The Hyster E25 XL2 36V 18-85-17 industrial forklift requires a 36V deep-cycle lead-acid battery with exact physical dimensions (typically L850mm × W175mm × H310mm) and terminal configuration matching OEM specifications. The “18-85-17” code denotes a 685Ah capacity in a 36V configuration. Replacement options must meet IEC 60254-1 standards for industrial applications and integrate seamlessly with the truck’s charging system. Third-party lithium conversions require BMS compatibility with Hyster’s voltage thresholds and thermal management protocols.
What Are Forklift Battery Cell Sizes?
What physical dimensions are critical for E25 XL2 batteries?
The battery compartment requires 850mm length × 175mm width (±2mm tolerance), with height not exceeding 310mm including terminals. Weight distribution must align with the truck’s center of gravity specs—lead-acid units typically weigh 540-580kg. Pro Tip: Always verify terminal orientation (left/right positive) using factory schematics before installation to prevent reverse polarity damage.
Wholesale lithium golf cart batteries with 10-year life? Check here.
Industrial battery replacements demand millimeter precision—the E25 XL2’s compartment has only 3-5mm clearance laterally. For example, a 852mm-long battery would require forklift modification costs exceeding $1,200. Transitioning to lithium? Remember, aluminum enclosures save 40% weight but need additional ballast to maintain operational stability. Always cross-reference the 18-85-17 footprint against DIN 43571 standards for industrial battery trays.
How does battery capacity affect Hyster E25 performance?
The original 685Ah (C5 rating) provides 6-8 hours runtime under 80% DoD. Upgrading to 725Ah lithium extends operation by 1.5 hours but requires 30A continuous charging compatibility. Warning: Exceeding 750Ah risks overloading the truck’s battery restraint system rated for 600kg max.
Want OEM lithium forklift batteries at wholesale prices? Check here.
Chemistry | Cycle Life | Charge Time |
---|---|---|
Lead-Acid | 1,500 cycles | 8-10h |
LiFePO4 | 3,500 cycles | 2-3h |
Are lithium batteries viable replacements?
Yes, but LiFePO4 conversions require BMS synchronization with Hyster’s CANbus system (post-2018 models). Key challenges include reprogramming voltage cutoffs from 1.75V/cell (lead-acid) to 2.5V/cell thresholds. Successful retrofits show 23% efficiency gains but need UL 2580-certified packs with IP67 protection for industrial environments.
What charger compatibility is required?
Original 36V chargers deliver 80A bulk charge with temperature-compensated absorption at 43.2V. Third-party chargers must replicate the OEM’s 5-stage profile including equalization cycles. Lithium systems need adjustable CV phases below 43.2V to prevent BMS disconnects.
How to maintain 18-85-17 battery health?
Weekly specific gravity checks (lead-acid) should show 1.265-1.285 SG. Monthly equalization charges at 46.8V prevent stratification. For lithium, maintain 20-80% SoC during storage and implement monthly full cycles to recalibrate capacity readings.
Parameter | Lead-Acid | LiFePO4 |
---|---|---|
Optimal Temp | 20-30°C | 0-45°C |
Water Topping | Bi-weekly | Not Required |
Redway Battery Expert Insight
FAQs
Not recommended—golf cart batteries lack the CCA ratings for lift motor surges and typically fail within 6 months under industrial loads.
What’s the cost difference between lead-acid and lithium?
Lithium solutions cost 2.8× upfront but achieve ROI in 18-24 months through reduced maintenance and energy savings.
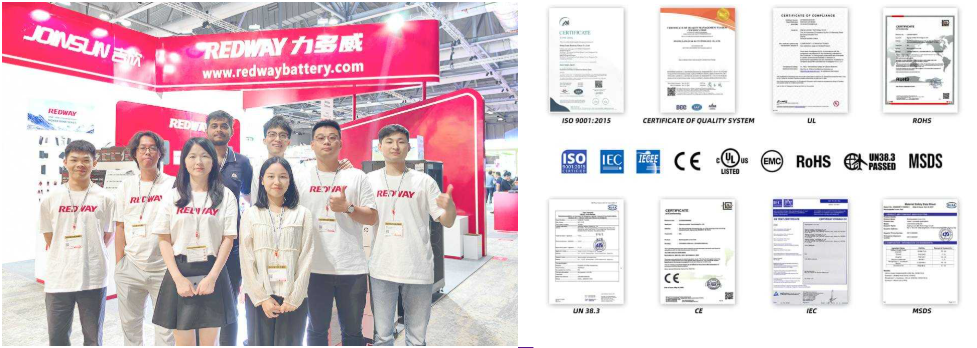