Forklift lithium batteries, chargers, and accessories form integrated power systems designed for modern electric material handling. LiFePO4-based batteries (48V–80V) offer 2–3x longer lifespan than lead-acid, paired with intelligent chargers enabling 1–2 hour fast charging. Key accessories include battery management systems (BMS), forklift trays, and cooling modules, ensuring safe, high-throughput operations in logistics and warehouses.
Forklift Battery Charging Station: A Comprehensive Guide
What constitutes forklift lithium battery systems?
Forklift lithium systems combine LiFePO4/NMC cells, modular designs (48V–80V), and built-in BMS for thermal/voltage regulation. They support rapid 1C–3C charging, unlike lead-acid’s 0.2C limit, with energy densities exceeding 120 Wh/kg for 8–12 hour shifts.
Wholesale lithium golf cart batteries with 10-year life? Check here.
Technically, a 48V 600Ah LiFePO4 battery delivers 28.8 kWh—enough to power a 3-ton forklift for 6–8 hours. Pro Tip: Always match charger output (e.g., 48V 100A) to battery specs—overcurrent charging degrades anode stability. For instance, Amazon warehouses use 80V lithium packs with regenerative braking, cutting downtime by 40%.
Want OEM lithium forklift batteries at wholesale prices? Check here.
How do lithium chargers differ from lead-acid models?
Lithium chargers use adaptive CC-CV algorithms and CAN bus communication with BMS, unlike lead-acid’s fixed voltage. They achieve 95% efficiency versus 75–80% for traditional chargers, with 1–3 hour charge cycles.
Advanced models like the Redway RXL series apply pulsed current to minimize heat during 2C charging. A 48V lithium charger typically operates at 54.6V (LiFePO4) with ±0.5% voltage accuracy. Pro Tip: Use temperature-compensated charging in cold warehouses—LiFePO4 requires ≥5°C for optimal ion mobility. For example, Walmart’s DC fast chargers replenish 80% capacity in 50 minutes, versus 8 hours for flooded lead-acid.
Charger Type | Charge Time | Efficiency |
---|---|---|
Lithium (30A) | 2 hours | 95% |
Lead-Acid (30A) | 8 hours | 78% |
What accessories optimize lithium forklift performance?
Critical accessories include BMS monitors, fire-resistant trays, and active cooling ducts. Battery trays with shock absorption (<5G vibration resistance) prevent cell misalignment during heavy lifting.
Parker Hannifin’s conductive cooling plates maintain cells at 25–35°C, extending cycle life by 30%. Telemetry add-ons like Forsee Power’s Cloud BMS track SoH in real-time—vital for fleet management. Pro Tip: Install anti-spark connectors when replacing lead-acid batteries—lithium’s lower internal resistance can cause arcing.
Accessory | Function | Benefit |
---|---|---|
BMS | Cell balancing | Prevents overcharge |
Cooling ducts | Thermal regulation | +50% cycle life |
Understanding Forklift Battery State of Charge: A Complete Guide
What safety standards govern lithium forklift systems?
Compliance with UL 2580, UN 38.3, and IEC 62619 is mandatory. UL tests include crush resistance (150% rated load) and thermal runaway containment (≤800°C external temps).
For instance, BYD’s lithium packs use ceramic separators and pressure relief vents to meet UL’s 1-hour fire containment rule. Pro Tip: Conduct quarterly insulation resistance tests (>100MΩ at 500VDC)—moisture ingress below IP65 ratings risks short circuits.
Redway Battery Expert Insight
FAQs
Only with compatible voltage/BMS—lithium’s 80% DoD vs. lead-acid’s 50% requires charger recalibration. Retrofit kits often include voltage converters.
How often should lithium forklift batteries be serviced?
Annual inspections suffice—check terminal torque (8–12 Nm) and BMS logs. No watering or equalization needed.
Are lithium forklift chargers compatible with all brands?
No—confirm protocol alignment (e.g., CAN vs. RS485). Mismatched chargers may fail to handshake with BMS, halting charging.
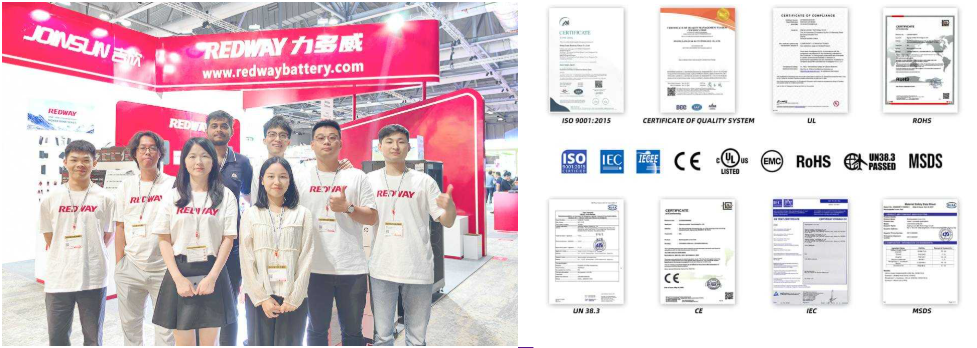