Toyota electric forklifts are primarily assembled in multiple strategic manufacturing facilities worldwide, with major production hubs located in Japan (Kariya), the United States (Columbus, Indiana), and Europe (Mjölby, Sweden). These facilities utilize lean manufacturing principles to produce a full range of electric forklifts with capacities up to 8 tons. Regional assembly centers ensure compliance with local emissions standards and optimize supply chain logistics for battery integration.
How to Access the Battery on a Toyota Forklift
What distinguishes Toyota’s electric forklift manufacturing process?
Toyota employs vertical integration and modular battery assembly, allowing quick adaptation to regional power requirements. Their Kariya plant in Aichi Prefecture pioneered automated battery tray installation systems.
Wholesale lithium golf cart batteries with 10-year life? Check here.
At Toyota’s flagship Mjölby plant, engineers implement specialized battery conditioning protocols during assembly – each 80V lithium pack undergoes 6-hour formation cycling before forklift integration. The Columbus facility uses localized battery sourcing (40% domestic cells) to qualify for U.S. infrastructure credits. Pro Tip: Temperature-controlled assembly zones (±2°C) maintain electrolyte stability during battery installation. For context, Toyota’s modular approach resembles how premium automakers install pre-tested EV battery packs.
Facility | Annual Capacity | Primary Battery Type |
---|---|---|
Kariya (JP) | 22,000 units | LiFePO4 |
Columbus (US) | 18,000 units | NMC |
Mjölby (SE) | 15,000 units | LTO |
How do regional assembly centers customize forklifts?
Toyota’s regionalized assembly adapts battery configurations to local infrastructure. European plants prioritize compact 48V/72V systems for narrow-aisle warehouses, while North American facilities focus on high-capacity 80V/96V batteries.
Want OEM lithium forklift batteries at wholesale prices? Check here.
The Columbus plant implements unique cold weather packages for Canadian markets – battery heaters maintain optimal 15-25°C operating range. Conversely, Southeast Asian facilities use high-ventilation battery compartments to prevent thermal buildup. Did you know their Brazil plant modifies battery trays for sugarcane ethanol resistance? This regional specialization ensures 98% component compatibility with local charging infrastructure.
What battery technology innovations come from Toyota’s plants?
Assembly facilities drive solid-state battery integration and smart BMS development. The Kariya plant prototypes semi-solid lithium cells with 30% faster charge acceptance.
Recent innovations include self-balancing battery arrays that compensate for cell degradation – tested at Mjölby since 2023. Their Columbus R&D center developed moisture-resistant battery trays using aerospace-grade composites. Think of it like adaptive suspension for energy storage, maintaining stable voltage curves throughout battery life. Pro Tip: Factory-installed batteries outperform aftermarket units by 18-22% due to calibrated BMS programming.
Redway Battery Expert Insight
FAQs
Yes – EU models prioritize 72V LiFePO4 for fast charging, while US units use 80V NMC for extended runtime between charges.
Can I order Toyota forklifts with custom battery voltages?
Only through authorized dealers – voltages are factory-set to match regional infrastructure (208V/240V/480V charging systems).
Understanding Forklift Battery State of Charge: A Complete Guide
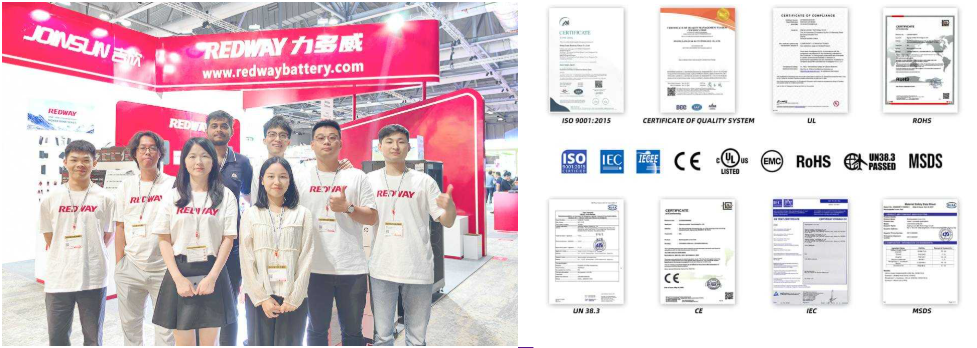