Mid Columbia Forklift, Inc. is a Pacific Northwest-based material handling specialist providing sales, service, and parts for forklift brands like Toyota and Hyster since 1985. They focus on electric and internal combustion (IC) forklifts, offering customized solutions for warehousing, logistics, and manufacturing. Their certified technicians handle repairs, battery refurbishment, and fleet management, with a strong emphasis on lithium-ion upgrades and energy-efficient systems. How Much Do Different Forklift Batteries Weigh by Type?
What services does Mid Columbia Forklift offer?
Their core services include forklift sales (new/used), preventive maintenance, emergency repairs, and OEM parts supply. They also provide battery reconditioning, fleet telematics, and operator training programs.
Beyond standard repairs, Mid Columbia specializes in retrofitting older forklifts with modern lithium-ion batteries—doubling lifespan while cutting energy costs by 30–40%. Technicians use diagnostic tools like CANbus analyzers to troubleshoot controllers and hydraulic systems. Pro Tip: Schedule pre-season maintenance in Q3 to avoid winter downtime spikes. For example, a Vancouver food distributor reduced fleet failures by 75% after adopting their predictive maintenance package. Why risk unplanned stoppages when proactive care saves thousands annually?
Wholesale lithium golf cart batteries with 10-year life? Check here.
Where does Mid Columbia Forklift operate?
Primarily serving Washington, Oregon, and Idaho, they support clients from warehouses to agricultural hubs. Mobile teams reach remote sites within 24 hours.
Their 12,000 sq ft Pasco headquarters houses a repair bay, parts inventory, and demo units. Service areas span 200+ miles—essential for rural sectors like Yakima’s fruit-packing industry. Transitionally, their logistics network partners with regional freight carriers to expedite parts delivery. Imagine a Boise fulfillment center needing same-day motor replacements; Mid Columbia’s stocked bearings and drive gears prevent 48-hour shipment waits. Pro Tip: Use their online parts portal (24/7 access) with cross-reference databases for discontinued models.
Want OEM lithium forklift batteries at wholesale prices? Check here.
Service Tier | Response Time | Coverage |
---|---|---|
Priority | 4 hrs | Urban |
Standard | 24 hrs | Rural |
What differentiates Mid Columbia from competitors?
They combine 40+ years’ expertise with EV-certified technicians and in-house battery reconditioning labs—unlike general equipment firms.
Their technicians hold ASE and Forklift Pro certifications, tackling complex issues like AC drive motor overhauls or CANbus communication errors. Meanwhile, competitors often subcontract battery work, increasing costs and delays. Practically speaking, a Tacoma lumber mill saved $8,200/year by switching to Mid Columbia’s refurbished battery program. How many repair shops offer lithium-ion conversions with real-time remote monitoring? Additionally, their “Forklift HealthCheck” AI tool predicts failures 3 weeks in advance using usage data.
Feature | Mid Columbia | Generic Shop |
---|---|---|
Battery Rebuilds | In-house (48h) | Outsourced (7d) |
Diagnostic Tech | CANbus+Thermal Imaging | Multimeter Only |
Do they handle industrial battery services?
Yes—they recondition, replace, and recycle lead-acid/lithium forklift batteries. Services include watering, equalization, and capacity testing.
Their battery shop uses Midtronics testers to detect weak cells before failure. For lithium upgrades, they install compatible BMS units and chargers—key for maximizing cycle life. Consider a Spokane cold storage facility: Switching to Mid Columbia’s LiFePO4 batteries cut charging time from 8 hours to 2.5 while withstanding -20°F conditions. Pro Tip: Always test battery Specific Gravity monthly; values below 1.225 indicate sulfation needing immediate equalization. Ever wonder why some batteries fail prematurely? Poor watering schedules cause 74% of lead-acid breakdowns.
Why choose Mid Columbia for forklift needs?
Clients gain single-point accountability—from procurement to decommissioning—plus 24/7 support and transparent pricing.
They offer lifetime service guarantees on repairs and performance-based leasing contracts. Transitionally, their customer portal provides repair histories and cost analytics. Picture a Portland e-commerce hub tracking 50 lifts’ uptime via custom dashboards—integrating with ERP systems. Why juggle multiple vendors when Mid Columbia streamlines compliance, safety, and budgeting? Plus, they’re one of six Northwestern dealers certified for Toyota System4 stability updates.
Redway Battery Expert Insight
FAQs
Yes—they’re factory-authorized for Hyster, Yale, and Clark models, plus unofficial support for Crown and Raymond with OEM-approved parts.
How long has Mid Columbia operated?
Since 1985, with 37 years specializing in electric forklift systems and battery innovations.
Do they serve residential clients?
Primarily commercial/industrial, but homeowners with small warehouse lifts can access parts and repairs.
Can they replace lead-acid with lithium batteries?
Yes, via turnkey retrofits including charger upgrades and BMS integration, typically paid back in <2 years via energy savings.
Do they offer on-site repair services?
24/7 mobile teams handle everything from battery swaps to transmission overhauls at customer facilities.
What warranty applies to refurbished batteries?
12–18 months, depending on AH capacity and usage cycles, with prorated replacement terms.
Forklift Battery Charging Station: A Comprehensive Guide
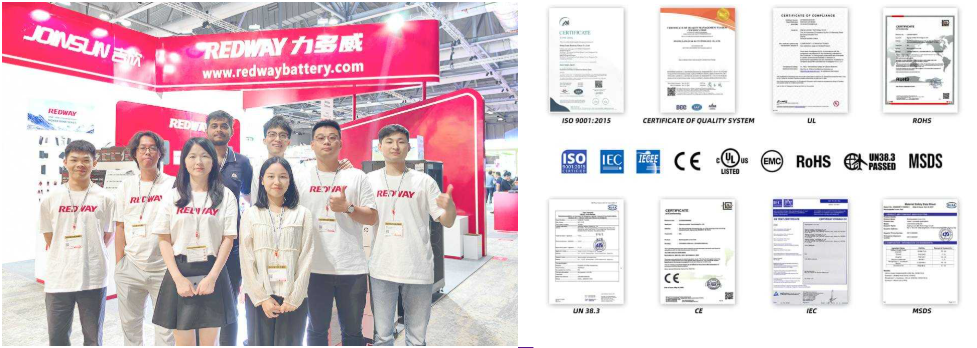