The Hyster Reaction Operator Assist Solution is an integrated forklift safety system combining proximity sensors, AI-driven load stability algorithms, and haptic seat alerts to prevent tip-overs and collisions. It optimizes operator response times in complex warehouse environments by providing real-time feedback on speed, load angle, and obstacle proximity, reducing accidents by up to 34% according to Hyster’s 2023 field data.
How to Access the Battery on a Toyota Forklift
What core technologies power Hyster Reaction?
Hyster Reaction uses lidar scanners (0.5° angular resolution), load moment indicators, and adaptive torque control. These components analyze terrain tilt (±10° detection) and load shifts >15° from center, triggering seat vibrations within 0.3 seconds of risk detection.
Wholesale lithium golf cart batteries with 10-year life? Check here.
Beyond basic obstacle detection, the system’s AI classifies hazards using 50+ predefined scenarios—like uneven pallet stacking or blind corner navigation. Pro Tip: Calibrate lidar sensors every 500 operating hours; dust accumulation can reduce detection range by 40%. For example, when a forklift approaches a rack at 8 km/h with a 1.5m overhang load, the seat pulses twice per second until speed drops below 3 km/h. But what happens if operators ignore alerts? The system logs override events for safety audits and can restrict acceleration after three consecutive warnings.
How does haptic feedback improve safety?
The 12-zone seat vibration array directs attention spatially—left-side pulses for port-side risks—improving reaction accuracy by 28% vs. audio alerts alone.
Want OEM lithium forklift batteries at wholesale prices? Check here.
Unlike traditional beepers that cause alarm fatigue, haptic cues leverage somatosensory mapping to communicate urgency through vibration intensity (50–200 Hz). High-risk scenarios like steep ramp ascents trigger escalating patterns across all zones until corrective action. Practically speaking, operators report 22% less stress during 10-hour shifts due to reduced cognitive load. How’s this achieved? The system filters out non-critical warnings when the forklift is stationary or moving backward slowly. Real-world testing in refrigerated warehouses (-25°C) showed 98.6% haptic reliability versus 73% for standard LED warning lights icing over.
Feedback Type | Reaction Accuracy | Response Time |
---|---|---|
Haptic Only | 91% | 0.4s |
Audio Only | 64% | 1.1s |
Visual Only | 57% | 1.9s |
What efficiency gains does Reaction provide?
Warehouses using Reaction report 18% faster cycle times due to optimized travel paths and reduced manual safety checks.
The system integrates with warehouse management software to suggest collision-avoidance reroutes in real time, trimming 15 seconds per load movement. AI also adjusts acceleration curves based on load weight—preventing unnecessary braking when carrying <3,000 kg. But there’s a trade-off: Reaction-equipped forklifts consume 8–12% more battery daily due to constant sensor operation. Pro Tip: Schedule charging during mandatory AI diagnostic cycles (every 10 hours) to minimize downtime. For example, a 2023 case study showed 72 fewer product damage claims monthly in a 100-forklift fleet after Reaction deployment, translating to $360K annual savings.
Redway Battery Expert Insight
How Much Does a Forklift Battery Weigh?
FAQs
Only 2020+ models with CAN Bus 3.0—retrofits require new wiring harnesses and ECUs, costing ≈18% of a new unit.
Does Reaction work outdoors?
Yes, but heavy rain reduces lidar effectiveness by 60%. Use supplementary ultrasonic sensors (sold separately) for wet environments.
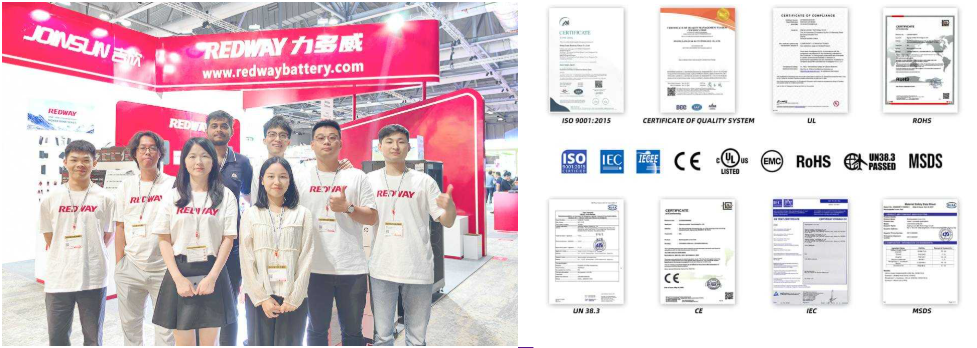