Tough attachments for Hyster forklifts are specialized add-ons made from hardened steel or alloy, designed to handle extreme loads (3,000–12,000 lbs) and harsh environments like lumber yards or recycling plants. Key types include fork positioners, clamps, and rotators, all engineered to integrate with Hyster’s hydraulic systems (e.g., 20–30 GPM flow rates). Pro Tip: Always verify attachment weight limits match your forklift’s capacity to avoid instability. What Is Standard Forklift Fork Spacing?
What defines a Hyster forklift tough attachment?
Hyster tough attachments are built with hardened steel frames and ISO 2328-compliant mounting, supporting vertical loads up to 12,000 lbs. They’re tested for 500,000+ duty cycles in -20°C to 50°C environments. For example, a paper roll clamp uses 30 GPM hydraulics for 360° rotation—ideal for tightly wrapped loads. Pro Tip: Pair high-pressure attachments (250+ PSI) with Hyster’s XD series for optimal hydraulic flow.
How do fork positioners enhance pallet handling?
Fork positioners adjust tine spacing (12–48 inches) in 3–5 seconds via electric or hydraulic actuators, reducing manual adjustments by 80%. A typical Hyster-compatible model handles 4,500 lbs at 20 GPM, but what if your loads vary? For mixed pallet sizes (e.g., 24″ and 40″), opt for models with position memory presets. Pro Tip: Install fork stops to prevent accidental overextension during side-shifting.
Wholesale lithium golf cart batteries with 10-year life? Check here.
Positioner Type | Max Load | Adjustment Speed |
---|---|---|
Hydraulic | 6,000 lbs | 3 sec |
Electric | 4,500 lbs | 5 sec |
Are hydraulic clamps suitable for fragile loads?
Yes—modern pressure-sensitive clamps with 10–200 PSI adjustable range prevent crushing damage to items like appliances or foam blocks. The Hyster J40-50XD series pairs with rubber-coated clamps exerting 500–1,200 lbs force. Practically speaking, a 48″ drum clamp needs 15 GPM flow to rotate safely. Pro Tip: Use load cells to monitor clamping force in real-time during fragile material handling.
What maintenance ensures attachment longevity?
Beyond weekly visual inspections, perform bi-annual pressure tests on hydraulic lines and check for frame cracks (≥0.5mm tolerance). Replace pivot bushings every 1,500 hours under heavy use. For example, a steel mill’s bale clamp requires monthly cylinder rebuilds due to metal dust ingress. Pro Tip: Keep attachment pins greased with NLGI #2 lithium-based lubricant to reduce wear by 40%.
Want OEM lithium forklift batteries at wholesale prices? Check here.
Maintenance Task | Frequency | Cost Estimate |
---|---|---|
Hydraulic Seal Replacement | 1,000 hrs | $120–$300 |
Frame Alignment Check | 500 hrs | $80–$150 |
Do load stabilizers improve uneven load safety?
Absolutely—stabilizers with dual-axis tilt control (±15°) and auto-leveling reduce load spills by 65% on slopes up to 10%. A Hyster H105-110HD forklift lifting lopsided machinery benefits from stabilizers distributing 80% of off-center weight. But what about sudden shifts? Choose models with inertial sensors triggering instant lock. Pro Tip: Combine stabilizers with spreader bars when lifting asymmetrical steel coils over 8,000 lbs.
Redway Battery Expert Insight
FAQs
Only models with Hyster’s S4/S5 carriage compatibility or aftermarket adapters (e.g., Cascade CL25) rated for 16,000+ lbs. Verify mount spacing (28” or 33.5”) matches your lift’s carriage.
How often inspect tough attachments?
Daily checks for hydraulic leaks and frame stress marks. Use NDT ultrasound annually to detect internal cracks in high-cycle applications.
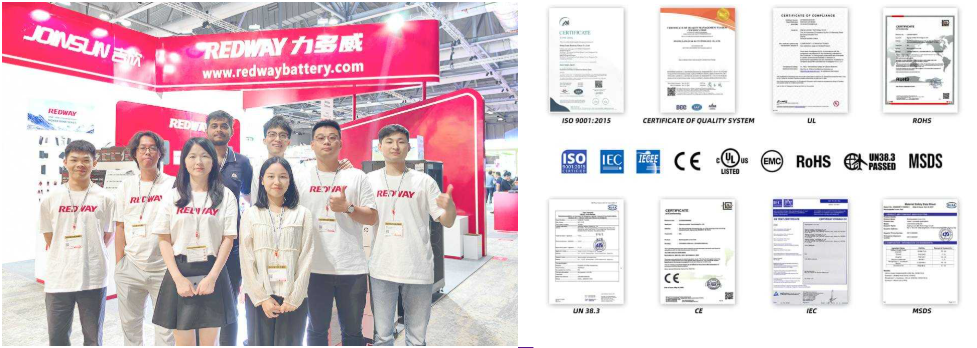