Frequently Asked Questions (FAQs) about forklift batteries focus on lifespan, charging practices, maintenance, safety, and cost comparisons between lithium-ion and lead-acid types. Key concerns include optimal replacement cycles (every 5 years for Li-ion vs. 3–4 for lead-acid), cold storage suitability, and weight management. Regular voltage checks, electrolyte level maintenance, and avoiding deep discharges are critical for longevity. Proper charging protocols and hazard mitigation (e.g., hydrogen venting) ensure operational safety.
How Much Do Different Forklift Batteries Weigh by Type?
How often should forklift batteries be replaced?
Forklift batteries typically last 3–5 years, depending on chemistry and usage. Lithium-ion variants often exceed 5,000 cycles, while lead-acid degrades faster after 1,200 cycles. Pro Tip: Track discharge depth—regular discharges below 20% capacity halve lead-acid lifespan.
Wholesale lithium golf cart batteries with 10-year life? Check here.
Replacement timing hinges on capacity loss. For example, a 48V lead-acid battery dropping below 70% rated capacity (measured via hydrometer) needs replacement. Transitioning to lithium-ion? Expect higher upfront costs but 2–3x lifespan. Beyond cycle limits, swelling, corrosion, or voltage drops below 80% under load signal replacement. Practically speaking, log monthly performance tests to preempt failures.
Can forklift batteries be used in cold storage?
Lead-acid batteries lose 30–40% capacity in sub-0°C environments, while lithium-ion performs better (15% loss at -20°C). Always use battery heaters for lead-acid in cold storage to prevent sulfation.
Want OEM lithium forklift batteries at wholesale prices? Check here.
Cold slows chemical reactions, reducing runtime. For instance, a 600Ah lead-acid battery at -10°C delivers only 360Ah. Lithium-ion’s BMS-regulated thermal management mitigates this. Pro Tip: Preheat batteries to 5°C before charging to avoid damage. But what happens if you skip insulation? Lead-acid plates sulfate irreversibly, while lithium-ion cells risk plating metallic lithium. Transitional solutions like heated storage cabinets maintain efficiency. Redway’s cold-optimized LiFePO4 batteries sustain 95% capacity at -30°C.
What is the cost difference between lead-acid and lithium-ion forklift batteries?
Lithium-ion costs 2–3x more upfront but offers lower lifetime costs. A 48V 600Ah lead-acid pack costs $4,000 vs. $10,000 for lithium, but lithium lasts 10+ years with minimal maintenance.
Factor | Lead-Acid | Lithium-Ion |
---|---|---|
Initial Cost | $4,000 | $10,000 |
Lifespan | 3–4 years | 8–10 years |
Energy Efficiency | 70–80% | 95–98% |
Beyond purchase price, factor in labor: lead-acid requires weekly watering, while lithium is maintenance-free. Real-world example: A warehouse saving $2,000/year on labor with lithium breaks even in 3 years. Pro Tip: Use total cost of ownership (TCO) calculators—lithium often wins long-term.
Can Forklift Batteries Be Used for Home Solar?
What maintenance practices extend forklift battery life?
For lead-acid: weekly watering, terminal cleaning, and equalizing charges. Lithium-ion needs monthly SOC checks and storage at 40–60% charge if idle.
Neglecting electrolyte levels exposes plates, causing sulfation. A 48V battery losing 10% water monthly requires refilling with distilled water. For lithium, avoid 100% SOC storage—store at 30–50% to slow degradation. Transitional practices like using automated watering systems save labor. Example: Toyota’s HydroLink system cuts maintenance time by 90%. Pro Tip: Document voltage trends—sudden drops indicate cell failure.
What safety protocols apply to forklift batteries?
Mandatory protocols include hydrogen venting, PPE (gloves, goggles), and spill containment. Lithium-ion requires BMS-monitored charging to prevent thermal runaway.
Hydrogen gas from lead-acid charging explodes at 4% concentration. Install ventilation moving 1 CFM per square foot. For lithium, thermal runaway triggers above 150°C—use CO2 extinguishers, not water. Real-world example: Amazon warehouses enforce 10-foot clearance around charging stations. Practically speaking, train staff on emergency shutdowns and acid spill kits. Pro Tip: Label batteries with install dates—older units demand stricter inspections.
Risk | Lead-Acid | Lithium-Ion |
---|---|---|
Fire Hazard | Low (unless overcharged) | Moderate (thermal runaway) |
Chemical Exposure | Sulfuric acid leaks | Electrolyte vapor |
Maintenance Risks | Watering hazards | High-voltage dangers |
How does charging frequency affect battery lifespan?
Lead-acid prefers 8-hour full charges; partial charges cause stratification. Lithium-ion thrives on opportunity charging, with no memory effect.
Frequent shallow charges sulfate lead-acid plates, reducing capacity by 20% annually. Lithium’s 80% DoD tolerance allows partial top-ups. For example, a lithium pack charged 3x/day at 30% depletion lasts 6,000 cycles vs. 1,200 for lead-acid. Transitioning to opportunity charging? Ensure lead-acid gets weekly equalization. Pro Tip: Set chargers to 10–15% below max voltage to reduce stress.
Redway Battery Expert Insight
FAQs
Technically yes, but lead-acid’s low depth of discharge (50%) makes them inefficient. Use lithium-ion forklift batteries only if they include compatible BMS for solar charge controllers.
Do all forklift batteries require special chargers?
Absolutely. Lead-acid needs voltage-tapered chargers (2.45V/cell), while lithium-ion requires constant current/constant voltage (CC/CV) profiles. Mismatched chargers cause fires or capacity loss.
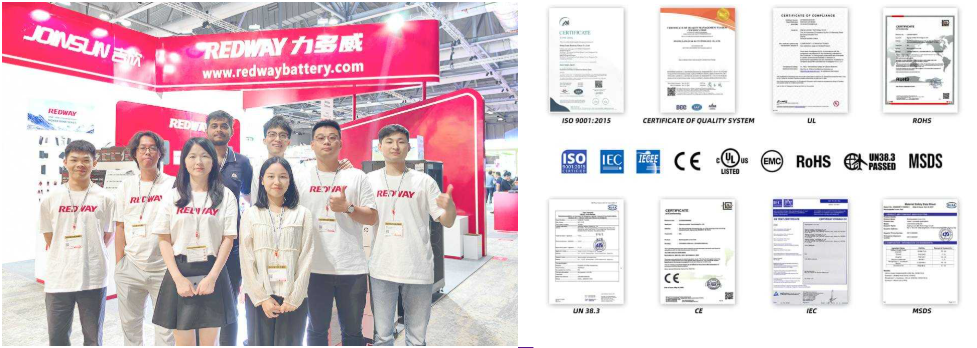