Industrial container handlers are heavy-duty machines designed to lift, stack, and transport shipping containers in ports, warehouses, and logistics hubs. They feature robust hydraulic systems, specialized spreaders, and load capacities ranging from 20 to 45 tons. Electric models use 96V–144V lithium-ion batteries for zero-emission operation, while diesel variants offer higher torque for rough terrains. Safety systems include anti-tip stabilizers and load moment indicators.
How Much Do Different Forklift Batteries Weigh by Type?
What types of industrial container handlers exist?
Common types include reach stackers, straddle carriers, and empty container handlers. Reach stackers handle 30–45 tons with telescopic booms, while straddle carriers lift containers via hydraulic legs. Electric models dominate indoor use, whereas diesel-powered units excel outdoors. Pro Tip: Opt for hybrid systems in mixed environments to balance fuel efficiency and power.
Wholesale lithium golf cart batteries with 10-year life? Check here.
Reach stackers excel in tight spaces due to their 360-degree steering and compact design, moving containers up to 45 tons. Straddle carriers, with their towering legs, lift containers overhead for high-density storage but require wide operational lanes. Why choose electric? For indoor facilities, electric handlers reduce noise and emissions—critical for urban ports. For example, a hybrid reach stacker might use a 144V lithium battery paired with a diesel generator for peak loads. Always verify the handler’s spreader compatibility—ISO container locks vary between 20ft and 40ft units.
What are the key components of a container handler?
Core components include the spreader assembly, hydraulic lift cylinders, and tiered mast systems. Advanced models integrate GPS tracking and automated stacking software. Steel-reinforced frames withstand torsional stress, while regenerative braking in electric models conserves energy during descents.
Want OEM lithium forklift batteries at wholesale prices? Check here.
A container handler’s spreader uses twist locks to grip containers securely, with hydraulic adjustments for different sizes (20ft/40ft/High Cube). The mast, built from high-tensile steel, supports vertical lifting via twin hydraulic cylinders generating up to 350 bar pressure. But how does stability work? Outriggers and load sensors calculate the center of gravity in real time, adjusting hydraulics to prevent tipping. For instance, Konecranes’ reach stackers employ LiDAR to map container positions within 5cm accuracy. Pro Tip: Regularly inspect hydraulic hoses—micro-cracks can lead to catastrophic failures under 300+ bar pressure.
Component | Function | Failure Risk |
---|---|---|
Hydraulic Pump | Power lift/tilt | Seal leaks (>2k hours) |
Spreader Lock | Secure container | Misalignment (5–8%) |
How do load capacities affect handler selection?
Load capacity dictates machine size, power source, and operational clearance. Handlers for 30–45 tons require reinforced booms and dual-axle drivetrains, while sub-20-ton units prioritize maneuverability. Electric models lose 10–15% capacity in cold climates due to battery inefficiency.
Selecting a 40-ton handler over a 30-ton model isn’t just about raw power—it impacts infrastructure costs. Heavier units need reinforced concrete pads and 6m-wide aisles, whereas compact handlers operate in 4m lanes. Imagine trying to stack 40ft containers in a cramped depot—undersized handlers cause 20% slower cycle times. Pro Tip: Add 20% to stated load capacities for real-world buffer—containers often exceed listed weights. For example, Kalmar’s DRF450-60S5X handles 45 tons but maintains a 10km/h speed even at max load.
Capacity | Typical Use | Battery Size |
---|---|---|
20–25 tons | Warehouses | 96V/600Ah |
30–45 tons | Ports | 144V/1200Ah |
What Is Standard Forklift Fork Spacing?
Redway Battery Expert Insight
FAQs
Diesel-powered handlers with all-wheel drive can manage slopes up to 15%, but electric units require paved surfaces—uneven terrain risks battery dislodgement and hydraulic leaks.
How often should container handlers be serviced?
Perform hydraulic checks every 500 hours and battery inspections every 100 cycles. Neglecting fluid changes causes 40% of pump failures.
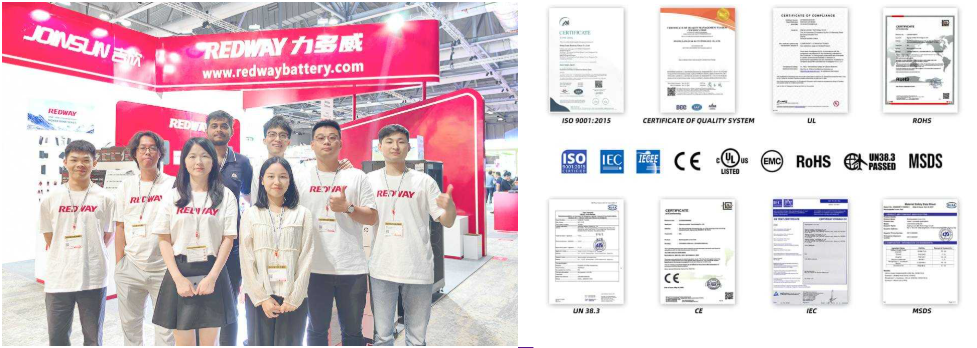