Specialized warehouse forklifts are material handling machines engineered for narrow aisles, high stacking, and automated workflows. Common variants include reach trucks, order pickers, and automated guided vehicles (AGVs), designed to optimize storage density and operational efficiency in constrained spaces. Lithium-ion or lead-acid batteries power most models, with runtime tailored to multi-shift logistics hubs. Key upgrades include articulated steering and wireless telemetry for real-time load tracking.
How Much Do Different Forklift Batteries Weigh by Type?
What types of forklifts are used in narrow-aisle warehouses?
Narrow-aisle forklifts prioritize compact dimensions (≤1.5m width) and 12m+ lift heights. Key models include turret trucks with rotating carriages and articulated counterbalances that pivot loads sideways. Pro Tip: Deploy laser guidance systems to reduce pallet damage in aisles under 2m wide.
Wholesale lithium golf cart batteries with 10-year life? Check here.
Turret trucks dominate ultra-narrow spaces (1.2–1.8m aisles) with their ability to rotate 180° without moving the chassis. For example, a Crown RR 5700 turret truck lifts 1,200 kg to 13m using a triple-stage mast while maintaining 1.6m aisle clearance. However, their top speed is often limited to 8 km/h for safety. Automated versions like the Hyster Fortens AGV integrate LiDAR obstacle detection, allowing 24/7 operation. Transitioning from standard forklifts? Expect 30–50% higher storage density but stricter operator training—articulated steering feels counterintuitive initially.
Type | Aisle Width | Max Height |
---|---|---|
Turret Truck | 1.2–1.8m | 14m |
Reach Truck | 2–2.5m | 11m |
AGV | 1.5–2m | 9m |
How do automated warehouse forklifts improve efficiency?
Automated forklifts (AGVs/AMRs) use SLAM navigation and IoT integration to cut labor costs by 45%. They optimize routes using WMS data, reducing unloaded travel by 60% versus manual operation.
Want OEM lithium forklift batteries at wholesale prices? Check here.
AGVs like Toyota’s Traigo 48V system follow magnetic tapes or predefined LiDAR maps, achieving 99.5% uptime with opportunity charging. A real-world example: DHL’s Rotterdam hub deployed 30 Jungheinrich EKS 215a AGVs, slashing order processing from 45 to 12 minutes. Pro Tip: Retrofit older fleets with telematics kits (e.g., Cat Lift Trucks’ VisionLink) to enable semi-automated pallet tracking. But what about mixed environments? AMRs (Autonomous Mobile Robots) dynamically reroute around obstacles using 3D cameras—ideal for warehouses sharing space with manual equipment.
What safety features do specialized forklifts have?
Specialized safety systems include load-sensing tilt prevention, blue safety lasers, and speed governors. Order pickers add harness anchors for operators working at 10m+ heights.
Modern reach trucks like the Hyster A1.6XNT automatically reduce speed when lifts exceed 6m. The BlueSpot® system projects a visible zone around the truck, warning pedestrians—critical in busy picking areas. For example, Amazon’s fleet uses Raymond 7500-Series trucks with “Slow Down” sensors that trigger when humans approach within 2m. Transitioning to automated models? Their 360° collision avoidance is 98% effective, but manual override protocols remain essential during sensor failures.
Which energy source is best for warehouse forklifts?
Lithium-ion batteries dominate modern fleets with 2–3 hour charge times vs 8h for lead-acid. But lead-acid remains cost-effective for single-shift operations needing <3 daily cycles.
Lithium’s 2,000–5,000 cycle lifespan suits high-throughput 24/7 warehouses. The Hyster Fortens AGV uses a 80V/600Ah LiFePO4 pack delivering 20h runtime with 30-minute fast charging. For colder environments (-20°C), NiCd batteries still prevail despite lower efficiency. Here’s a comparison:
Type | Cycle Life | Charge Time |
---|---|---|
Li-ion | 2,500 | 2h |
Lead-Acid | 1,500 | 8h |
NiCd | 1,800 | 6h |
How to choose between reach trucks and order pickers?
Reach trucks excel in pallet transport up to 12m, while order pickers prioritize operator platforms for case-level picking at heights. Throughput decides: reach trucks move 30+ pallets/hour vs 15–20 for pickers.
Consider SKU size—Crown’s SC 6000 Series reach trucks handle double-deep pallets in 2.3m aisles, whereas a Raymond 1100-Series order picker allows workers to directly access boxes on 9m racks. Transitioning from manual to automated picking? The average ROI is 18 months for warehouses processing 10,000+ daily items. But remember: order pickers require fall protection investments, adding $2,000–$5,000 per unit.
Redway Battery Expert Insight
FAQs
No—standard units need 3m+ aisles vs 1.5m for turret trucks. Forced use risks 80% higher damage rates.
Are automated forklifts worth the cost?
Yes for facilities with 20,000+ daily movements—AGVs cut labor by 60% with 2-year ROI via 24/7 operation.
How often should warehouse forklifts be serviced?
Li-ion models: bi-annual checks. Lead-acid: quarterly watering. AGVs need monthly sensor calibration and software updates.
Forklift Battery Charging Station: A Comprehensive Guide
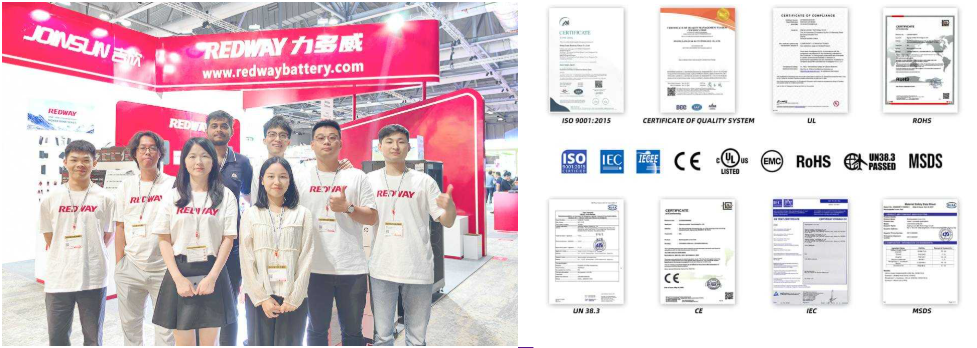