The 85-13 industrial cell is a 6V lead-acid battery cell designed for heavy-duty applications requiring high surge current and deep-cycle resilience. Commonly used in electric forklifts, floor scrubbers, and airport ground support equipment, these cells feature thick Pb-Ca plates (8.5×13 cm plate size) and sulfuric acid electrolytes. They withstand 1,500+ cycles at 80% depth of discharge (DoD) when maintained with regulated charging (7.3–7.45V per cell).
How to Access the Battery on a Toyota Forklift: A Complete Guide
What defines the 85-13 industrial cell?
The 85-13 cell refers to standardized plate dimensions (8.5 cm x 13 cm) dictating capacity and current output. These cells operate at 6V nominal voltage, with 550–700Ah capacities, optimized for deep-cycle industrial workloads like electric forklift propulsion or pallet jack systems.
Wholesale lithium golf cart batteries with 10-year life? Check here.
Unlike automotive SLI batteries, 85-13 cells prioritize thick plates (4–5 mm) to minimize corrosion during repetitive deep discharges. A typical 24V forklift battery uses four cells in series, weighing ~250 kg. Pro Tip: Always maintain electrolyte levels 3–5 mm above plates to prevent sulfation. For example, an 85-13 cell discharged to 20% SOC daily lasts 3–5 years versus 1–2 years if drained below 10%. Transitionally, while lithium alternatives exist, lead-acid remains cost-effective for high-uptime environments.
What are the technical specifications of 85-13 cells?
Key specs include 6V nominal voltage, 570–720Ah capacity (C20 rating), 58–62 kg weight per cell, and 300–500 cycle life at 50% DoD. Terminal configurations use SAE posts or threaded studs for high-current lugs (up to 500A surges).
Want OEM lithium forklift batteries at wholesale prices? Check here.
Electrolyte density ranges from 1.265–1.295 specific gravity when fully charged. Charging requires constant current until 7.35V/cell, then constant voltage until current drops below 2% of C20. Practically speaking, 85-13 cells need monthly equalization charges (7.5V/cell for 2–4 hours) to prevent stratification. Did you know? A 48V system with eight cells can deliver 25 kW bursts for lifting 2-ton loads. However, ambient temperatures above 40°C accelerate water loss by 30%.
Parameter | 85-13 Cell | DIN 43556 Cell |
---|---|---|
Voltage | 6V | 2V |
Typical Capacity | 650Ah | 1100Ah |
Application | Forklifts | Telecom Backup |
Why choose 85-13 cells over lithium-ion for industrial use?
85-13 cells offer lower upfront costs (50–70% cheaper than LiFePO4) and tolerance to harsh environments (-20°C to 50°C). They’re preferable where rapid replacement matters—swapping a failed lead-acid cell takes minutes versus BMS-protected lithium packs needing recalibration.
Lithium batteries falter in high-vibration settings due to welded internals, whereas 85-13 cells have mechanically robust inter-cell connections. For example, paper mills using lead-acid report 40% lower downtime versus lithium units. But what about energy efficiency? Lead-acid averages 75–85% efficiency versus lithium’s 95%, but this gap narrows in partial-SOC applications. Transitionally, hybrid systems now pair 85-13 cells with supercapacitors for peak shaving, extending cycle life by 30%.
How to maintain 85-13 battery systems?
Maintenance focuses on electrolyte levels, terminal cleaning, and temperature-compensated charging. Water must be added every 10–15 cycles using deionized water to avoid mineral contamination. Terminal corrosion is reduced via anti-oxidant sprays.
Hydrometers or refractometers should verify specific gravity monthly. Did you know? Overwatering dilutes electrolyte, reducing capacity by 5–8% per incident. Pro Tip: Schedule equalization charges during off-peak hours to avoid workplace disruptions. A real-world example: Logistics centers using automated watering systems cut maintenance labor by 70% while extending cell life to 7 years.
Maintenance Task | Frequency | Tool |
---|---|---|
Water Topping | Biweekly | Deionized Water Bottle |
Terminal Cleaning | Quarterly | Wire Brush + Baking Soda |
Equalization | Monthly | Programmable Charger |
Are 85-13 cells compatible with modern battery tech?
Yes, 85-13 cells integrate with IoT battery monitors and automated watering systems. Advanced chargers adjust profiles based on real-time temperature and sulfation data, boosting efficiency by 15–20%.
Some facilities retrofit lead-acid systems with partial lithium banks for peak demands, but this requires diode isolators to prevent voltage clashes. But isn’t mixing chemistries risky? Absolutely—it’s only viable with professional oversight. Transitionally, hydrogen recombination caps now reduce watering needs by 50%, cutting OpEx costs. For example, a German auto plant slashed water usage by 3,000 liters annually after upgrading their 85-13 cells with recombinant vents.
How Much Does a Forklift Battery Weigh?
Redway Battery Expert Insight
FAQs
Not recommended—lead-acid requires daily full charging, which solar can’t consistently provide. Use lithium or AGM batteries instead.
Why choose 85-13 over 2V traction cells?
85-13 systems simplify wiring with fewer interconnects, reducing resistance losses in 24–80V industrial equipment.
How often should 85-13 cells be replaced?
Every 4–6 years, depending on discharge depth. Capacity below 60% of initial C20 rating indicates replacement.
Are 85-13 cells recyclable?
Yes—98% of lead and plastic is recoverable. Always return spent cells to licensed recyclers.
What causes terminal corrosion in 85-13 cells?
Acid mist reacts with copper, forming conductive sulfate crystals. Apply silicone grease to minimize oxidation.
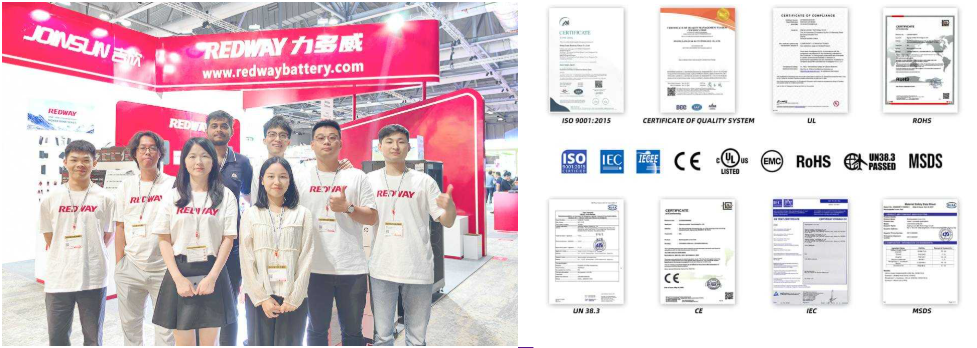