The typical forklift battery lifespan ranges from 1,200–2,500 cycles (5–8 years) depending on chemistry: lead-acid degrades faster due to sulfation, while lithium-ion (LiFePO4) retains 80% capacity beyond 3,000 cycles. Key factors include discharge depth, charging frequency, and ambient temperature. Pro Tip: Avoid discharging below 20% for lead-acid—partial cycles below 50% DoD extend lifespan by 30–50%.
How Much Does a Forklift Battery Weigh?
What factors determine forklift battery lifespan?
Depth of discharge (DoD), charging protocols, and operational environment are primary determinants. Lead-acid batteries lose 10% capacity annually if discharged below 50% regularly, while Li-ion tolerates 80% DoD. Temperature extremes (below 0°C or above 45°C) accelerate degradation by 15–25%.
Wholesale lithium golf cart batteries with 10-year life? Check here.
For lead-acid, cycle life plummets from 1,500 cycles at 50% DoD to 600 cycles at 80% DoD. Lithium-ion, however, maintains 3,000+ cycles even at 80% DoD due to robust cathodes. Charging practices matter too: opportunity charging (multiple partial charges) reduces lead-acid lifespan by inducing stratification. But what about Li-ion? Lithium batteries thrive on partial charges, which actually minimize stress on cells. Pro Tip: Use thermal management systems (cooling plates) in high-temperature warehouses to prevent capacity fade. Imagine a lead-acid battery as a car engine—neglecting oil changes (equalization charges) leads to irreversible wear. For example, a 700Ah lead-acid pack in a 2-shift warehouse may last 3 years, while Li-ion under similar conditions exceeds 6 years.
What’s the average lifespan of Li-ion vs. lead-acid forklift batteries?
Lithium-ion lasts 8–12 years (3,000–5,000 cycles), while lead-acid averages 3–5 years (1,200 cycles). LiFePO4 chemistry’s low internal resistance enables faster charging without heat buildup, a key longevity advantage.
Want OEM lithium forklift batteries at wholesale prices? Check here.
Practically speaking, lithium batteries outlive lead-acid by 2–3x even in intensive 24/5 operations. A Toyota 8HBW23 forklift using lead-acid requires battery swaps every 1.5 years, but Li-ion units from Redway Battery last 4+ years. Beyond cycle counts, calendar aging also matters: Li-ion loses 2-3% capacity annually when idle, versus lead-acid’s 10%+ self-discharge. But how does cost factor in? Though pricier upfront, lithium’s 8-year lifespan delivers 35% lower TCO. Real-world example: A Crown SC 5300 forklift switching to Li-ion reduced energy costs by 40% and eliminated watering labor. Pro Tip: For multi-shift operations, Li-ion’s opportunity charging capability cuts downtime by 30%.
Parameter | Lithium-ion | Lead-acid |
---|---|---|
Cycle Life | 3,000–5,000 | 1,200–1,500 |
DoD Tolerance | 80–90% | 50% |
Maintenance | Zero | Weekly watering |
How do charging practices affect battery longevity?
Partial charging (20–80% SoC) maximizes Li-ion lifespan, while lead-acid requires full 100% charges to prevent sulfation. Fast charging lead-acid beyond 0.2C rate increases plate corrosion by 18%.
Charging frequency is pivotal. Lithium batteries thrive on opportunity charging—topping up during breaks—which keeps cells in the 30–70% “sweet spot.” Lead-acid, conversely, needs full 8-hour charges to mix electrolytes via gassing. Ever seen a stratified lead-acid battery? It’s like unmixed paint: concentrated acid at the bottom corrodes plates. Fast charging lithium at 1C (1-hour charge) is safe with active cooling, but lead-acid risks thermal runaway beyond 0.3C. Pro Tip: Install timed chargers for lead-acid to prevent overcharging—a common cause of grid corrosion. For example, a Hyster H2.5XT forklift using opportunity charging extended Li-ion lifespan by 400 cycles versus single daily charges.
What maintenance extends forklift battery life?
Equalization charges for lead-acid (monthly) and cell balancing for Li-ion (every 6 months) are critical. Cleaning terminals prevents resistance spikes that accelerate aging.
Beyond basic maintenance, monitoring voltage sag identifies aging cells early. Lead-acid requires specific gravity checks (1.265–1.299) to detect stratification, while Li-ion BMS logs track cell variances. Think of it as a blood test for batteries—catching issues before they’re fatal. For lead-acid, post-charge watering prevents plate exposure, but overwatering dilutes electrolyte. Pro Tip: Use automated watering systems to reduce labor and ensure optimal levels. Real-world case: A Raymond 9500 forklift fleet cut battery replacements by 22% after implementing weekly terminal cleaning and monthly equalization.
Maintenance Task | Lead-acid | Lithium-ion |
---|---|---|
Watering | Weekly | None |
Equalization | Monthly | Every 6 months |
Terminal Cleaning | Bi-weekly | Quarterly |
Redway Battery Expert Insight
FAQs
Water every 5–10 charging cycles, post-charge, when electrolyte levels are ¼” above plates. Use deionized water to prevent mineral buildup.
Do lithium forklift batteries need equalization charges?
No—Li-ion cells balance automatically via BMS. Forced equalization risks overvoltage and thermal events.
Can I replace lead-acid with lithium in older forklifts?
Yes, but verify compatibility: Lithium’s 20–50% weight reduction affects forklift stability. Redway’s retrofit kits include adjustable ballast and voltage converters.
Forklift Battery Charging Station: A Comprehensive Guide
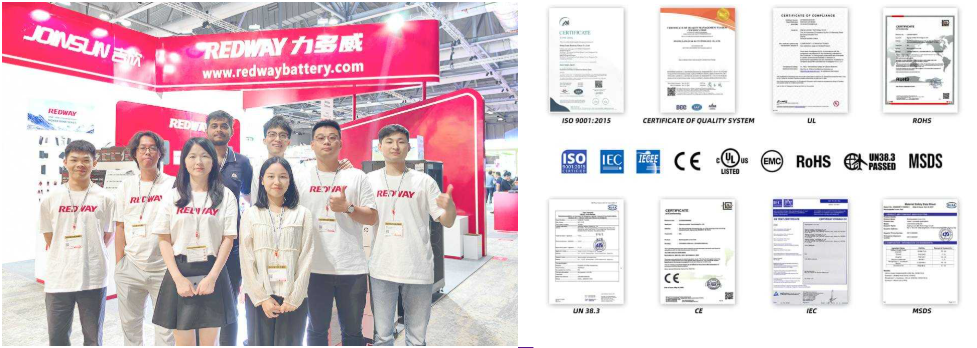