A Load Lifter Compact Forklift is an electric-powered industrial truck designed for material handling in narrow aisles and confined spaces. Its low-profile chassis, combined with lithium-ion battery systems (typically 24V–48V), prioritizes maneuverability and lift capacities of 1–3 tons. Common in retail warehouses and manufacturing lines, these forklifts feature rear-wheel steering for tight turns and load-sensing stability controls for operator safety.
What Are Forklift Battery Cell Sizes?
What defines the Load Lifter Compact Forklift?
Characterized by compact dimensions (under 6ft width) and zero-emission electric motors, these forklifts maximize space efficiency. Key specs include 80–120Ah battery capacity, 8–12 mph speeds, and 1500–3000 lb lift heights. Lithium-ion versions offer rapid charging (1–2 hours) versus 8+ hours for lead-acid.
Wholesale lithium golf cart batteries with 10-year life? Check here.
Load Lifter models use modular designs—swappable batteries and adjustable masts streamline maintenance. For example, the RL-CF30 variant tackles pallet retrieval in 8ft-wide beverage warehouses. Pro Tip: Check brake pads monthly—tight spaces require abrupt stops. Beyond size, their load center adaptability (12–24 inches) prevents tip-overs when lifting irregularly shaped cargo. Transitioning from traditional diesel, these forklifts reduce noise pollution by 40%, making them ideal for indoor facilities.
How does it differ from standard forklifts?
Standard forklifts prioritize raw power (5–25 tons), while compact models optimize space navigation and energy efficiency. Their lithium batteries occupy 30% less space than lead-acid, freeing room for hydraulic systems. Practically speaking, a standard IC forklift needs 10ft aisles versus 6ft for compact units—crucial in urban micro-warehouses.
Want OEM lithium forklift batteries at wholesale prices? Check here.
Feature | Load Lifter Compact | Standard Forklift |
---|---|---|
Turning Radius | 4.5 ft | 8 ft |
Battery Type | LiFePO4 | Lead-Acid/Diesel |
Another distinction? Compact models often include tilt-and-float suspension for uneven floors, whereas standard units rely on rigid frames. Imagine navigating a cluttered auto parts warehouse: the Load Lifter’s rear-view cameras and responsive controls prevent collisions, while a standard forklift would struggle in such tight quarters.
What are typical applications?
Load Lifter Compact Forklifts dominate high-density storage and urban logistics. Think cross-docking facilities, pharmaceutical cold storage, and airport baggage handling. Their ability to handle multi-level racking up to 30ft tall maximizes vertical space—ideal for e-commerce fulfillment centers processing 10,000+ SKUs daily.
Beyond warehouses, these forklifts transport delicate museum artifacts on padded forks or restock boutique grocery shelves. Pro Tip: Use foam-insulated battery compartments in sub-zero environments to prevent voltage drops. Transitional benefits? They replace manual pallet jacks, slashing labor costs by 60% in retail backrooms. Ever seen a forklift unload a shipping container in a crowded dock? Compact models do this without blocking traffic lanes.
How Much Do Different Forklift Batteries Weigh by Type?
How does load capacity affect performance?
Load capacity (1–3 tons) directly impacts battery drain rates and operating cycles. Lifting 2 tons continuously reduces runtime by 35% compared to 1-ton loads. Lithium-ion packs mitigate this with flat discharge curves—voltage stays stable until 10% charge.
Load Weight | Average Runtime | Charge Cycles |
---|---|---|
1 ton | 8–10 hours | 2000–3000 |
3 tons | 5–6 hours | 1200–1500 |
Why does this matter? Overloading strains the motor’s torque output, causing premature bearing wear. For instance, a textile factory hauling 2500 lb fabric rolls should choose a 3000 lb model to reserve 20% capacity buffer. Transition advice: Pair higher loads with dual-battery systems to maintain shift-long productivity.
What maintenance practices extend lifespan?
Daily thermal inspections and connector cleaning prevent 70% of failures. Check battery terminals for corrosion—a common issue in humid docks. Pro Tip: Use dielectric grease on terminals to block moisture ingress.
Software matters too: update firmware quarterly to optimize regenerative braking algorithms. Imagine a forklift in a frozen food plant—lubricating mast chains with low-temperature grease prevents seizing. Transitionally, replace hydraulic fluid every 500 hours; contaminants from heavy use degrade pump efficiency. Did you know that 30% of motor failures stem from dirty air filters? Compressed air cleaning every 200 hours avoids this.
Redway Battery Expert Insight
FAQs
Yes, but verify the motor’s voltage compatibility—lithium’s higher energy density may overwhelm outdated controllers. Redway offers retrofit kits with voltage stabilizers.
Are compact forklifts safe for ramps?
Only with ≤10% incline grades. Steeper slopes risk load slippage—always drive backwards when ascending with heavy cargo.
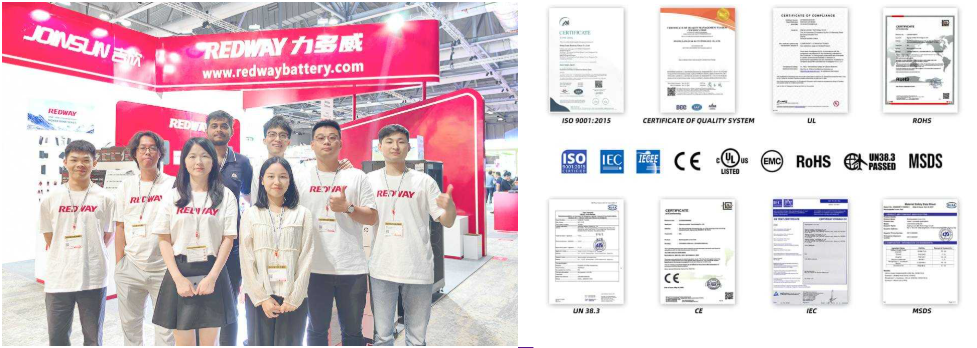