Forklift batteries are robust energy sources designed for heavy-duty material handling. Key features include lead-acid or lithium-ion chemistries, capacities from 200–1200Ah, and voltages of 24V–80V. Built for durability, they prioritize deep-cycle performance, thermal management, and safety compliance (OSHA, UL). Maintenance requirements vary: flooded lead-acid needs watering, while lithium-ion is sealed. Typical lifespan ranges 5–15 years, depending on usage and charging protocols.
What Is Standard Forklift Fork Spacing?
What types of forklift batteries dominate industrial use?
Two primary types prevail: flooded lead-acid (80% market share) and lithium-ion. Lead-acid offers low upfront costs but demands watering/equalization. Lithium variants (LiFePO4) provide maintenance-free operation and 3× faster charging. Nickel-iron batteries exist but are niche due to lower efficiency (65% vs. 95% for lithium).
Wholesale lithium golf cart batteries with 10-year life? Check here.
Forklift batteries are categorized by voltage (24V–80V) and capacity. For example, a 48V 600Ah lead-acid battery weighs ~2,100 lbs, delivering 28.8kWh. Lithium-ion equivalents reduce weight by 40% due to higher energy density (150–200Wh/kg vs. 30–50Wh/kg). Pro Tip: Use lithium-ion in multi-shift operations—they handle partial charging without sulfation damage. Real-world case: Amazon’s warehouses shifted to lithium to eliminate 8-hour lead-acid cool-down periods, boosting productivity 22%.
How does battery capacity affect forklift performance?
Capacity (Ah) determines runtime and load-handling. Higher Ah extends operating hours but increases weight—a 36V 750Ah battery powers 6–8 hours of heavy lifting (3,000–4,500 lbs). However, oversized packs may strain chassis. Lithium’s scalable modules (50Ah increments) allow precise capacity-tuning without weight penalties.
Want OEM lithium forklift batteries at wholesale prices? Check here.
Runtime calculations hinge on the 80% discharge rule. A 48V 500Ah battery provides 500Ah × 48V × 0.8 = 19.2kWh usable energy. Electric forklifts average 1.5–2.5kWh/hour under load, translating to 7.7–12.8 hours. Pro Tip: Monitor voltage sag—if a 36V battery drops below 31V under load, capacity is degrading. Transitional insight: Just as car engines lose horsepower over time, aging batteries suffer reduced peak amperage, slowing lift speeds.
What charging methods optimize forklift battery life?
Lead-acid requires opportunity charging (partial top-ups) but mandates full weekly equalization. Lithium-ion thrives on partial charges (20%–80% SOC) with no memory effect. High-frequency chargers (HF) with 92% efficiency outperform traditional SCR units (78%).
Charger Type | Efficiency | Charge Time (0–80%) |
---|---|---|
SCR | 75–78% | 8–10 hrs |
HF | 90–93% | 2–3 hrs |
For instance, a 48V lithium pack charges from 30%–80% in 1.5 hours using 100A HF systems. Pro Tip: Install temperature sensors—charging lead-acid above 113°F (45°C) accelerates corrosion. Rhetorical question: Why risk thermal stress when smart chargers auto-adjust current based on cell temperatures?
What safety certifications are mandatory for forklift batteries?
Compliance with UL 2580 (electrical vehicle batteries) and OSHA 1910.178(g) is non-negotiable. UL tests cover short-circuit, overcharge, and crush resistance (>200 kN for lithium). Ventilation mandates differ: lead-acid demands 1 CFM/Ah to vent hydrogen, while sealed lithium needs minimal airflow.
Standard | Lead-Acid | Lithium-Ion |
---|---|---|
Ventilation | Required | Optional |
Thermal Cutoff | No | Yes (165°F) |
Real-world example: Tesla’s Gigafactory uses lithium forklifts with IP67 enclosures to withstand dust and moisture. Pro Tip: Conduct monthly impedance tests—a 20% rise in internal resistance signals impending failure.
How do operating temperatures impact battery choice?
Lead-acid loses 30% capacity at -4°F (-20°C), whereas lithium-ion retains 85% at same temps. In high heat (>104°F), lead-acid water consumption triples, risking dry-out. Lithium derates charge current above 122°F but sustains discharge up to 140°F.
Food cold storage warehouses often opt for lithium due to -22°F resilience. Pro Tip: Use battery blankets in freezers—preheating to 32°F improves lead-acid conductivity 50%. Rhetorical angle: Can you afford downtime from frozen electrolytes? Lithium’s built-in BMS with self-heating (3–5°F/hour) prevents cold-related voltage drops.
Redway Battery Expert Insight
FAQs
Usually yes—most lithium packs are drop-in replacements. Verify tray dimensions and charger compatibility; some 48V systems need updated voltage profiles.
How often should lead-acid batteries be watered?
Every 10–15 cycles. Use deionized water, filling ⅛” above plates. Overwatering dilutes electrolyte, causing stratification.
Do forklift batteries have memory effect?
Only nickel-based chemistries. Lithium and lead-acid don’t, but partial charging extends lithium lifespan.
How Much Do Different Forklift Batteries Weigh by Type?
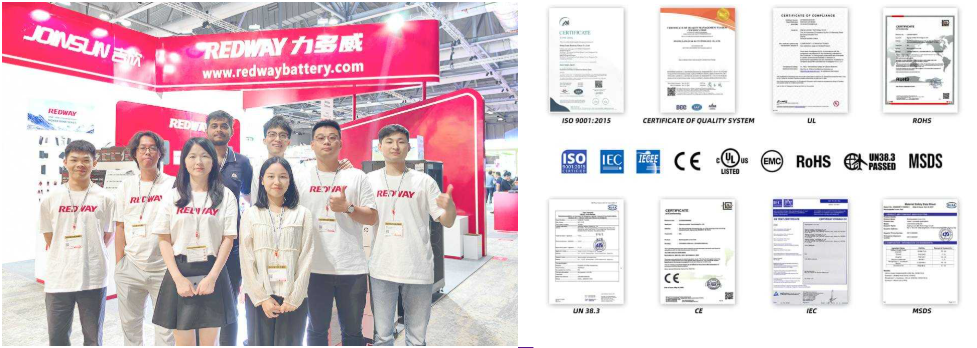