Proper forklift battery care ensures longevity and safety. Key steps include daily voltage checks, maintaining electrolyte levels in lead-acid batteries, and avoiding deep discharges. For lithium-ion models, use temperature-controlled charging (0°C–45°C) and store at 50% charge. Always clean terminals with baking soda solutions to prevent corrosion. Implement scheduled equalization charges every 10 cycles for lead-acid types to balance cells.
How to Access the Battery on a Toyota Forklift
What daily maintenance ensures forklift battery health?
Daily care focuses on voltage monitoring, terminal cleaning, and charge state optimization. Lead-acid batteries need electrolyte topping with deionized water when plates are exposed, while lithium-ion requires avoiding storage at full charge. Pro Tip: Use infrared thermometers to spot overheating cells during charging—a 10°C+温差 between cells indicates imbalance.
Wholesale lithium golf cart batteries with 10-year life? Check here.
Beyond basic checks, voltage should stay above 1.75V/cell for lead-acid during operation. Did you know sulfation starts below 20% charge? For lithium-ion, BMS data logs reveal cycle patterns—sudden capacity drops often signal coolant leaks. Example: A 48V 600Ah lead-acid battery losing 0.5V overnight likely has a faulty cell. Transitional phrase: Considering chemical wear, equalize every 50 cycles by charging at 2.7V/cell for 12 hours.
Want OEM lithium forklift batteries at wholesale prices? Check here.
How should charging practices adapt to battery chemistry?
Tailor charging to lead-acid or lithium-ion requirements. Lead-acid needs slow 8–10-hour charges with rest periods, while lithium-ion handles 2C fast charging if temps stay below 45°C. Pro Tip: For flooded lead-acid, pause charging hourly to check water levels—gassing phase increases evaporation.
Practically speaking, lead-acid chargers should taper current when hitting 2.45V/cell. Why risk thermal runaway? Lithium-ion systems demand precision: Our 72V LiFePO4 packs use CC-CV until 3.65V/cell with ±0.5% voltage tolerance. Example: Charging a 48V lithium battery to 54.6V (3.65V x 15 cells) ensures 95% capacity retention after 2,000 cycles. Transitional phrase: Beyond voltage, temperature sensors are crucial—charging below freezing causes lithium plating.
Parameter | Lead-Acid | Lithium-Ion |
---|---|---|
Charge Rate | 0.1C | 0.5–1C |
End Voltage | 2.45V/cell | 3.65V/cell |
Forklift Battery Charging Station: A Comprehensive Guide
Why is water critical for lead-acid forklift batteries?
Water compensates for electrolyte evaporation during gassing. Use only distilled water to avoid mineral contamination—tap water causes sulfation. Maintain levels ¼” above plates; overfilling dilutes acid concentration.
Technically, hydrogen gas releases during charging reduce electrolyte volume by 5–15% per cycle. Ever seen battery corrosion? It’s often low water exposing lead plates to oxygen. Example: A 36V 800Ah battery needing weekly 2L water refill indicates heavy use. Transitional phrase: To optimize hydration timing, refill post-charge when electrolyte is expanded.
What temperature ranges maximize battery lifespan?
Operate lead-acid between 20°C–30°C; lithium-ion prefers 15°C–25°C. Avoid charging below 0°C or above 45°C—thermal stress degrades all chemistries.
At 35°C, lead-acid loses 50% cycle life; lithium-ion suffers SEI layer growth. Ever wonder why cold storage kills capacity? Lithium ions plate instead of intercalating below freezing. Example: A warehouse heated to 25°C extends battery life by 18 months versus unregulated environments. Transitional phrase: Active liquid cooling adds cost but prevents thermal runaway in 48V+ systems.
Condition | Lead-Acid | Lithium-Ion |
---|---|---|
Ideal Temp | 25°C | 20°C |
Max Discharge | -20°C | -20°C |
Redway Battery Expert Insight
FAQs
Only for lithium-ion with auto-shutdown BMS—lead-acid risks overwatering and grid corrosion. Use timers to limit lead-acid charging to 12 hours max.
How often should battery cables be replaced?
Inspect monthly—replace if insulation cracks or resistance exceeds 0.5 ohms. Poor connections cause 27% efficiency loss in 48V systems.
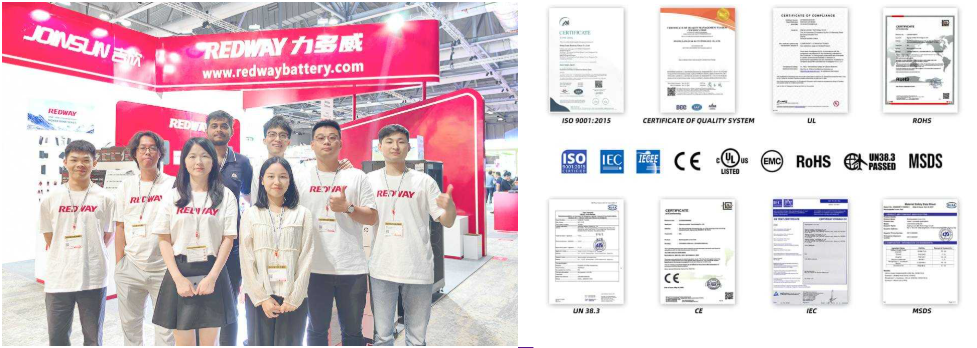