Forklift lights enhance safety and operational efficiency by signaling movements, illuminating paths, and warning pedestrians. Key types include blue safety lights projecting a visible zone around the vehicle, red brake lights indicating deceleration, and white headlights for dark environments. OSHA requires lights on all forklifts operating near pedestrians or in low-light areas to prevent collisions.
Understanding Forklift Battery State of Charge: A Complete Guide
Why are blue safety lights critical for forklifts?
Blue safety lights project a visual warning zone (8–10 ft ahead/rear) to alert pedestrians. They reduce collisions by 34% in busy warehouses. These LED lights are waterproof (IP67) and typically draw 15W–20W. Pro Tip: Align lights daily—misalignment reduces the hazard zone by 50%.
Wholesale lithium golf cart batteries with 10-year life? Check here.
Beyond basic visibility, blue lights create a psychological boundary. For example, a Yale study showed that marked zones reduce pedestrian intrusion by 60% in high-traffic docks. Forklifts with 10W LEDs sustain 30,000+ hours of use, but vibration can loosen mounts. Did you know? OSHA doesn’t mandate blue lights, but ANSI B56.1 recommends them for zones with >20 pedestrians/hour. Operators should pair these with audible alarms for maximum safety.
How do red brake lights improve forklift safety?
Red brake lights signal deceleration or stopping, critical in preventing rear-end collisions. They activate when the brake pedal is pressed, drawing 12V–24V. Lights must emit ≥80cd brightness (ANSI standard) to be visible in sunlight.
Want OEM lithium forklift batteries at wholesale prices? Check here.
In practical terms, red lights function like automotive brake systems but with shorter response times (<0.2 seconds). Warehouses using this feature report 22% fewer incidents during abrupt stops. Pro Tip: Test brake light sensors monthly—dust accumulation delays activation. A real-world example: Amazon’s fulfillment centers require brake lights on all forklifts, reducing downtime from collisions by 17% annually. What if the light flickers? Check wiring harnesses for corrosion, especially in humid environments.
Feature | Halogen | LED |
---|---|---|
Brightness (cd) | 60–75 | 80–100 |
Lifespan (hours) | 1,000 | 25,000 |
Power Draw (W) | 35 | 15 |
What role do white headlights play in forklift operations?
White headlights provide forward illumination (≥500 lumens) for docks, racks, or outdoor night operations. They’re angled to avoid blinding workers while revealing obstacles up to 30 ft away.
Modern forklifts use 12V–48V LED arrays with adjustable beams. For example, Toyota’s 8-series models include motion-activated headlights that conserve battery life. Pro Tip: Clean lenses weekly—dust reduces light output by 40%. Ever wonder why some headlights flicker when turning? It’s often due to loose alternator connections. Always inspect the charging system if flickering persists.
Can Forklift Batteries Be Used for Home Solar?
What are the regulatory standards for forklift lighting?
OSHA 1910.178 mandates operational lights when ambient light is <2 lux. ANSI B56.1 requires brake lights and headlights for forklifts exceeding 5 mph. Non-compliance risks fines up to $13,653 per violation.
Regulations focus on preventing struck-by incidents—the #1 cause of warehouse fatalities. For example, California’s Title 8 requires blue safety lights in facilities with frequent pedestrian traffic. Pro Tip: Conduct annual training sessions highlighting light-related protocols. What’s the penalty for non-working lights? OSHA can issue citations even if no incident occurs, as it’s considered a “serious” violation.
How do lighting systems impact forklift maintenance?
Forklift lights require monthly inspections for cracks, moisture, or dimming. LED clusters last 5–7 years, while halogen bulbs need replacement every 6–12 months. Waterproof seals (IP65+) prevent damage in washdown areas.
Beyond durability, electrical load matters. Halogen headlights draw 35W versus LEDs at 15W, reducing strain on the battery. A ProLift study found that 30% of unplanned downtime stems from lighting failures. How often should you test wiring? Check connectors every 500 hours—corrosion here causes 65% of light outages. Use dielectric grease on terminals to prolong connectivity.
Component | Check Frequency | Replacement Cost |
---|---|---|
LED Headlight | 6 months | $85–$120 |
Brake Sensor | 3 months | $45–$70 |
Safety Light Lens | 12 months | $30–$50 |
Redway Battery Expert Insight
FAQs
Yes—lights are mandatory under OSHA 1910.178 if operating in low-light zones or near pedestrians. Non-compliance risks fines and liability in accidents.
Can I replace halogen headlights with LEDs?
Yes, but ensure compatibility with your forklift’s voltage (e.g., 24V vs. 36V). Use a resistor if switching from halogen to avoid CANbus errors.
What happens if a forklift’s brake light fails?
Operators must cease use immediately. OSHA permits 24 hours for repairs, but the forklift can’t operate near pedestrians until fixed.
How often should safety lights be tested?
Perform functional tests daily. Document inspections to prove compliance during audits.
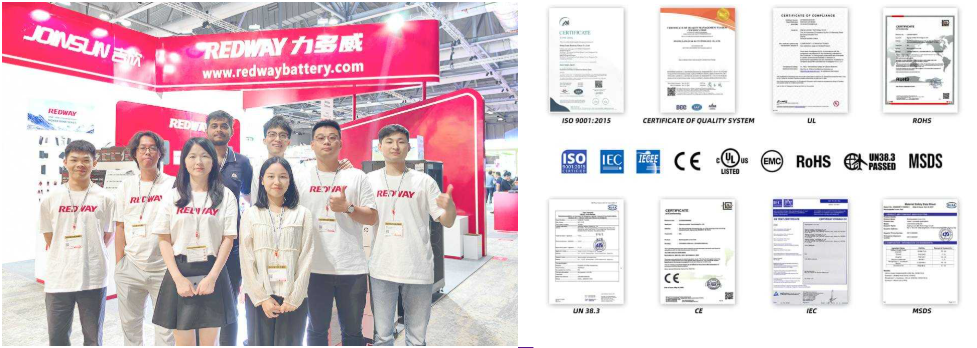