The 36V 18-85-23 battery is a lead-acid or lithium-ion power pack designed for Hyster E50XL forklifts, measuring 38.29 inches in length. With 600–800 Ah capacity, it supports 5–8 hour shifts, depending on load cycles. Lithium variants offer 2,000+ cycles vs. 1,200 for lead-acid. Charging typically requires 36V chargers with temperature compensation. Pro Tip: Use adaptive chargers for lithium to prevent cell imbalance.
How to Access the Battery on a Toyota Forklift: A Complete Guide
What makes the 18-85-23 battery model unique for Hyster E50XL?
The 18-85-23 designation specifies length (38.29″), width, and terminal orientation for seamless E50XL integration. Its 36V configuration balances power density and heat dissipation critical for Class II forklift operations.
Wholesale lithium golf cart batteries with 10-year life? Check here.
This battery’s 18-inch width and rear-terminal placement prevent clearance issues in the E50XL’s compartment. With a 600–800 Ah range, it sustains 3,000–4,500 lbs lifts for 6–8 hours. Lead-acid versions weigh ~2,200 lbs versus 700 lbs for lithium, impacting forklift counterbalance. Pro Tip: Check compartment dimensions before retrofitting lithium—some models need spacer kits. For instance, a lithium 18-85-23 battery reduces recharge downtime by 60% compared to lead-acid, boosting warehouse productivity. Watch out: Mixing old and new lead-acid cells accelerates sulfation—replace entire banks at once.
Parameter | Lead-Acid | Lithium |
---|---|---|
Weight | 2,200 lbs | 700 lbs |
Cycle Life | 1,200 | 2,500+ |
Charge Time | 8–10h | 2–3h |
How does voltage affect Hyster E50XL performance?
36V systems optimize torque for 3,000–4,500 lb lifts without overheating motors. Lower voltages (24V) strain components under heavy loads, while 48V may require motor rewinding.
Want OEM lithium forklift batteries at wholesale prices? Check here.
Hyster’s E50XL motors are wound for 36V nominal operation—deviating from this risks field weakening or commutator arcing. At 36V, the battery delivers 120–150A continuous current, enabling 8–10 mph travel with loads. But what happens if you use a mismatched voltage? A 48V pack could over-rev the motor by 33%, wearing brushes prematurely. Pro Tip: Stick to OEM voltage specs unless upgrading the entire drivetrain. For example, a lithium 36V pack maintains voltage stability during peak draws, unlike lead-acid, which sags below 30V under heavy loads. Moreover, proper voltage alignment ensures the forklift’s controller interprets SOC accurately.
Lead-acid vs. lithium: Which is better for the E50XL?
Lithium batteries offer 70% weight reduction and 3x faster charging but cost 2–3x more upfront. Lead-acid remains cheaper for low-duty cycles but requires watering and equalization.
For multi-shift operations, lithium’s 2,500+ cycles and opportunity charging (topping up during breaks) reduce downtime. Conversely, lead-acid needs full 8-hour charges to avoid sulfation. Imagine this: A warehouse using lithium saves 400 hours/year in charging time—equivalent to 50 workdays. However, lithium’s BMS adds complexity; cell failures may require module replacements instead of single-cell swaps. Pro Tip: For cold storage below 32°F, stick to lead-acid—lithium charge rates plummet under 50°F. Here’s a cost breakdown over 5 years:
Cost Factor | Lead-Acid | Lithium |
---|---|---|
Initial | $4,000 | $11,000 |
Maintenance | $1,200/yr | $200/yr |
Replacement | Every 2 yrs | Every 5+ yrs |
How to maintain a 36V Hyster forklift battery?
Equalize monthly for lead-acid and update BMS firmware for lithium. Keep terminals corrosion-free and avoid deep discharges below 20% SOC.
Lead-acid demands specific gravity checks (1.265–1.299 per cell) and distilled water refills. In contrast, lithium batteries self-balance but need storage at 50% SOC if idle for weeks. Did you know? Overwatering lead-acid cells dilutes electrolyte, reducing capacity by 15%. A real-world example: A warehouse extending lead-acid lifespan to 1,500 cycles by implementing bi-weekly equalization. Pro Tip: Use infrared cameras during charging to detect hot cells—a sign of impending failure. Transitioning between charge cycles? Always let lead-acid cool for 2 hours post-charging before use.
Forklift Battery Charging Station: A Comprehensive Guide
Can third-party batteries harm Hyster E50XL systems?
Non-OEM batteries risk connector mismatch and BMS incompatibility. Poorly regulated units may overheat motor controllers or provide inaccurate SOC readings.
Hyster’s CANbus system expects specific voltage curves and fault codes—third-party BMS might not communicate throttle or regen braking data correctly. For example, a generic lithium pack caused E50XL error codes 21-09 (communication timeout) in a logistics center, halting operations. But does OEM always mean better? Sometimes OEM batteries are rebranded third-party cells with 30% markup. Pro Tip: Choose UL2580-certified replacements with compatible data ports. Moreover, verify that the battery’s discharge curve aligns with the forklift’s Curtis controller expectations—sharp drops trigger low-voltage faults.
Redway Battery Expert Insight
FAQs
Only if dimensions, terminal polarity, and communication protocols match. Mismatched BMS can deactivate Hyster’s dash display.
How long does a 36V 18-85-23 battery last per charge?
Lead-acid: 6–8 hours. Lithium: 8–10 hours with opportunity charging. Actual runtime depends on lift frequency and load weight.
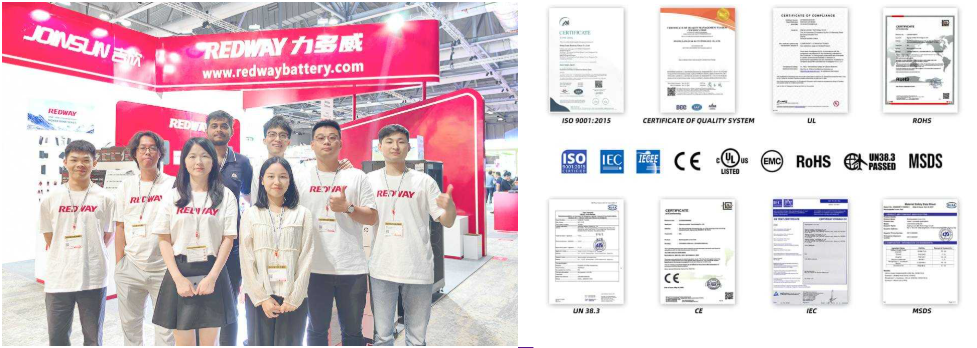