800V battery adoption in forklifts remains highly unlikely in the foreseeable future due to technical constraints and market demands. Current mainstream forklift batteries use 24V-80V systems optimized for low-speed torque and energy efficiency. While 800V architectures are emerging in electric passenger vehicles for fast charging, forklifts operate on different performance metrics where ultra-high voltage provides no meaningful advantage while escalating costs and safety risks.
What Is Standard Forklift Fork Spacing?
How Do Existing Forklift Voltage Ranges Compare to 800V?
Forklift battery systems typically span 24V-80V, with 80V already reserved for heavy-duty models. For context, industrial 80V 600Ah lead-acid battery packs deliver 48kWh capacity—sufficient for 8–10 hours of intensive operation. 800V architectures would require 10x voltage scaling without proportional operational benefits. Torque requirements at low RPMs make high-current 80V systems more practical than high-voltage/low-current alternatives.
Wholesale lithium golf cart batteries with 10-year life? Check here.
Transitioning to 800V would mandate complete redesigns of motors, controllers, and charging infrastructure. Consider the physics: a 10-ton forklift needing 20kW continuous power at 80V draws 250A, manageable with copper busbars. At 800V, current drops to 25A—seemingly advantageous until realizing that DC-DC converters and insulation systems for 1000V+ systems cost 3–5x more than legacy 80V solutions. Pro Tip: Battery compartment dimensions in most forklifts can’t accommodate 800V pack configurations without compromising counterweight balance.
What Technical Barriers Prevent 800V Adoption?
Component availability poses the first roadblock. Forklift-specific 800V motors don’t exist commercially—OEMs would need custom IPM (Interior Permanent Magnet) designs costing $15k–$25k per unit versus $3k–$5k for standard 48V motors. Charging infrastructure presents another hurdle: warehouse 480V AC systems can’t directly support 800V DC fast charging without expensive transformer upgrades.
Want OEM lithium forklift batteries at wholesale prices? Check here.
Battery chemistry further complicates adoption. While automotive 800V packs use NMC/NCA cells, forklifts still predominantly rely on lead-acid/LFP chemistries for their deep-cycle durability. Scaling these to 800V would require 230+ cells in series versus 24–40 cells in current configurations, drastically increasing failure points. Imagine maintaining cell balance across 230 lead plates—the equalization challenges would cripple operational uptime.
Parameter | 80V Forklift System | 800V Automotive System |
---|---|---|
Cell Count | 40 (Lead-Acid) | 192-216 (NMC) |
Typical Cycle Life | 1,500 cycles | 2,000 cycles |
Charge Time | 8-10 hours | 15-30 minutes |
Are There Any Emerging Use Cases?
Autonomous forklifts in megawarehouses theoretically could benefit from 800V’s faster charging during operational pauses. However, current autonomous models like Toyota’s Traigo 80V system already achieve 95% uptime with opportunity charging—eliminating the business case for ultra-rapid charging.
High-voltage experiments exist at the fringes: KION Group tested 144V lithium packs for faster warehouse logistics, but even this 2x voltage jump required complete vehicle redesigns. Until warehouse power grids evolve beyond 600V AC standards, 800V remains electrodynamically mismatched with infrastructure realities.
How Does Cost Compare to Existing Systems?
An 80V 600Ah LFP forklift battery costs ~$12k with 10-year lifespan. An equivalent 800V 75Ah pack—while physically smaller—would demand premium BMS and safety systems, escalating costs to ~$45k. For fleets of 50 forklifts, this represents a $1.65M premium with zero ROI in typical 2-shift operations.
Cost Factor | 80V System | Hypothetical 800V |
---|---|---|
Battery Pack | $12,000 | $45,000 |
Charger | $3,000 | $18,000 |
5-Year Maintenance | $2,500 | $12,000 |
Redway Battery Expert Insight
FAQs
Unlikely—rough terrain forklifts need high current for hill climbs, which 800V’s lower current design exacerbates. Component waterproofing costs would triple versus standard 80V IP67 systems.
Are any manufacturers prototyping 800V forklifts?
No major OEMs have public prototypes. Hyster’s 2025 roadmap shows commitment to 80V lithium with DC-DC converters for auxiliaries, not voltage escalation.
Forklift Battery Charging Station: A Comprehensive Guide
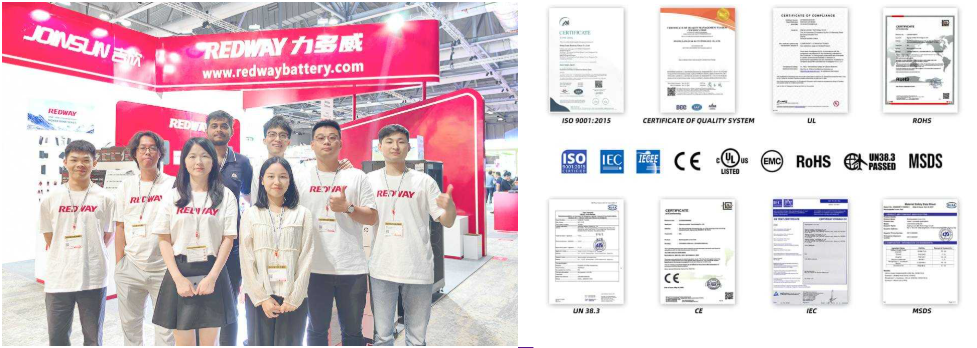