Forklift battery sizing depends on voltage (typically 24V, 36V, 48V), capacity (Ah), and physical dimensions. Common configurations include 24V200Ah for light-duty models like Linde L10, 48V600Ah for heavy-duty units like Heli CPD18, and lithium upgrades (e.g., 25.6V300Ah). Brands like Toyota and TCM require cell spacing compatibility, while lead-acid replacements must match tray sizes. Pro Tip: Always verify charging system compatibility—higher Ah batteries demand proportional charger current upgrades.
How Much Do Different Forklift Batteries Weigh by Type?
What voltage standards govern forklift batteries?
Forklift batteries align with equipment power needs—light 1-3 ton models use 24V or 36V (e.g., BT Reflex), while 48V-80V systems power 5-10 ton loads. Lithium variants often employ 25.6V/51.2V to match lead-acid equivalents. Voltages directly affect motor torque—underpowered packs cause sluggish operation.
Wholesale lithium golf cart batteries with 10-year life? Check here.
Most electric forklifts operate on 24V, 36V, or 48V DC systems. For instance, Linde’s T20 uses 24V345Ah batteries, whereas Heli CPD25 requires 48V630Ah. Lithium conversions maintain voltage parity: 25.6V lithium packs replace 24V lead-acid units. Transitionally, voltage mismatches cause controller failures—never pair 36V batteries with 48V systems without DC-DC conversion. Pro Tip: Measure voltage under load—resting voltage can falsely indicate 2-3V higher than operational levels. Real-world example: A 48V600Ah lead-acid battery provides 28.8kWh, enabling 6-8 hours in 3-ton forklifts.
How does battery capacity (Ah) vary by forklift class?
Capacity ranges span 200Ah-1200Ah: 24V200Ah suits 1.5-tonners like Noli CPD15, while 48V1150Ah powers 10-ton giants. Ah dictates runtime—50% discharge cycles optimize lead-acid lifespan.
Want OEM lithium forklift batteries at wholesale prices? Check here.
Forklift battery capacity directly correlates with equipment class. Small warehouse stackers (1-2 ton) typically use 24V165Ah-24V280Ah packs, providing 4-5 hours per charge. Medium-duty 3-5 ton models require 48V400Ah-48V600Ah, delivering 6-8 hours. Heavy 8-10 ton forklifts demand 48V700Ah+ configurations. However, beyond capacity, consider C-rating—many lead-acid batteries only support 5-hour discharge (C5 rating). Transitionally, upgrading from 420Ah to 600Ah requires physical space verification—larger capacities often mean bigger cells. For example, replacing a CPD15’s 420Ah battery with 600Ah may require modifying battery compartments. Pro Tip: Lithium alternatives offer 100% DoD (Depth of Discharge), effectively doubling usable capacity versus lead-acid’s 50% limit.
Forklift Class | Typical Voltage | Capacity Range |
---|---|---|
1-2 ton | 24V | 165-280Ah |
3-5 ton | 48V | 400-700Ah |
8-10 ton | 80V | 575-1150Ah |
Which brands require specialized battery formats?
Proprietary formats exist for Linde (48V700Ah), TCM (48V480Ah), and Toyota (24V225Ah). GS Yuasa’s VGD series uses unique cell spacing incompatible with generic trays.
Certain forklift manufacturers require bespoke battery designs. Linde’s H20D-T hybrid models need 48V700Ah packs with dual terminals for auxiliary systems. TCM’s FD70 demands 48V480Ah batteries with 315mm cell spacing, differing from standard 400mm layouts. Japanese models like Toyota 8FGU25 use 24V225Ah configurations with side-terminal connections. Transitionally, third-party batteries may physically fit but lack required BMS protocols—Toyota System of Active Stability (SAS) won’t recognize non-OEM lithium packs. Real-world example: GS Yuasa’s VGD620 battery (620Ah) has 426mm width, requiring custom trays in older Hyster lifts. Pro Tip: Always request CAD drawings when retrofitting batteries to verify terminal alignment.
When should you consider lithium battery conversions?
Lithium upgrades benefit high-use operations needing 2,000+ cycles. Lead-acid to 25.6V300Ah lithium swaps save 40% weight while doubling lifespan.
Lithium-ion conversions become viable when lead-acid replacement costs exceed $3,000 annually. Operations with multi-shift patterns gain most—lithium supports opportunity charging (10-20 minute top-ups). For instance, converting a 48V600Ah lead-acid system to 51.2V300Ah lithium reduces weight by 900kg while maintaining runtime. Transitionally, lithium’s flat discharge curve maintains full power until 10% SOC, unlike lead-acid’s voltage sag. However, existing charging infrastructure often needs upgrades—a 48V lead-acid charger’s 60A output takes 10 hours to refill 600Ah, whereas lithium can accept 100A+ for 6-hour charges. Pro Tip: Verify BMS compatibility—some forklift controllers require CAN communication for SOC display.
Parameter | Lead-Acid | Lithium |
---|---|---|
Cycle Life | 1,200 | 3,000+ |
Charge Time | 8-10h | 2-4h |
Energy Density | 30-40Wh/kg | 100-150Wh/kg |
What charger specifications match battery capacity?
Chargers must deliver 10-13% of battery Ah: 600Ah packs need 60-78A output. Mismatched currents cause sulfation (lead-acid) or BMS faults (lithium).
Charger selection follows C-rate guidelines. For lead-acid, C10 is standard—a 600Ah battery requires 60A charger (600 ÷ 10). High-frequency chargers can push to C8 (75A) for faster cycles. Lithium tolerates up to 1C charging—300Ah pack with 300A input. Transitionally, oversized chargers for lead-acid cause overheating, while undersized units induce memory effects. Example: A 48V600Ah battery upgraded from 60A to 80A charging reduces refill time from 10 to 7.5 hours. However, cable gauges must handle increased current—6 AWG replaces 8 AWG beyond 70A. Pro Tip: Multi-voltage chargers (24V/48V/80V) future-proof fleets mixing equipment classes.
Forklift Battery Charging Station: A Comprehensive Guide
Redway Battery Expert Insight
FAQs
Yes, with voltage calibration—lithium’s 51.2V nominal vs. lead-acid’s 48V requires controller reprogramming to prevent overvoltage errors.
How do I calculate battery runtime?
Runtime (h) = Battery Ah × Voltage × 0.85 (inefficiency) ÷ Motor kW. Example: 48V600Ah ÷ 10kW ≈ 5 hours at 60% load.
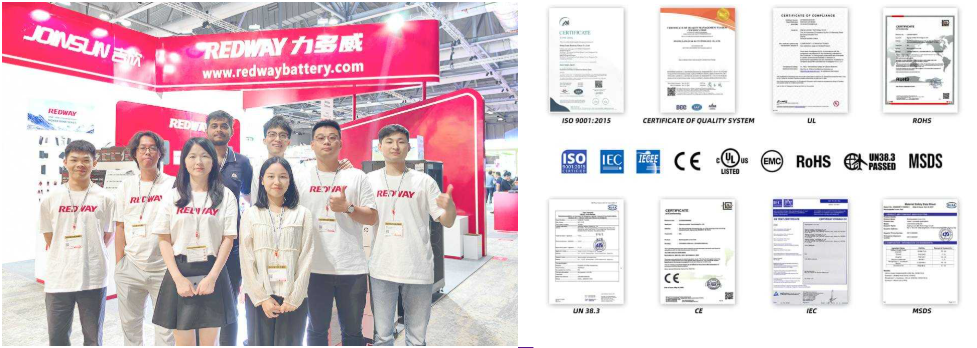