A forklift truck tracker solution combines GPS, IoT sensors, and telematics software to monitor forklift location, usage, and operational health in real time. These systems enhance safety, reduce downtime, and optimize workflow by providing data on speed, battery status, and maintenance needs. Advanced models integrate with warehouse management systems (WMS) for automated task routing and collision avoidance.
How to Access the Battery on a Toyota Forklift: A Complete Guide
What are the core components of a forklift tracker?
Forklift trackers rely on GPS modules, accelerometers, and cellular connectivity to transmit data. Sensor arrays monitor metrics like tilt angles and hydraulic load, while cloud platforms analyze patterns to predict maintenance. Pro Tip: Opt for trackers with IP67 ratings to withstand industrial dust/moisture.
Wholesale lithium golf cart batteries with 10-year life? Check here.
Beyond basic location tracking, modern systems use MEMS accelerometers detecting ±8g forces to flag reckless driving. For example, a sudden lateral G-force spike might indicate a near-tip event. When paired with load sensors, trackers can alert managers if forks exceed rated capacity by 10%. Technically, most solutions operate on 12–24V DC, drawing ≤0.5A to avoid draining forklift batteries. A 2×3 table below compares tracking technologies:
Technology | Range | Accuracy |
---|---|---|
GPS | Global | 3–5m |
RFID | 50m | 1m |
Bluetooth | 30m | 5m |
Pro Tip: Combine RFID for indoor tracking with GPS for yard management.
Want OEM lithium forklift batteries at wholesale prices? Check here.
How does tracking improve forklift safety?
Real-time monitoring reduces accidents via speed alerts, geo-fencing, and operator ID verification. Systems automatically enforce zone-specific speed limits (e.g., 5 mph near loading docks) and disable unauthorized use.
Practically speaking, when a forklift approaches a geo-fenced pedestrian area, the tracker can trigger audible alarms and restrict acceleration. Advanced solutions even integrate with LED floor lights to project warning signs. Take Amazon warehouses: their trackers reduced side-impact collisions by 72% by correlating turn rates with load heights. How? By calculating center-of-gravity shifts in real time using IMU data. Technically, safety systems require ≤100ms latency—achievable only via edge computing processors onboard the tracker.
What wireless technologies do trackers use?
Most systems utilize 4G LTE, LoRaWAN, or Wi-Fi 6, balancing coverage and data throughput. LTE offers real-time updates but consumes 3x more power than LoRa’s low-bandwidth signals.
In dense warehouses with metal shelving, signal attenuation can hit 20dB—why some trackers use mesh networks. For example, Toyota’s tracker relays data through nearby forklifts to overcome dead zones. Pro Tip: Deploy LTE-M (LTE for Machines) modules where cellular coverage is spotty; they maintain connectivity at -130dBm vs. standard LTE’s -100dBm cutoff. A 2×3 table clarifies tradeoffs:
Tech | Range | Battery Impact |
---|---|---|
4G LTE | Unlimited | High |
LoRaWAN | 5km | Low |
BLE 5.2 | 200m | Medium |
Redway Battery Expert Insight
FAQs
Quality trackers use ≤15Wh/day—under 1.5% of a 48V/200Ah battery’s capacity. Solar-powered options eliminate draw entirely.
Can trackers be retrofitted to older forklifts?
Yes, via OBD-II ports or direct-wired kits. However, pre-2010 models may lack CAN-BUS, limiting data granularity.
Forklift Battery Charging Station: A Comprehensive Guide
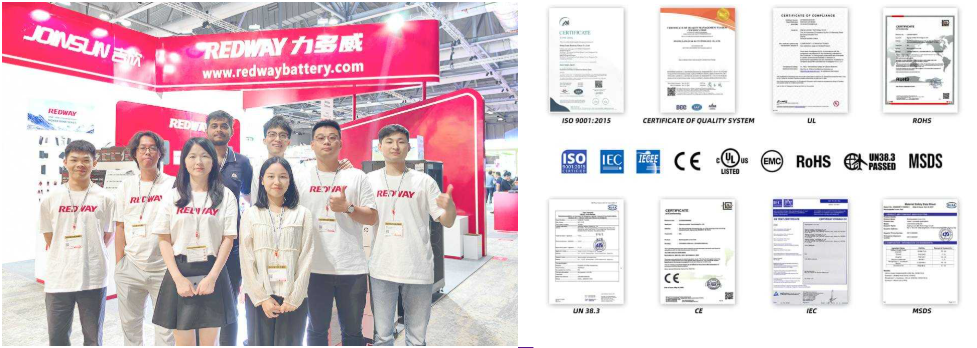