Industrial vehicles and forklift batteries are specialized power systems designed for heavy-duty applications like material handling. Forklift batteries typically use lead-acid or lithium-ion chemistries, offering 24V–80V voltages and capacities from 200Ah to 1200Ah. Built for deep cycling and high torque, they power forklifts, pallet jacks, and airport tow tractors. Lithium variants like LiFePO4 now dominate modern fleets due to 3x lifespan and 50% faster charging versus lead-acid.
Forklift Battery Charging Station: A Comprehensive Guide
What defines industrial vehicle batteries?
Industrial vehicle batteries prioritize high discharge rates and deep-cycle resilience for equipment operating 8–24 hours daily. Unlike automotive SLI batteries, forklift units endure 80% depth-of-discharge (DoD) cycles. Lithium models achieve 3,000–5,000 cycles vs. 1,500 for lead-acid. For example, a 48V 600Ah LiFePO4 battery can deliver 28.8kWh daily—enough for 6–8 hours of continuous forklift operation. Pro Tip: Monitor electrolyte levels in flooded lead-acid bi-weekly to prevent sulfation.
Wholesale lithium golf cart batteries with 10-year life? Check here.
How do forklift batteries differ from automotive ones?
Forklift batteries use thicker plates (6–7mm vs. 2mm automotive) for sustained high-current output. They’re rated for deep discharges (80% DoD) versus automotive’s 20% limit. Lithium forklift batteries also integrate robust thermal management, handling -20°C to 60°C. A Tesla car battery prioritizes energy density (260 Wh/kg), while a forklift’s LiFePO4 focuses on power density (150–200 Wh/kg) and cycle life. Moreover, forklift chargers use 3-stage protocols to prevent stratification in lead-acid units.
Parameter | Forklift Battery | Automotive Battery |
---|---|---|
Plate Thickness | 6–7mm | 1.5–2mm |
Typical Cycles | 1,500+ | 200–300 |
DoD Tolerance | 80% | 20% |
Why choose lithium over lead-acid for forklifts?
Lithium forklift batteries offer zero maintenance, 30–50% faster charging, and 2–3x longer lifespan. They eliminate acid spills and hydrogen venting, enhancing warehouse safety. A 48V 600Ah lithium pack weighs 700kg vs. 1,200kg for lead-acid—reducing vehicle wear. Upfront costs are 2x higher, but 8-year TCO is 40% lower. For example, Walmart slashed energy costs by 60% after switching 9,000 forklifts to lithium. Practically speaking, opportunity charging during breaks extends uptime without memory effects.
Want OEM lithium forklift batteries at wholesale prices? Check here.
Factor | LiFePO4 | Lead-Acid |
---|---|---|
Cycle Life | 3,000–5,000 | 1,000–1,500 |
Energy Efficiency | 95% | 70–80% |
Charge Time | 1–2h | 8–10h |
What safety protocols govern forklift batteries?
OSHA mandates spill containment pallets for lead-acid and UL 2580 certification for lithium models. Charging areas require ventilation (20 ACH) to disperse hydrogen gas. Thermal runaway prevention is critical—lithium BMS must monitor cell voltages within ±20mV. Pro Tip: Use IR thermometers weekly to check terminal temps; rises over 50°C signal connection issues. Remember the 2019 Amazon warehouse fire? Faulty battery handling caused $8M in damages—never bypass safety interlocks.
How Much Do Different Forklift Batteries Weigh by Type?
Redway Battery Expert Insight
FAQs
Yes, Redway’s heated lithium packs work at -30°C, unlike lead-acid which loses 50% capacity below 0°C. Always confirm low-temp specs before purchase.
How often should forklift batteries be replaced?
Lead-acid lasts 3–5 years; lithium 8–12 years. Replace when capacity hits 60%—checked via annual discharge testing.
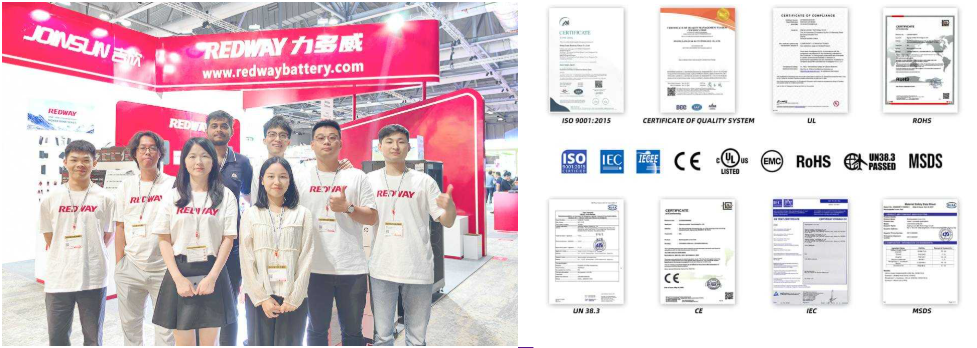