Electric tow tractors and tuggers are electric-powered material handling vehicles designed to pull or push heavy loads (1–50 tons) in industrial settings. Using AC motors and lithium-ion batteries, they replace manual carts and diesel alternatives in airports, warehouses, and manufacturing plants. Modern models feature regenerative braking, obstacle detection, and modular payload attachments. How Much Do Different Forklift Batteries Weigh by Type?
What distinguishes electric tuggers from traditional diesel models?
Electric tuggers use zero-emission powertrains with quieter operation (≤65 dB) vs. diesel’s 85–100 dB. Lithium-ion batteries enable faster charging (1–2 hours) and eliminate fuel handling. Key metrics: continuous towing force (500–5,000 lbf), gradient handling (≤15%), and IP54-rated water resistance for outdoor use.
Unlike diesel models requiring exhaust systems and fuel pumps, electric tuggers rely on motor controllers (like Curtis 1238E) and battery management systems (BMS) for thermal safety. For example, a 72V 200Ah LiFePO4 system can tow 8,000 lbs for 6–8 hours per charge. Pro Tip: Always match the tugger’s rated drawbar pull to your trailer weight—overloading accelerates motor brush wear. Transitioning from diesel? Expect 30–50% lower operating costs but higher upfront investment ($18K–$45K).
Wholesale lithium golf cart batteries with 10-year life? Check here.
How do payload capacities vary between tugger types?
Capacity depends on frame design (rigid vs. articulated) and motor torque (30–150 Nm). Warehouse tuggers handle 1–10 tons, while heavy-duty airport tractors manage 20–50 tons. Lithium batteries sustain peak loads better than lead-acid, with 95% discharge depth vs. 50%.
Industrial electric tuggers use reinforced chassis and planetary gear drives to distribute weight. Take the Redway RTT-45: its dual 15 kW motors deliver 45,000 lbs towing force using a 144V 400Ah battery. But what happens if you exceed payload limits? Premature bearing failure and reduced brake lifespan. Comparatively, pedestrian-operated models max out at 4,400 lbs, while rider-seated units handle 22,000+ lbs. Pro Tip: Add 20% to your calculated payload for acceleration/deceleration forces. Here’s a quick comparison:
Want OEM lithium forklift batteries at wholesale prices? Check here.
Type | Payload | Use Case |
---|---|---|
Pedestrian | 1–5 tons | Warehouse carts |
Rider | 5–25 tons | Airport baggage |
Heavy-Duty | 25–50 tons | Shipyard trailers |
What battery technologies power modern electric tuggers?
Three dominate: LiFePO4 (safety), NMC (energy density), and LTO (fast-charging). LiFePO4 dominates industrial use (3,000–5,000 cycles) due to thermal stability, while NMC suits space-constrained operations.
A 96V 300Ah LiFePO4 pack provides 28.8 kWh—enough for 12 hours of mixed towing. LTO batteries, though pricier, charge in 15 minutes but occupy 30% more space. Why does chemistry matter? Warehouse tuggers needing 200+ daily cycles benefit from LTO’s 20,000-cycle lifespan, despite higher costs. Pro Tip: Monitor battery SOC (State of Charge) religiously—consistent deep discharges below 20% permanently degrade capacity. Transitional note: Beyond chemistry, charging infrastructure matters. Industrial 72V systems often use 10–30 kW onboard chargers compatible with CCS or CHAdeMO connectors.
What safety features are mandatory for electric tow tractors?
OSHA/ANSI require emergency stop buttons, load-sensitive brakes, and blue safety lights. Advanced models add ultrasonic obstacle detection (3–5m range) and rollover protection structures (ROPS).
Mechanical brakes must engage automatically if the electrical system fails. For example, the Ring Motor RG-2000 uses dual redundant hydraulic disc brakes with 0.3g deceleration. Did you know? Tuggers operating near pedestrian zones need strobe lights and 360° cameras. Pro Tip: Conduct weekly brake pad thickness checks—replace at ≤3mm to prevent failure during emergency stops.
Feature | Regulation | Penalty for Non-Compliance |
---|---|---|
E-Stop | ANSI B56.9 | $13K+ fines |
ROPS | OSHA 1926.602 | Work stoppage |
Lights | ISO 3691 | Liability lawsuits |
How does gradient affect electric tugger performance?
Steeper slopes increase motor current draw exponentially. A 10% grade reduces runtime by 40% vs. flat terrain. Motors must have 150% overload capacity for sustained hill climbing.
Tuggers rated for 15% gradients use helical gear reducers (85% efficiency) and 24” pneumatic tires. Compare that to a 5% max gradient model using smaller motors and solid tires. Practically speaking, always derate advertised gradients by 25% when towing near capacity. Pro Tip: Use incline sensors to trigger low-gear modes automatically—prevents controller overheating on long slopes. Forklift Battery Charging Station: A Comprehensive Guide
Redway Battery Expert Insight
FAQs
LiFePO4 lasts 5–7 years (3,000 cycles) with proper maintenance. Avoid temperatures above 45°C and full discharges below 10%.
Can electric tuggers handle outdoor terrain?
Only IP54-rated models with all-terrain tires. Avoid mud deeper than 4” and grades exceeding OEM specs.
Are electric tuggers cheaper than diesel long-term?
Yes—average 5-year savings hit $28K from lower energy ($0.15/kWh vs. $3.50/gallon diesel) and maintenance costs.
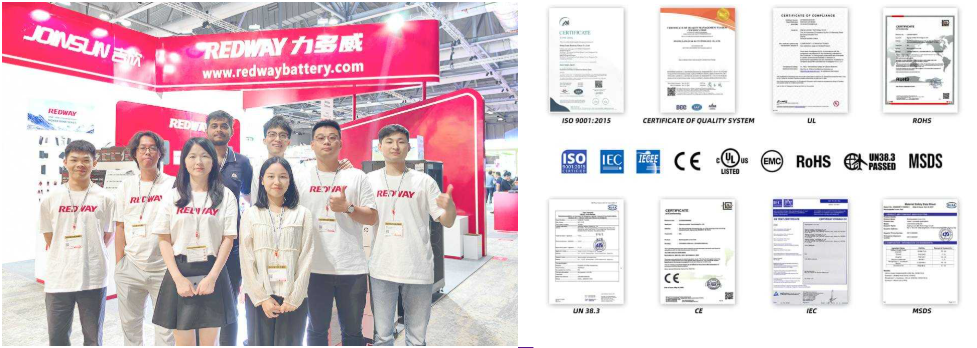