A heavy-duty forklift is engineered to lift and transport extremely heavy loads exceeding 15,000 lbs, commonly used in construction, steel manufacturing, and shipping industries. These machines feature reinforced frames, high-torque engines, and specialized attachments (e.g., drum handlers, crane hooks) to handle materials like steel coils, shipping containers, or industrial machinery. Pro Tip: Opt for electric heavy-duty models in warehouses to reduce emissions and noise.
How Much Does a Forklift Battery Weigh?
What industries rely on heavy-duty forklifts?
Industries like steel mills, construction sites, and port terminals depend on heavy-duty forklifts for moving multi-ton loads. They’re critical for stacking steel coils, loading container ships, and transporting pre-cast concrete slabs. Enhanced stability systems prevent tip-overs on uneven terrain.
Wholesale lithium golf cart batteries with 10-year life? Check here.
Heavy-duty forklifts handle loads up to 50,000 lbs, far exceeding standard models’ 10,000–15,000 lb limits. For example, a Hyster H450HD-EC electric forklift lifts 45,000 lbs using dual AC motors. Pro Tip: Regularly inspect load-bearing components like mast rollers and hydraulic cylinders—wear here risks catastrophic failure. Transitioning from warehouses to outdoor sites? Heavy-duty units often include all-terrain tires and weatherproofed electronics. But how do they maintain stability? Many use counterweights up to 12,000 lbs and wide wheelbases. A real-world analogy: Think of them as the semi-trucks of forklifts, built for endurance over precision.
Industry | Typical Load | Forklift Type |
---|---|---|
Steel Manufacturing | Steel Coils (20,000–40,000 lbs) | Reach Stackers |
Port Terminals | Shipping Containers (up to 50,000 lbs) | Container Handlers |
How do heavy-duty forklifts differ from standard models?
Heavy-duty forklifts have reinforced frames, higher lifting capacities, and specialized attachments. Standard models prioritize maneuverability, while heavy-duty versions focus on brute strength and durability under extreme loads.
Want OEM lithium forklift batteries at wholesale prices? Check here.
Unlike standard forklifts with single-stage masts, heavy-duty units use 3-stage masts reaching 30+ feet. They often integrate planetary axles for smoother load distribution. Pro Tip: Avoid using standard forklift tires—heavy-duty tasks require puncture-resistant solids or foam-filled types. Consider this: A Toyota 8FGCU25 (standard) lifts 5,000 lbs, while a Kalmar DCG460-120 (heavy-duty) handles 120,000 lbs. Transitionally, heavy-duty models sacrifice speed (max 12 mph vs 20 mph) for torque. Think of it like comparing a sprinter to a powerlifter—different physiologies for different goals.
What safety features are critical for heavy-duty forklifts?
Load moment sensors, ROPS/FOPS cabins, and automatic braking systems are essential. These prevent tip-overs, protect operators from falling debris, and ensure controlled stops with heavy loads.
ROPS (Roll-Over Protective Structure) cabins withstand 3x the forklift’s weight in impacts. Pro Tip: Install rear-view cameras—blind spots expand with taller loads. For instance, a 40,000 lb steel coil blocks 90% of the operator’s forward view. How do manufacturers combat this? Linde’s heavy-duty series uses 360° radar detection. Practically speaking, combine these with daily pre-op checklists focusing on brake fluid levels and tire integrity.
Feature | Standard Forklift | Heavy-Duty Forklift |
---|---|---|
Braking Distance | 10 ft at 10 mph | 18 ft at 10 mph |
Cab Protection | Basic canopy | FOPS-certified cabin |
How often should heavy-duty forklifts be maintained?
Service intervals should occur every 250 hours or quarterly, whichever comes first. Hydraulic systems and mast rollers require lubrication every 50 hours under heavy use.
High-pressure hydraulic lines (up to 3,000 psi) demand leak checks—failure here causes abrupt load drops. Pro Tip: Use synthetic oils in extreme temperatures; they resist viscosity breakdown better than mineral oils. Imagine neglecting a 30,000 lb forklift’s axle bearings—it’s like ignoring wheel bearings on a freight train. Transitioning from light to heavy maintenance? Double the frequency of filter replacements compared to standard models.
Can heavy-duty forklifts be electrified?
Yes, modern lithium-ion batteries now power heavy-duty forklifts, offering 8–10-hour runtimes. Redway Battery’s 80V 600Ah LiFePO4 packs enable fast charging (<2 hrs) without voltage sag.
Electric models like the Cat EP20-25KT handle 25,000 lbs silently, ideal for food processing plants. Pro Tip: Opt for battery thermal management systems—overheating reduces lifespan by 40% in high-amperage draws. Why go electric? Lower lifetime costs—$8k in annual fuel savings vs diesel. But what about torque? AC motors deliver instant peak torque, critical for lifting inertia-laden loads.
Understanding Forklift Battery State of Charge: A Complete Guide
Redway Battery Expert Insight
FAQs
15–20 years with proper maintenance—twice as long as standard models due to overbuilt components.
Can they operate on rough terrain?
Yes, models with 4WD and oscillating axles handle mud, gravel, and slopes up to 25% grade.
Are attachments interchangeable with standard forklifts?
No—heavy-duty attachments require Class IV mounting systems and higher hydraulic flow rates (20–30 GPM).
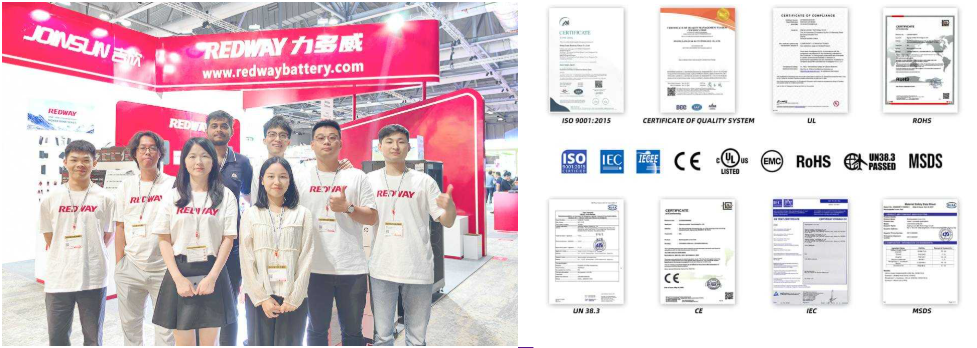