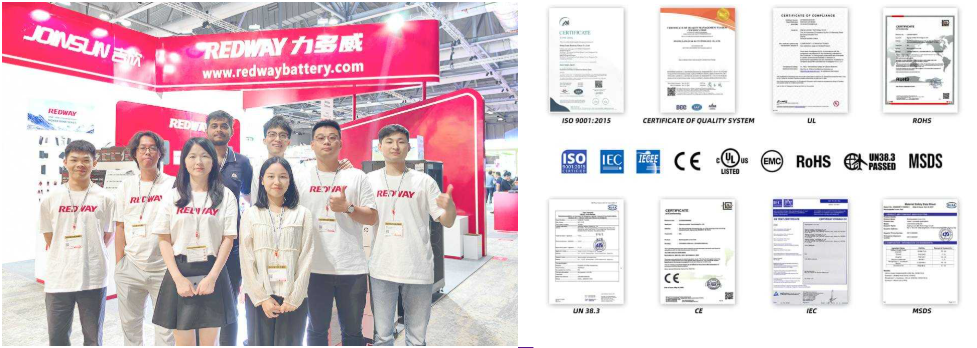