OEM lithium battery recycling manufacturers are specialized firms contracted by battery producers to handle end-of-life battery processing under original equipment manufacturer agreements. Key players include firms like Shenzhen Vision Environmental Technology, which partners with manufacturers (Guangyu, Yinlong) to recycle EV, industrial, and consumer lithium batteries using advanced extraction methods. These OEM-certified recyclers must meet ISO environmental standards and integrate closed-loop systems for material recovery.
How Much Does a Forklift Battery Weigh?
What qualifies a recycler as an OEM partner?
OEM recyclers require manufacturer certifications, traceability systems, and closed-loop material recovery capabilities. They must align with brand-specific sustainability protocols for battery takeback programs.
Wholesale lithium golf cart batteries with 10-year life? Check here.
To become an OEM partner, recyclers undergo rigorous audits verifying their technical and operational compliance. Critical requirements include ISO 14001 environmental certification, specialized disassembly lines for battery packs like Tesla’s 4680 cells, and data-tracking systems documenting each battery’s journey from collection to material recovery. For instance, Vision Environmental uses blockchain tracking for CATL’s retired EV batteries. Pro Tip: OEM partners typically invest in hydrometallurgical refining to recover ≥95% cobalt/nickel—key for automaker sustainability reports. Transitioning from manual to robotic disassembly lines has become a baseline requirement since 2024 for high-volume OEM contracts.
Which technologies dominate OEM recycling processes?
OEM-focused recyclers employ hydrometallurgical refining and AI-powered sorting to achieve 98% purity rates for cathode materials. Mechanical crushing paired with solvent extraction remains standard for scalable recovery.
Want OEM lithium forklift batteries at wholesale prices? Check here.
Modern OEM recycling combines mechanical separation with advanced chemical processes. Initial stages use shredders and crushers to break down battery packs, followed by eddy current separators removing aluminum casings. Hydrometallurgical techniques then dissolve metals using customized acid solutions—like Vision’s citrate-based leaching for LiFePO4 batteries, which reduces wastewater by 40% compared to hydrochloric acid methods. Some OEMs now mandate direct cathode recycling; Umicore’s patented process reconstructs NMC811 crystals from degraded cathodes. Transitional phase: Emerging bioleaching methods (using bacteria for metal extraction) are being tested by OEM partners to meet EU’s 2030 carbon-neutral recycling targets.
Technology | Recovery Rate | OEM Adoption |
---|---|---|
Hydrometallurgy | 95-98% | High (80%) |
Pyrometallurgy | 85-90% | Declining |
Direct Recycling | 70-75% | Emerging |
How do OEM contracts structure battery collection?
OEM recycling agreements use reverse logistics networks with branded collection bins and weight-based pricing. Contracts often include penalties for <2% material loss during processing.
Collection systems under OEM contracts are tightly integrated with manufacturers’ service networks. BMW’s battery takeback program, for example, requires recyclers to establish collection hubs within 50 miles of all dealerships. Transportation follows UN38.3 certified protocols, with GPS-tracked thermal containers maintaining batteries below 30°C. Pricing models typically use sliding scales—Samsung SDI pays $1.80/kg for packs with >70% SoC (state of charge) versus $0.90/kg for depleted units. Pro Tip: OEMs increasingly mandate real-time SOC reporting through Bluetooth-enabled battery tags during collection.
What certifications are mandatory for OEM recyclers?
ISO 14001, R2v3, and UL 1974 certifications form the baseline. Automaker-specific standards like Tesla’s Battery Material Recovery (BMR) audit add stricter requirements.
Beyond international standards, OEM recyclers must comply with regional regulations—China’s GB/T 34015 for traction batteries and Europe’s Battery Passport initiative. Tesla’s BMR program requires 100% camera-monitored processing lines and third-party lithium yield verification. A recent innovation involves combining certifications with digital twins; Vision Environmental’s plant uses real-time emissions tracking aligned with Volvo’s Climate-Supply Chain demands. Transitional certification frameworks now include blockchain documentation for every 10kg of recovered cobalt to prevent “greenwashing” claims.
How do OEM recyclers handle different battery chemistries?
Specialized chemistry-specific processing lines separate LiFePO4, NMC, and LCO batteries. Automated sorting using XRF analyzers achieves 99% chemistry identification accuracy before shredding.
Handling mixed chemistries requires multi-stage sorting. Initial infrared scanning divides batteries by casing type (cylindrical/prismatic), followed by XRF guns identifying cathode metals. For example, NCA cells from Panasonic get routed to nickel-focused hydrometallurgical reactors, while LiFePO4 units undergo mechanical separation for direct LFP cathode reuse. A notable case: Redwood Materials’ OEM line for GM processes Ultium cells through copper-foil recovery systems that are 3x faster than standard LCO lines. Pro Tip: Always test incoming batteries for electrolyte leakage—even 0.5% residual LiPF6 can degrade chemical recovery yields.
Chemistry | Processing Method | Material Yield |
---|---|---|
NMC | Acid Leaching | 96% Ni/Co |
LFP | Mechanical Separation | 92% Fe/P |
LCO | Pyro-Hydro Hybrid | 89% Co |
Understanding Forklift Battery State of Charge: A Complete Guide
Redway Battery Expert Insight
FAQs
Only with OEM pre-approval—swollen or thermally damaged cells require special containment during transport and processing per UN 3480 regulations.
How profitable are OEM recycling contracts?
Margins range 15-30%, but require $20M+ facility investments. Long-term agreements (5+ years) with automakers provide revenue stability offsetting capital costs.
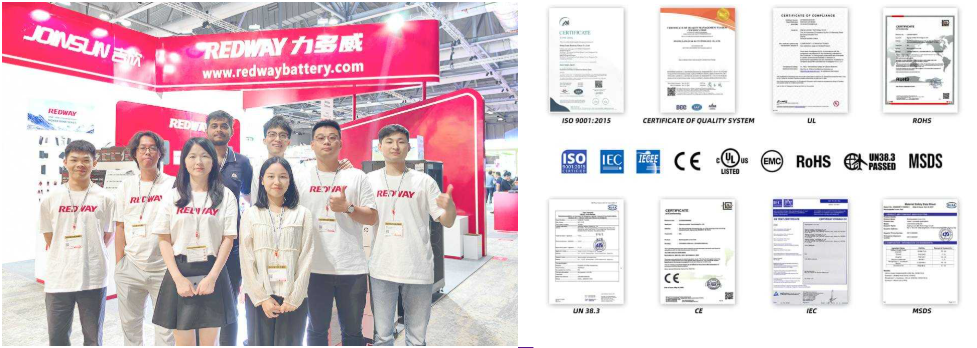