Lift truck lithium-ion power sources are rechargeable battery systems using lithium-ion cells (like LiFePO4 or NMC) to deliver 24–80V energy for material handling equipment. They offer 2-3x higher energy density than lead-acid, zero maintenance, and fast charging (1-3 hours). Optimized for Class I-III forklifts, these batteries integrate BMS thermal controls to prevent overheating during intensive lifting cycles. Most operate via CAN-Bus protocols for real-time fleet monitoring.
What Is Standard Forklift Fork Spacing?
What chemistry types power lift truck Li-ion batteries?
Three primary lithium chemistries dominate: LiFePO4 (safety-focused), NMC (energy-dense), and LTO (ultra-fast charging). LiFePO4 prevails in warehouses due to thermal stability under 150°C, while NMC suits high-throughput operations needing compact energy storage. LTO’s titanium oxide anodes support 10,000+ cycles but cost 2x more. Pro Tip: Always verify cell chemistry against your operation’s charge/discharge rates—using LTO for single-shift work wastes ROI.
Wholesale lithium golf cart batteries with 10-year life? Check here.
How do Li-ion advantages surpass lead-acid in forklifts?
Lithium batteries eliminate acid spills, equalization charging, and water top-ups required by lead-acid. They maintain >95% capacity over 2,000 cycles vs. lead-acid’s 500-800 cycles. Opportunity charging during breaks extends runtime without memory effect. For example, a 48V 300Ah LiFePO4 pack provides 14.4kWh—equivalent to 3 lead-acid packs—but weighs 40% less. Pro Tip: Deploy Li-ion in multi-shift operations; their 85% DoD maximizes throughput versus lead-acid’s 50% limit.
Feature | Li-ion | Lead-Acid |
---|---|---|
Cycle Life | 2,000–5,000 | 500–1,200 |
Energy Density | 150–250 Wh/kg | 30–50 Wh/kg |
Charge Time | 1–3 hours | 8–12 hours |
Can any forklift integrate Li-ion power sources?
Not universally—retrofitting requires voltage compatibility and BMS communication with the truck’s controller. Modern electric forklifts (2015+) often support CAN-Bus integration, while older models may need voltage converters. For instance, replacing a 36V lead-acid system with Li-ion demands a DC-DC converter if the truck’s motor can’t handle lithium’s steeper discharge curve. Warning: ⚠️ Never bypass factory voltage limits—overvoltage can fry motor windings.
Want OEM lithium forklift batteries at wholesale prices? Check here.
What maintenance safeguards Li-ion forklift batteries?
Lithium systems need monthly SOC checks and terminal cleaning but avoid lead-acid’s watering rituals. BMS self-monitoring tracks cell balance—imbalances over 50mV trigger alerts. Storing at 30–60% SOC in 15–25°C environments prevents calendar aging. Practically speaking, a warehouse using 20 Li-ion packs might save 200 labor hours/year versus lead-acid upkeep. Pro Tip: Use dielectric grease on terminals quarterly to resist corrosion from pallet jack washdowns.
How Much Does a Forklift Battery Weigh?
Are Li-ion costs justified for small-scale operations?
Upfront costs run 2-3x lead-acid ($8k–$15k vs. $3k–$6k), but TCO breakeven occurs at ~800 cycles. Operations with <1 shift/day or seasonal demand may not recoup savings. However, lithium’s resale value (30–50% after 5 years) vs. lead-acid’s scrap value (10%) changes the math. For example, a 48V 600Ah Li-ion battery saving $3,200/year in labor/energy pays back in 3 years.
Cost Factor | Li-ion | Lead-Acid |
---|---|---|
Initial Price | $12,000 | $5,000 |
5-Year TCO | $15,000 | $22,000 |
Residual Value | $4,000 | $500 |
How are industries adopting Li-ion for material handling?
E-commerce giants like Amazon and Walmart deploy Li-ion fleets for 24/7 operation scalability. Automotive plants favor their rapid charging during 45-minute production breaks. Cold storage facilities benefit from lithium’s -20°C performance—lead-acid loses 50% capacity at 0°C. But what about smaller warehouses? Those with 5+ daily shifts gain most, while low-utilization sites should analyze payback periods. Transition Tip: Phase in lithium—replace 20% of lead-acid units annually to spread capital outlay.
Redway Battery Expert Insight
FAQs
Advanced BMS with thermostatic cutoffs prevent overheating—our packs maintain <40°C even at 2C rates. Always use Li-ion-certified chargers; generic units lack temperature compensation.
Can I leave a Li-ion forklift battery charging overnight?
Yes—once fully charged, the BMS disconnects input. However, avoid continuous 100% SOC storage; programmable chargers can limit to 80% for overnight phases.
Is retrofitting Li-ion into diesel forklifts feasible?
No—diesel engines lack electric drivetrains. Li-ion only replaces existing electric power sources.
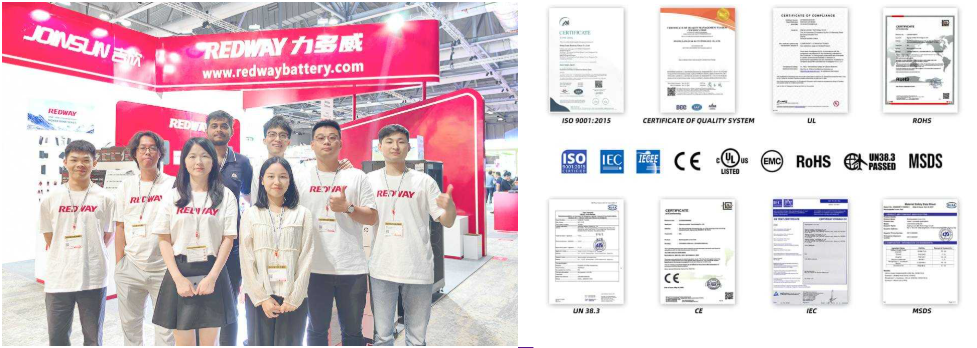