The 8250 Lithium Ion Pallet Jack uses a 48V Li-ion battery to power its electric drive motor and hydraulic pump, enabling efficient lifting (up to 5,500 lbs) and transportation of pallets. Its brushless motor and regenerative braking recover energy during deceleration, extending runtime to 8–10 hours per charge. Integrated load sensors optimize power delivery based on weight, while a modular BMS safeguards against overheating and over-discharge.
How to Access the Battery on a Toyota Forklift: A Complete Guide
What powers the 8250 pallet jack’s operation?
The 8250 relies on a 48V lithium-ion battery pack (typically 100–200Ah) paired with a brushless DC motor. This setup delivers consistent torque for lifting and driving, while regenerative braking converts kinetic energy back into stored power during stops. Pro Tip: Always let the battery cool for 15 minutes after heavy use before recharging to prevent cell stress.
Wholesale lithium golf cart batteries with 10-year life? Check here.
At its core, the 8250’s 48V Li-ion battery provides 15–20% more energy density than lead-acid alternatives, translating to longer shifts without mid-day charging. The brushless motor operates at 85–90% efficiency, minimizing heat buildup even under full 5,500-lb loads. For example, moving 40 pallets/hour drains only ~30% of a 150Ah battery. Beyond raw power, the onboard BMS constantly monitors cell voltages—balancing them during charging to prevent premature aging. A common mistake? Using non-OEM chargers that skip balancing phases, causing uneven wear. Transitionally, while lithium-ion batteries excel in runtime, they demand strict temperature management. Operate in environments below 113°F (45°C) to avoid BMS-induced shutdowns.
Component | 8250 Li-ion | Lead-Acid Equivalent |
---|---|---|
Battery Weight | 150 lbs | 400 lbs |
Charge Time | 2 hrs (80%) | 8–10 hrs |
Cycle Life | 2,000+ | 500–800 |
How does the electric motor enhance performance?
The brushless DC motor eliminates friction-prone commutators, enabling smoother acceleration and 92% energy efficiency. It’s governed by a programmable controller that adjusts torque based on load weight—crucial for preventing wheel slippage with max-capacity pallets.
Want OEM lithium forklift batteries at wholesale prices? Check here.
Unlike traditional AC motors, the 8250’s brushless design uses electronic commutation, reducing maintenance by 70%. The motor delivers up to 4,000W peak power, managed by a PWM controller that modulates current flow. For instance, lifting a 4,000-lb load draws ~120A from the battery, but the controller caps surges at 150A to protect windings. Practically speaking, this means operators can tackle ramps without speed drops. However, brushless motors rely on hall-effect sensors—if these get dirty, erratic movement occurs. A Redway field study found annual sensor cleaning boosts motor lifespan by 3 years. Transitionally, while powerful, the motor’s efficiency depends on battery health. Always check voltage sag under load; if it exceeds 8%, cells may need replacement.
What role do control systems play?
The 8250 uses CAN bus technology to synchronize its motor, hydraulics, and operator inputs. This digital network allows real-time adjustments—like reducing lift speed when batteries dip below 20% charge to conserve energy.
Control systems in the 8250 operate on a 2-tier hierarchy: the main ECU manages drive and lift functions, while subsystems handle braking and battery communication. For example, when an operator lowers the forks, the system engages regenerative braking, feeding ~15% of the potential energy back into the battery. But what happens if the CAN bus fails? A redundant analog circuit maintains basic lift/drive functions at reduced speeds. Pro Tip: Update controller firmware annually—manufacturers often optimize load-response algorithms. Transitionally, while smart controls enhance performance, they require clean power. Voltage spikes from aged batteries can corrupt ECUs; use surge protectors during charging.
Feature | 8250 Li-ion | Legacy Models |
---|---|---|
Control Interface | Touchscreen | Buttons/LEDs |
Error Codes | 50+ diagnosable | 5–10 basic |
Response Time | 50 ms | 200 ms |
How does charging differ from lead-acid models?
Lithium-ion batteries in the 8250 support opportunity charging—partial top-ups during breaks without memory effect. Integrated cell balancing during each charge ensures all 192 cells (in a 48V system) maintain ≤2mV deviation, prolonging pack life.
Charging the 8250’s Li-ion battery involves a 3-stage process: bulk charge (0–80% at 50A), absorption (80–95% at 20A), and balance (95–100% with 5A pulses). This takes 1.5–2 hours versus 8+ hours for lead-acid. For context, a warehouse using opportunity charging can achieve 3 shifts/day instead of 1–2. But beware: using incompatible chargers skips the balance phase, causing capacity loss. Transitionally, while fast charging is convenient, it generates heat. Always charge in well-ventilated areas below 104°F (40°C). A real-world example: A logistics center reduced downtime 60% by installing 4x 48V Li-ion chargers per 10 jacks.
What safety mechanisms are integrated?
The 8250 features multi-layer protection: inertia sensors that cut power during tip-overs, temperature monitors derating power at 131°F (55°C), and hydraulic overload valves preventing lifts beyond 110% capacity. The Li-ion BMS also enforces hard stops at 10% and 95% charge to prevent deep discharge/overcharge.
Safety systems start with mechanical backups—like the manual release valve that lowers forks during power loss. Electronically, the ECU cross-checks load sensor data with motor currents; mismatches trigger instant shutdowns. For example, if a 6,000-lb load is detected (beyond the 5,500-lb limit), the hydraulics lock. Transitionally, while robust, safety systems need validation. Perform monthly overload tests: place 110% weight on forks and confirm shutdown within 2 seconds. Pro Tip: Replace inertia sensors every 5 years—magnet degradation causes false positives.
Redway Battery Expert Insight
FAQs
No—the motor controller’s voltage tolerances (45–52V) mismatch lead-acid’s 46–58V range. Forced retrofits risk overloading the motor.
How often should I calibrate load sensors?
Annually, or after any impact. Use certified 5,500-lb test weights—improper calibration causes hydraulic system strain.
Is the 8250 suitable for freezer warehouses?
Yes, but keep batteries above -4°F (-20°C) during charging. Li-ion cells can’t accept charge below this threshold.
Forklift Battery Charging Station: A Comprehensive Guide
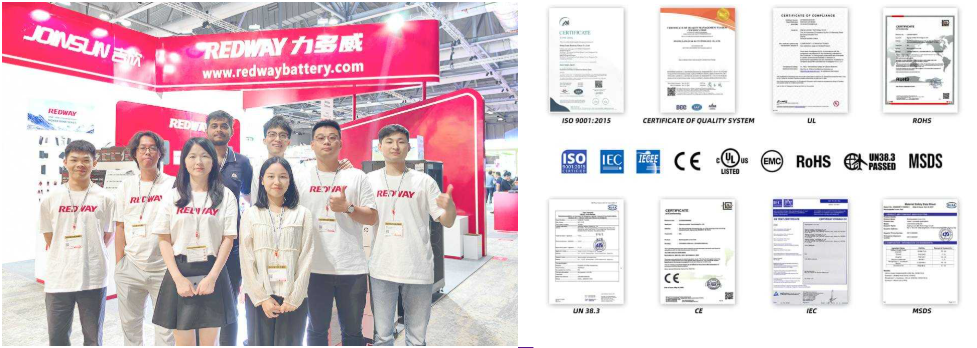