Lithium-ion (Li-ion) batteries outperform lead-acid in energy efficiency, lifespan, and fast charging, making them ideal for high-throughput warehouses. Lead-acid remains cost-effective for light-use applications but requires frequent maintenance and longer charging times. Li-ion’s higher upfront cost offsets with 2–3x longer cycle life (3,000–5,000 cycles vs. 1,500) and 30% energy savings. How Much Does a Forklift Battery Weigh?
What factors determine forklift battery choice?
Selecting between Li-ion and lead-acid hinges on operational intensity, total cost of ownership (TCO), and charging infrastructure. High-shift operations benefit from Li-ion’s rapid charging, while intermittent use may favor lead-acid’s lower initial cost.
Operational demands dictate the optimal choice. For example, a three-shift warehouse using Li-ion can opportunity-charge during breaks, achieving 24/7 uptime. Lead-acid requires 8–10-hour full charges and equal cooling periods, reducing availability. Pro Tip: Calculate TCO over 5 years—Li-ion often saves 20–40% despite higher upfront costs. Technically, Li-ion maintains 80% capacity after 3,000 cycles vs. lead-acid’s 30% degradation at 1,200 cycles. A Toyota 8HBW23 forklift using Li-ion reduces energy costs by $4,000 annually compared to lead-acid.
Wholesale lithium golf cart batteries with 10-year life? Check here.
Factor | Lithium-ion | Lead-Acid |
---|---|---|
Energy Density (Wh/kg) | 150–200 | 30–50 |
Charge Efficiency | 95–99% | 70–85% |
Partial Charge Tolerance | Yes | No |
How do energy densities compare?
Li-ion offers 3–4x higher energy density than lead-acid, enabling lighter batteries with equivalent runtime. A 600Ah Li-ion pack weighs 50% less than lead-acid, reducing forklift wear.
Higher energy density directly impacts performance. A 48V 600Ah Li-ion battery (28.8kWh) weighs ~350 kg versus 1,000 kg for lead-acid. This weight reduction lowers tire and drivetrain wear by 18–22%, per Hyster Europe data. However, lead-acid’s weight provides counterbalance advantages in some configurations. Pro Tip: Use Li-ion in electric reach trucks where weight savings improve maneuverability. But what happens if you need abrupt stops? Lead-acid’s mass enhances stability, while Li-ion requires advanced brake systems. For example, Crown’s SP 2300 reach truck with Li-ion achieves 12-hour runtime with 30-minute midday charges.
Want OEM lithium forklift batteries at wholesale prices? Check here.
What’s the cost difference over 5 years?
Li-ion’s TCO is 20–40% lower long-term despite 2–3x higher upfront costs. Lead-acid incurs hidden expenses like watering, equalization, and shorter lifespan.
Over five years, a 600Ah Li-ion battery costs ~$18,000 (including $12,000 upfront + $6,000 energy/maintenance) versus $24,000 for lead-acid ($6,000 upfront + $18,000 replacements/energy). Why? Li-ion eliminates watering labor ($1,200/year), reduces energy use by 30%, and avoids replacement cycles. A Yale forklift study showed Li-ion reduced downtime costs by 45% in cold storage facilities. However, lead-acid remains viable for single-shift operations with infrequent use. Transitional phrase: Beyond dollar figures, consider productivity gains—Li-ion’s opportunity charging adds 30+ minutes daily operation.
Cost Factor | Li-ion | Lead-Acid |
---|---|---|
Cycle Life | 3,000–5,000 | 1,200–1,500 |
Maintenance | $0.02/Ah/cycle | $0.08/Ah/cycle |
5-Year TCO | $0.15/kWh | $0.27/kWh |
How does lifespan differ between technologies?
Li-ion lasts 2–3x longer, with 3,000–5,000 cycles at 80% capacity versus lead-acid’s 1,200–1,500. Depth of discharge (DoD) impacts both—Li-ion handles 80% DoD daily without degradation.
Cycle life directly affects replacement costs. Li-ion’s nickel-manganese-cobalt (NMC) cells lose 0.03% capacity per cycle vs. lead-acid’s 0.1% loss. Practically speaking, a Li-ion forklift battery used 5x weekly hits 3,000 cycles in 11.5 years—lead-acid needs replacing every 4–5 years. Pro Tip: Avoid deep cycling lead-acid below 50% DoD—it halves lifespan. For example, a Raymond 8250 reach truck with Li-ion logged 14,000 hours without capacity loss in a Kroger distribution center study. Transitional phrase: Considering labor and downtime, lifespan becomes a strategic advantage.
Redway Battery Expert Insight
Lithium-ion dominates modern forklift fleets through superior energy efficiency and lifetime value. Our custom NMC packs enable 2-hour fast charging and 8,000-cycle lifespans with integrated Battery Management Systems (BMS) for thermal safety. For mixed-voltage fleets, we offer drop-in lead-acid replacements with 20% lighter modules, slashing operational costs while extending equipment longevity.
FAQs
Yes for multi-shift operations—Li-ion’s 5-year TCO averages 40% lower than lead-acid. Low-use scenarios (<4 hrs/day) may still benefit from lead-acid’s lower capital cost.
Can I retrofit lead-acid forklifts with lithium batteries?
Only with voltage-compatible BMS and charger upgrades. Li-ion’s flat discharge curve requires adjusting voltage cutoffs to prevent premature shutdowns.
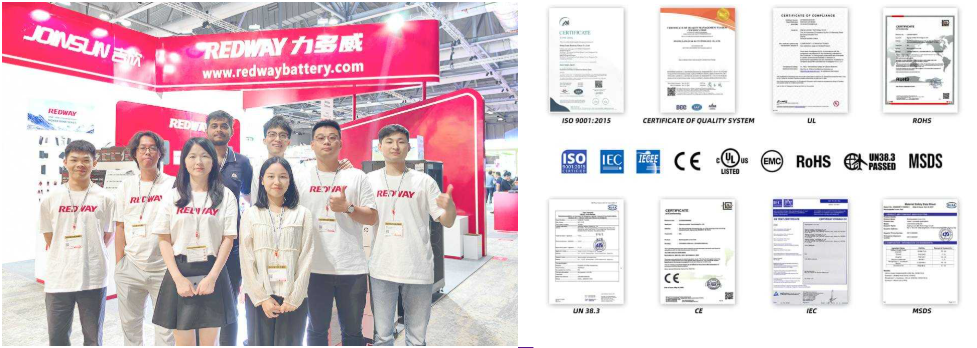