Forklift battery chargers convert AC power to DC to replenish lead-acid or lithium-ion batteries through three stages: bulk (constant current), absorption (constant voltage), and float (maintenance). Designed for 24V–80V systems, they adjust rates based on battery temperature and voltage feedback. Advanced models feature ripple correction (<3%) and microprocessors to prevent sulfation in lead-acid packs. LiFePO4 chargers use voltage ceilings like 29.2V for 24V systems.
How to Access the Battery on a Toyota Forklift: A Complete Guide
What are the three charging stages in forklift batteries?
Forklift chargers use bulk, absorption, and float stages to optimize charge speed and battery health. Bulk delivers 15–25A (lead-acid) until 80% capacity, absorption tops up at reduced current, while float maintains 13.4V (12V systems) to offset self-discharge. Lithium-ion skips float but uses balancing during constant voltage.
Wholesale lithium golf cart batteries with 10-year life? Check here.
During bulk charging, a 48V charger might push 40A until voltage hits 57.6V (lead-acid). Absorption then holds 57.6V while current tapers to 5A. For lithium, bulk stops at 54.6V (3.65V/cell). Pro Tip: Use temperature-compensated charging—batteries at 35°C need 0.03V/cell less to avoid overheating. Think of it like filling a pool: bulk is the hose wide open, absorption is a gentle trickle, and float is just covering evaporation losses.
What components enable AC-to-DC conversion in chargers?
Key components include rectifiers, transformers, and PWM controllers. Transformers step down 230V AC to 72V AC, rectifiers (diodes/SCRs) convert it to DC, while PWM chips regulate current pulses (1–5kHz) for precise voltage control. Cooling fans and thermistors prevent overheating beyond 50°C.
Want OEM lithium forklift batteries at wholesale prices? Check here.
Beyond basic components, high-frequency chargers use IGBT transistors instead of silicon-controlled rectifiers (SCRs) for 92% efficiency vs. SCR’s 78%. For example, a 10kW charger with IGBTs wastes 800W as heat, while SCR models dissipate 2,200W. Pro Tip: Clean fan filters monthly—dust buildup can increase internal temps by 15°C, shortening capacitor lifespan. A failing diode in the rectifier often causes voltage ripple above 5%, detectable via multimeter AC mode on DC outputs.
Component | Role | Failure Symptoms |
---|---|---|
Rectifier | AC to DC conversion | Low output voltage, overheating |
Transformer | Voltage reduction | Humming noise, burnt insulation smell |
PWM Controller | Current regulation | Erratic charging, no absorption stage |
How do chargers detect battery voltage?
Chargers use voltage sensing circuits and Hall effect sensors to identify battery voltage. Upon connection, a 2A trickle current measures open-circuit voltage—24V batteries read 25.3V (lead-acid) or 26.8V (LiFePO4). Mismatches >10% trigger faults to avoid over/undercharging.
Practically speaking, if you connect a 48V charger to a 36V battery, the sensor detects the 22V–25V rest voltage and halts with a “Wrong Voltage” error. Advanced models auto-adjust in 8V increments (24V/36V/48V). Pro Tip: Dirty battery terminals add 0.5–1.2Ω resistance, fooling sensors into reading lower voltages—clean terminals monthly with baking soda solution. It’s like a fuel gauge misreading due to a corroded sensor wire.
What’s the difference between opportunity and conventional charging?
Opportunity chargers deliver partial charges during breaks (15–30 mins) at 0.2C rates, while conventional chargers perform full 8-hour cycles. Opportunity modes extend lead-acid life by minimizing deep discharges but require liquid-cooled cables for 100A+ currents.
Beyond speed considerations, opportunity charging suits multi-shift operations but demands robust battery monitoring. For instance, a 500Ah battery charged opportunely at 100A for 30 minutes regains 50Ah—enough for another 1.5 hours of operation. Pro Tip: Avoid opportunity charging lithium below 10°C—it causes lithium plating, reducing cycle life by half. Traditional charging is like a full meal, while opportunity charging is snacking—useful but not nutritionally complete.
Type | Charge Time | Cycle Life Impact |
---|---|---|
Conventional | 8–10 hours | 1200 cycles (lead-acid) |
Opportunity | 15–30 mins | 900 cycles (with temp control) |
How Much Do Different Forklift Batteries Weigh by Type?
Why is temperature management critical?
High temps (>45°C) degrade lead-acid electrolyte and lithium anode SEI layers. Chargers employ NTC thermistors to reduce voltage by 3mV/°C (lead-acid) or pause charging (lithium) if cells exceed 50°C. Active cooling via fans or liquid systems maintains optimal 20–30°C ranges.
Consider a lithium pack charging at -5°C: ions move sluggishly, causing metallic lithium plating on the anode. This creates internal shorts over time. Pro Tip: Install chargers in well-ventilated areas—ambient temps above 35°C derate output current by 20%. Imagine charging your phone in direct sunlight; it’s slower and risks damage, just like forklift batteries.
Redway Battery Expert Insight
FAQs
Conventional charging takes 8–10 hours for lead-acid (20%–100%), while lithium-ion reaches 95% in 2–3 hours using 0.5C rates. Fast chargers cut this to 1 hour but require liquid cooling.
Can I use a car battery charger for forklifts?
No—car chargers lack voltage/current profiles for deep-cycle forklift batteries. Using them risks undercharging (voltage mismatch) or overheating.
Are forklift chargers safe indoors?
Yes, if ventilation meets OSHA standards (50 CFM/ft²) to disperse hydrogen gas from lead-acid charging. Lithium chargers are safer with zero emissions.
Do chargers work with all battery sizes?
Chargers are rated for voltage (24V/36V/48V/80V) and capacity (100Ah–1500Ah). Mismatched units fail—a 500A charger can’t safely charge a 100Ah battery.
How to extend charger lifespan?
Clean dust quarterly, check fan operation monthly, and recalibrate voltage sensors annually—drifting by >2% strains components.
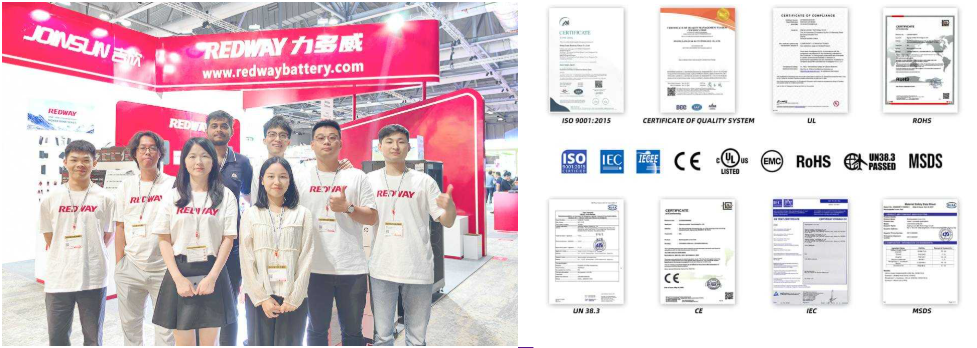