Forklift batteries fall into three primary categories: lead-acid (flooded or sealed), lithium-ion (LiFePO4), and hydrogen fuel cells. Lead-acid remains popular for low upfront costs, while lithium-ion dominates for fast charging, higher energy density, and zero maintenance. Heavy-duty applications (e.g., 48V, 600–1,200Ah) prioritize durability, whereas compact electric forklifts benefit from lightweight lithium options. Proper charging protocols and electrolyte management are critical for lifespan. How to Convert Ah to kWh: Formula and Calculator
What are the primary types of forklift batteries?
Lead-acid, lithium-ion, and fuel cell batteries power modern forklifts. Flooded lead-acid offers affordability, while lithium-ion excels in fast charging (1–2 hours) and 2,000–5,000 cycle lifespans. Hydrogen fuel cells suit continuous-use environments with instant refueling but require infrastructure.
Flooded lead-acid batteries use liquid electrolytes, needing weekly watering and ventilation due to hydrogen emissions. Lithium-ion variants, like LiFePO4, operate maintenance-free with built-in Battery Management Systems (BMS) to prevent overcharging. For example, a 48V 800Ah LiFePO4 battery reduces downtime by charging during lunch breaks. Pro Tip: Match battery capacity to duty cycles—undersized packs degrade rapidly in high-throughput warehouses. Mechanics often prioritize lead-acid for budget fleets but underestimate lithium’s TCO savings. But how do you balance upfront costs vs. long-term efficiency?
Wholesale lithium golf cart batteries with 10-year life? Check here.
Lead-acid vs. lithium-ion: Which is better?
Lithium-ion batteries outperform lead-acid in lifespan and efficiency but cost 2–3× more upfront. Lead-acid suits low-duty cycles; lithium dominates multi-shift operations with rapid charging.
Lead-acid batteries deliver 1,000–1,500 cycles at 50% depth of discharge (DoD), while lithium-ion achieves 3,000–5,000 cycles at 80% DoD. Consider a warehouse running three shifts: lithium-ion’s 1-hour charging slashes downtime versus lead-acid’s 8-hour cooling period. However, lead-acid’s lower initial cost appeals to small businesses. Pro Tip: Calculate energy needs using Ah × Voltage × DoD—e.g., 48V 600Ah at 80% DoD = 23 kWh usable. Transitional phrase: While lithium seems superior, lead-acid still holds niche advantages. For instance, cold storage warehouses (-20°C) often stick with robust flooded models.
Want OEM lithium forklift batteries at wholesale prices? Check here.
Factor | Lead-Acid | Lithium-Ion |
---|---|---|
Cost per kWh | $100–$150 | $300–$500 |
Cycle Life | 1,000–1,500 | 3,000–5,000 |
Charging Time | 8–10 hours | 1–3 hours |
How do flooded lead-acid batteries work?
Flooded lead-acid batteries rely on liquid sulfuric acid and lead plates. During discharge, acid reacts with plates, producing electricity and water. Charging reverses the reaction.
These batteries require regular watering to maintain electrolyte levels and prevent plate exposure. A 36V 750Ah model weighs ~1,200 kg, necessitating sturdy forklift frames. Overcharging causes excessive gassing and water loss. Pro Tip: Use automated watering systems to minimize maintenance labor. Transitional phrase: Despite their heft, flooded batteries handle high surge currents better than most lithium counterparts. For example, paper mills use them for heavy pallet lifting. But what happens if maintenance is neglected? Corrosion and sulfation can permanently reduce capacity by 40%.
What are the advantages of lithium-ion forklift batteries?
Lithium-ion batteries offer 95% efficiency, partial charging, and no maintenance. They’re 30–50% lighter than lead-acid, reducing forklift wear.
With integrated BMS, lithium-ion prevents over-discharge and thermal runaway. A 48V 600Ah LiFePO4 battery lasts 10+ years with 2–3 daily charges, ideal for refrigerated warehouses. Transitional phrase: Beyond performance, lithium’s compact size allows innovative forklift designs. Pro Tip: Avoid charging below 0°C to prevent lithium plating. Ever wondered why Amazon’s warehouses favor lithium? It’s the 30-minute opportunity charging during shifts that boosts uptime by 20%.
Feature | Lithium-Ion | Lead-Acid |
---|---|---|
Energy Density | 100–265 Wh/kg | 30–50 Wh/kg |
Maintenance | None | Weekly |
Operating Temp | -20°C–60°C | 0°C–40°C |
Are there specialized forklift batteries for extreme environments?
Nickel-based batteries (NiCd/NiFe) and hydrogen fuel cells serve extreme temperatures or continuous use. NiCd performs at -40°C, while fuel cells refuel in minutes.
In freezer storage (-30°C), lithium-ion’s efficiency drops below 70%, but nickel-cadmium maintains 85% capacity. Fuel cells, though expensive, excel in ports running 24/7. Pro Tip: Pair hydrogen fuel cells with solar-powered electrolyzers for greener logistics. Transitional phrase: While niche, these solutions address critical industrial challenges. For instance, a Tyson Foods freezer facility reduced downtime by 35% after switching to NiCd.
How to maintain forklift batteries for maximum lifespan?
For lead-acid: Water weekly, equalize monthly, and clean terminals. Lithium-ion needs clean, dry storage and firmware updates.
Lead-acid batteries require specific gravity checks (1.277–1.299) to monitor charge. Equalization charges prevent sulfation—apply 58.8V to a 48V battery monthly. Transitional phrase: Proper care extends lifespan significantly. Pro Tip: Document charging cycles; overcharging lithium-ion beyond 4.2V per cell degrades capacity. Imagine a 48V lead-acid battery lasting 5 years instead of 3—just by following watering schedules.
Redway Battery Expert Insight
FAQs
Yes, but opportunity charging during breaks is better. Full 0–100% cycles stress cells; partial charges (20–80%) extend lifespan.
Is retrofitting lead-acid forklifts to lithium-ion feasible?
Yes, but verify compatibility. Lithium’s lighter weight may require counterweight adjustments. Always upgrade chargers to avoid voltage mismatches.
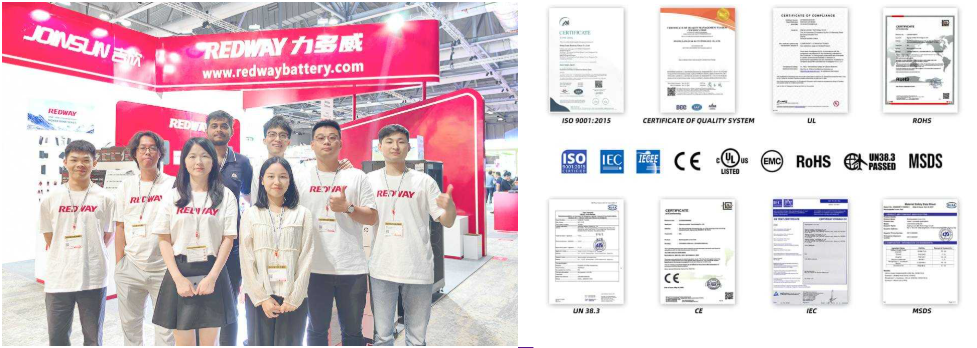