Fleet electrification for forklifts involves transitioning a company’s entire material handling fleet from internal combustion engines (ICE) to electric-powered units. This shift reduces carbon emissions, slashes fuel costs, and enhances warehouse air quality. Lithium-ion batteries dominate modern systems due to fast charging (1–2 hours) and 2,000–5,000 cycle lifespans, paired with smart chargers and telematics for real-time energy management. Pro Tip: Prioritize charger-fleet compatibility to avoid downtime from mismatched voltage or current ratings.
Understanding Forklift Battery State of Charge: A Complete Guide
What are the core components of forklift fleet electrification?
Key elements include lithium-ion battery packs, high-frequency chargers, and energy management software. Battery capacities range from 24V/200Ah for light loads to 80V/1200Ah for heavy-duty lifts. Pro Tip: Opt for modular battery designs to scale capacity as operational demands grow.
Wholesale lithium golf cart batteries with 10-year life? Check here.
Transitioning a fleet requires more than swapping ICE for electric forklifts. Lithium-ion systems need thermal management (cooling/heating) to maintain 15–35°C for optimal performance. Chargers must align with battery specs—48V systems, for instance, require 54.6V (LiFePO4) termination voltage. For example, a warehouse using 50×48V/600Ah forklifts would need 60kW chargers to refuel 30 units daily without bottlenecks. But how do you balance peak demand charges? Smart chargers with load-sharing cut power during grid spikes, reducing energy costs by 15–20%.
Want OEM lithium forklift batteries at wholesale prices? Check here.
Component | ICE Forklift | Electric Forklift |
---|---|---|
Energy Source | Diesel/LPG | Li-ion/PbA |
Maintenance Cost/Year | $1,200–$1,800 | $300–$500 |
How does electrification impact total cost of ownership (TCO)?
Electric forklifts cut TCO by 40–60% over 5 years despite higher upfront costs. Savings stem from lower energy ($0.08/kWh vs. $3/gallon diesel) and reduced maintenance.
While a diesel forklift costs $25,000 upfront vs. $35,000 for electric, the latter saves ~$15,000 in fuel/maintenance over 5 years. For fleets operating 3 shifts, fast charging (1–2 hours) slashes downtime versus 8-hour lead-acid charging. Imagine a 100-forklift fleet: electrification reduces annual CO2 by 450 tons, aligning with ESG goals. However, battery replacement every 5–7 years adds $4,000–$10,000 per unit. Pro Tip: Leasing batteries as a service (BaaS) converts upfront costs into monthly OPEX, easing cash flow.
Forklift Battery Charger Stand: Ensuring Safety and Efficiency in Your Charging Area
What infrastructure upgrades are necessary?
Facilities need 240V/480V AC charging stations, ventilation, and reinforced flooring (500–700 kg/m²). Electrical panels often require upgrades to handle 30–100kW per charger.
Beyond chargers, warehouses must install proper battery storage areas with fire suppression systems (NFPA 855 standards). For example, a 20,000 sq. ft. facility might need 10×50kW chargers, demanding a 500kW grid connection. Transitional phrases like “In practice” and “Consider this” help contextualize data. Lithium-ion’s 95% efficiency outperforms lead-acid’s 75%, but requires precise humidity control (30–50% RH). Pro Tip: Use aluminum racking to prevent corrosion from battery off-gassing.
Requirement | Lead-Acid | Lithium-ion |
---|---|---|
Charging Area Space | 30% More | Compact |
Ventilation Needs | High | Low |
Redway Battery Expert Insight
FAQs
Retrofitting is rarely cost-effective—motor mounts and hydraulics differ radically. New electric units offer better ROI with warranties and modern features.
How long do lithium forklift batteries last daily?
Li-ion packs provide 6–8 hours per charge (400–600 cycles/year). Fast-charging during breaks extends uptime by 1–2 hours vs. lead-acid.
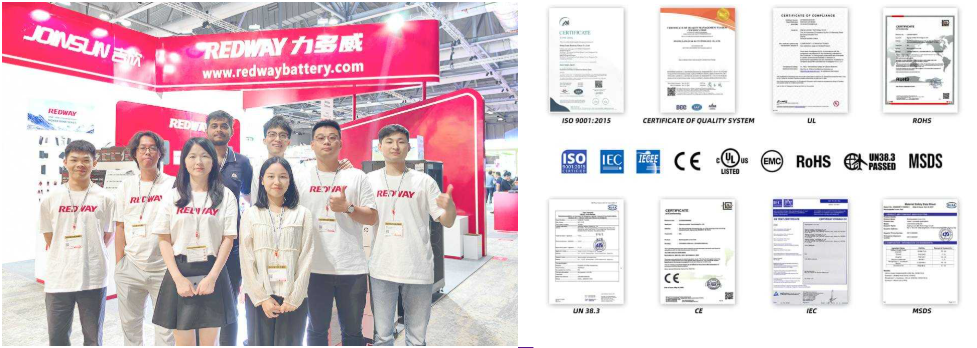