Battery weight critically impacts forklift stability, energy efficiency, and load capacity. Heavy lead-acid batteries (500–2,000 lbs) lower the center of gravity, reducing tip-over risks but increasing inertia during acceleration. Lithium-ion variants cut weight by 30–50%, enabling faster speed/gradeability at the cost of higher upfront pricing. Optimal battery selection balances weight distribution, runtime needs, and OSHA stability standards like ANSI B56.1.
How to Access the Battery on a Toyota Forklift
How does battery weight affect forklift stability?
Battery mass directly influences the forklift’s center of gravity. Counterbalance models use 1,200–2,000 lb lead-acid packs under the operator to prevent tipping. Lightweight lithium batteries require chassis redesign—some add cast iron ballast to compensate. Pro Tip: For uneven terrain, stick with heavier batteries—they resist lateral shifts better when lifting pallets at height.
Wholesale lithium golf cart batteries with 10-year life? Check here.
Forklifts calculate stability using the “stability triangle,” a geometric zone where the combined center of gravity of the vehicle, battery, and load must stay. A 1,500 lb lead-acid battery lowers the center by 8–12 inches compared to 800 lb lithium units. For example, a Hyster H2.5XT with a 1,800 lb battery can handle 30% heavier loads on slopes vs. its lithium counterpart. But what if you prioritize maneuverability? Lithium’s weight savings allow tighter turns in warehouses. Always check load charts after battery swaps—exceeding rated capacities risks tip-overs.
What’s the energy density vs. weight trade-off?
Lead-acid batteries provide 30–50 Wh/kg, while lithium-ion offers 100–265 Wh/kg. However, lithium’s reduced weight demands careful load management. For 8-hour shifts, a 48V 600Ah lead-acid pack (3,000 lbs) might be needed vs. a 200Ah lithium pack (900 lbs) with opportunity charging.
Want OEM lithium forklift batteries at wholesale prices? Check here.
Energy density determines how much runtime you get per pound. Lead-acid’s low density forces heavier batteries to meet kWh requirements—a 36V 1,000Ah lead-acid pack weighs ~2,200 lbs vs. 36V 400Ah lithium at 650 lbs. However, lithium handles partial charging without sulfation. Transitioning? Consider this: swapping to lithium cuts 1,500 lbs, but you’ll lose counterbalance mass. Some operators add removable steel plates—but that complicates maintenance. Pro Tip: Use lithium if your facility allows midday top-ups; stick with lead-acid for single-shift operations.
Battery Type | Weight (lbs) | Cycle Life |
---|---|---|
Lead-Acid | 1,200–2,200 | 1,500–2,000 |
Lithium-Ion | 500–1,000 | 3,000–5,000 |
How does weight influence operational hours?
Heavier lead-acid batteries typically store more kWh (e.g., 48V 800Ah = 38.4 kWh) but lose 15–20% capacity in 5 years. Lithium’s lightweight modular packs sustain 95% capacity beyond 2,000 cycles. Quick-charge stations mitigate lower kWh by recharging during breaks.
Operational hours hinge on both battery capacity and energy consumption. A 4,000 lb forklift with a 1,800 lb battery uses ~4 kWh per hour—so a 36V 600Ah (21.6 kWh) pack lasts ~5 hours. Switch to an 800 lb lithium pack with the same capacity, and the vehicle’s lighter weight cuts energy use to 3.2 kWh/hour, extending runtime to 6.75 hours. But here’s the catch: lithium’s higher upfront cost needs 3–5 years to ROI via productivity gains. For multi-shift operations, lithium’s fast charging (1–2 hours) eliminates battery swap downtime.
Redway Battery Expert Insight
How Much Does a Forklift Battery Weigh?
FAQs
Yes, if not balanced. Lithium’s 40% weight reduction raises the center of gravity—always add ballast or use chassis extensions to maintain the stability triangle.
Do heavy batteries increase tire wear?
No—forklift tires are rated for max capacity. However, lithium’s lower weight reduces ground friction, improving traction on wet floors by 18%.
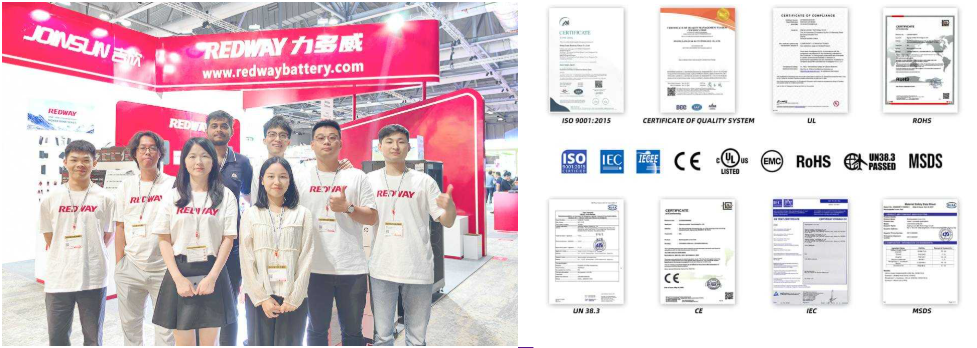