The Hyster E35 XL2 48V 24-85-13 requires a 48V lead-acid or lithium-ion traction battery matching its compartment dimensions (L24″ x W33″ x H35.5″), weight capacity (~2000–2500 lbs), and terminal placement. OEM specs often use 24-85-13 to denote cell layout (24 cells, 85Ah per cell, 13-plate design) for 48V systems. Third-party alternatives must align with voltage, dimensions, and BMS compatibility to ensure safe operation.
How Much Does a Forklift Battery Weigh?
What does the “24-85-13” code signify in Hyster E35 batteries?
The 24-85-13 identifier refers to the battery’s cell count (24 cells for 48V), Ah capacity per cell (85Ah), and plate configuration (13 plates per cell). This design ensures 4.08kWh total energy (48V × 85Ah), optimized for Hyster’s motor controllers. Always verify these metrics when replacing to avoid underpowering or compartment fit issues.
Wholesale lithium golf cart batteries with 10-year life? Check here.
Deep Dive: Hyster’s 24-cell battery arranges 2V lead-acid cells in series (24×2V=48V), with each cell containing 13 lead plates submerged in sulfuric acid. The 85Ah rating indicates a 5-hour discharge capacity—critical for shift-long operation. Pro Tip: Avoid mismatched Ah ratings; lower Ah reduces runtime, while higher Ah risks overloading chargers. For example, a Hyster E35 using an 85Ah battery typically operates 6–8 hours per charge. Lithium-ion upgrades (e.g., 100Ah LiFePO4) require BMS adjustments to handle voltage curves. But what happens if you ignore cell count? Using 22 cells (44V) starves the motor, while 26 cells (52V) may fry controllers.
Can lithium-ion batteries replace OEM lead-acid in Hyster E35 XL2?
Yes, lithium-ion batteries like LiFePO4 can replace lead-acid in the E35 XL2 if they match voltage (48V), dimensions, and communication protocols. Lithium packs offer 2–3x cycle life (3,000+ cycles) and 50% faster charging but require upgraded charging infrastructure and BMS integration.
Want OEM lithium forklift batteries at wholesale prices? Check here.
Deep Dive: Swapping lead-acid for lithium-ion in the Hyster E35 involves more than plug-and-play. Beyond matching voltage and physical size, the forklift’s onboard computer may need firmware updates to interpret lithium’s flat discharge curve (lead-acid voltage drops linearly). Practically speaking, a 48V 100Ah LiFePO4 battery cuts weight by 40% (from 2,200 lbs to ~1,300 lbs), freeing up payload capacity. Redway Battery’s custom solutions, for instance, include CAN-BUS integration to sync with Hyster’s diagnostic systems. Pro Tip: Opt for lithium with IP67 ratings to withstand warehouse debris. But why isn’t lithium a universal fix? Upfront costs are 2–3x higher, and some facilities lack 240V charging stations needed for rapid lithium charging.
Factor | Lead-Acid | Lithium-Ion |
---|---|---|
Cycle Life | 1,500 cycles | 3,000+ cycles |
Charge Time | 8–10 hours | 3–4 hours |
Weight | 2,200 lbs | 1,300 lbs |
How do Hyster E35 battery dimensions affect replacements?
The Hyster E35 XL2 compartment requires 24″ length x 33″ width x 35.5″ height batteries. Third-party units deviating by ±0.5″ risk misalignment, terminal interference, or compromised stability during lifting. Weight distribution must also mimic OEM specs (1,800–2,500 lbs) to prevent forklift imbalance.
Deep Dive: Forklift battery compartments are precision-engineered for load distribution. A lithium-ion battery 1″ narrower than OEM specs, for example, might shift during sharp turns, destabilizing the E35. Beyond physical fit, terminal placement (left vs. right, top vs. front) must match the existing wiring harness. Consider a warehouse case: a 24x33x35.5″ lead-acid battery with front terminals couldn’t connect to a replacement using top terminals without costly rewiring. Pro Tip: Use CAD models from suppliers to verify fitment digitally. Why does weight matter? Lighter lithium batteries may require ballast to maintain the E35’s center of gravity—always consult Hyster’s engineering guidelines.
What’s the cost difference between OEM and aftermarket batteries?
OEM Hyster batteries cost $8,000–$12,000, while aftermarket lead-acid ranges from $5,000–$9,000. Lithium-ion replacements span $12,000–$20,000 but offer long-term savings via reduced maintenance and 2x lifespan. Always factor in warranty coverage (OEM: 2–3 years, third-party: 1–5 years).
Deep Dive: Hyster’s OEM batteries include proprietary software integration and guaranteed fitment but come at a premium. Aftermarket options, like those from East Penn or GS Yuasa, may lack BMS compatibility, risking error codes. For example, a $7,000 third-party lead-acid battery with 1,200 cycles saves $3,000 upfront but costs more per cycle ($5.83 vs. OEM’s $6.67). Lithium-ion’s $20,000 price tag seems steep, but over 10 years, it’s $2,000/year versus lead-acid’s $4,000/year (with two replacements). Pro Tip: Lease lithium batteries to offset upfront costs—some vendors offer $300/month plans. But what about hidden fees? Third-party batteries may void Hyster’s powertrain warranty; always get written confirmation.
Type | Upfront Cost | 10-Year Cost |
---|---|---|
OEM Lead-Acid | $10,000 | $30,000 |
Third-Party Lead-Acid | $7,000 | $21,000 |
Lithium-Ion | $20,000 | $20,000 |
Understanding Forklift Battery State of Charge: A Complete Guide
Redway Battery Expert Insight
FAQs
Yes, but only if the charger supports it. A 100Ah battery requires a 50A charger (0.5C rate) versus the stock 42.5A (0.5C for 85Ah). Exceeding charger limits risks overheating.
Do lithium batteries work in cold warehouses?
Yes, but LiFePO4 performs best at -4°F to 140°F. Below -4°F, capacity drops 20–30%; use thermal blankets for sub-zero environments.
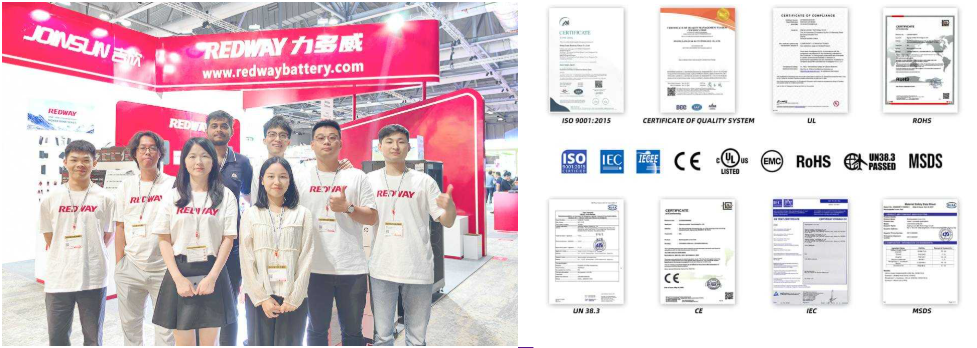