The Nissan WSN-30 24V 12-85-13 battery is a specialized industrial power unit designed for electric forklifts or material handling equipment. It requires a 24V lead-acid battery system with specific terminal configuration and dimensions matching OEM specifications. For optimal compatibility, prioritize batteries with group size G-24 (L13″ x W6.8″ x H10.5″) and recessed terminal posts. Pro Tip: Always verify the battery compartment dimensions and charging system compatibility before replacement. Forklift battery weight typically ranges 150–200 kg for 24V systems, necessitating proper lifting equipment during installation.
How Much Do Different Forklift Batteries Weigh by Type?
What are the key specifications for WSN-30 replacement batteries?
Nissan WSN-30 batteries require precise 24V nominal voltage and capacities typically spanning 500–850Ah. Terminal alignment (usually SAE posts) and tray dimensions (approx. 31×19×29cm) are critical for secure fitment. Deep-cycle models with 1,200+ cycle life at 80% DOD ensure operational reliability.
Wholesale lithium golf cart batteries with 10-year life? Check here.
Industrial batteries for WSN-30 forklifts demand stringent compatibility with onboard chargers and vehicle electronics. Lead-acid variants remain standard, though lithium-ion upgrades require modified charging protocols. For example, a lithium replacement would need BMS integration to prevent voltage spikes in the 24V system. Transitional phrase: While voltage matching seems straightforward, real-world implementation requires deeper analysis. Pro Tip: Always check battery polarity configuration – reversed terminals can fry controller circuits instantly.
How does 12-85-13 coding affect battery selection?
The 12-85-13 designation indicates specific capacity and construction parameters – likely 12 cells @ 85Ah with 13-plate design. This coding system ensures correct intercell connector spacing and electrolyte volume for OEM charging profiles.
Want OEM lithium forklift batteries at wholesale prices? Check here.
Battery plates per cell directly impact discharge rates and cycle longevity. Thirteen 2V cells (totaling 26V fully charged) require precise equalization during maintenance. Transitional phrase: Beyond code deciphering, practical installation factors dominate. Real-world example: Using a generic 24V battery without matching plate count risks reduced runtime and premature sulfation. Pro Tip: Cross-reference manufacturer datasheets for amp-hour ratings at 6-hour discharge rates to ensure true capacity equivalence.
Parameter | OEM Spec | Replacement Minimum |
---|---|---|
Voltage | 24V | 24V ±0.5V |
Capacity | 850Ah | 800Ah |
Can lithium batteries replace lead-acid in WSN-30 systems?
Lithium-ion conversions are possible but require charger modifications and BMS integration. LiFePO4 batteries offer 50% weight reduction and 3× faster charging, but initial costs are 2–3× higher than lead-acid equivalents.
Critical considerations include CAN bus compatibility and temperature monitoring. Transitional phrase: Despite apparent advantages, operational realities dictate careful planning. Pro Tip: Install voltage step-down modules if converting to lithium to prevent ECU overvoltage errors in legacy systems.
Feature | Lead-Acid | Lithium |
---|---|---|
Cycle Life | 1,200 | 3,000+ |
Charge Time | 8–10h | 2–3h |
What safety protocols govern battery replacement?
ASME B56.1 standards mandate insulated tools, acid containment kits, and load-bearing verification for battery compartments. Proper PPE (face shields, acid aprons) is mandatory during handling due to explosion risks from hydrogen off-gassing.
Transitional phrase: While safety seems obvious, most accidents occur during routine procedures. Real-world example: A 2023 OSHA report attributed 37% of forklift battery incidents to improper jump-start attempts. Pro Tip: Always test battery compartment structural integrity – corrosion weakens support rails over time.
How to verify third-party battery compatibility?
Certify replacements meet EN 60254-2 standards for industrial batteries. Check UL certification for North American markets or TUV Rheinland for European compliance. Cross-reference vendor spec sheets against OEM current derating curves.
Transitional phrase: Documentation review separates adequate from optimal solutions. Pro Tip: Require vendors to provide 72-hour load bank test reports – this verifies actual vs claimed capacity under realistic discharge profiles.
Redway Battery Expert Insight
FAQs
Lead-acid variants last 3–5 years with proper watering; lithium batteries achieve 7–10 years with full maintenance cycles.
Can I use automotive batteries instead?
Never – automotive SLI batteries can’t handle deep cycling and may fail catastrophically under forklift loads.
How often should battery water levels be checked?
Weekly in heavy use – maintain plates 6–8mm below filler necks to prevent acid stratification.
Forklift Battery Charging Station: A Comprehensive Guide
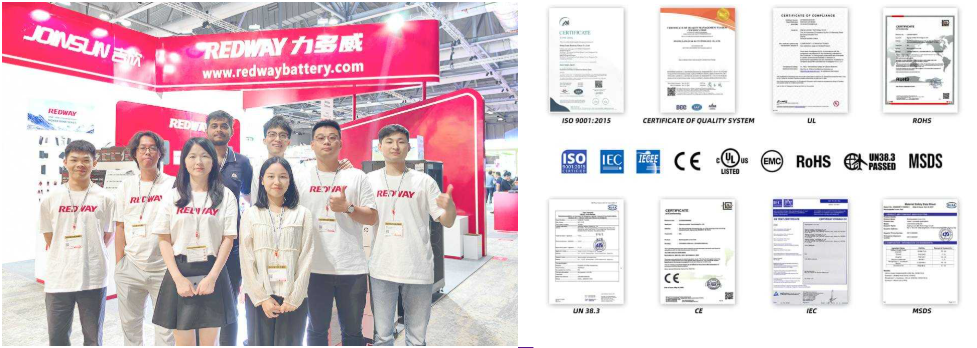