Forklift clamps are specialized attachments replacing standard forks to handle non-palletized materials like drums, bales, or rolls. They use hydraulic pressure to grip loads laterally, ideal for industries like recycling, textiles, or paper manufacturing. Available in drum, paper roll, or carton clamp variants, they improve efficiency by securing irregular loads without pallets. Proper clamp selection depends on load dimensions, weight, and surface friction.
How Much Does a Forklift Battery Weigh?
What are the primary types of forklift clamps?
Drum clamps, paper roll clamps, and carton clamps dominate the market. Drum clamps secure cylindrical loads (e.g., oil barrels), while paper roll clamps vertically lift 500–2,500 kg rolls. Carton clamps use rubber-faced arms for fragile boxes. Each type requires precise hydraulic pressure (150–250 bar) and load-width adjustments.
Wholesale lithium golf cart batteries with 10-year life? Check here.
Forklift clamps vary by design and application. Drum clamps typically feature curved arms with rubber padding to prevent slippage under 20–1,000 kg loads. Paper roll clamps often include V-shaped saddles and rotating arms to handle rolls up to 1.5m in diameter. Carton clamps apply 1–5 psi pressure via adjustable arms to avoid crushing. Beyond basic functionality, industries prioritize clamp opening widths—e.g., recycling facilities need 1.2m widths for bales. Pro Tip: Always verify the clamp’s load center rating—using a 500kg clamp for 600kg paper rolls risks hydraulic failure. For example, a Crown BX50 drum clamp lifts 800kg at 1,100mm load center, but exceeding this strains the forklift’s mast bearings.
Clamp Type | Max Capacity | Typical Use Case |
---|---|---|
Drum | 1,000 kg | Chemical barrels |
Paper Roll | 2,500 kg | Printing paper rolls |
Carton | 1,800 kg | Retail inventory |
How do hydraulic clamps differ from mechanical models?
Hydraulic clamps use the forklift’s hydraulic system for pressure (100–300 bar), enabling precise grip adjustments. Mechanical clamps rely on levers/springs, limiting control but offering lower cost. Hydraulic models dominate heavy industries due to automated operation and safety valves preventing sudden releases.
Want OEM lithium forklift batteries at wholesale prices? Check here.
Hydraulic clamps integrate with the forklift’s hydraulic network via hoses and control valves, delivering 200–400 N/cm² grip force. They’re programmable for load sensitivity—critical for fragile glass panes or uneven concrete tubes. Mechanical clamps, while cheaper, require manual adjustments and lack pressure feedback. But what happens if hydraulic pressure drops mid-operation? Safety check valves lock the clamps, preventing accidental drops. For instance, a Toyota 8FGCH25 with hydraulic clamps maintains 220 bar pressure for 1,500 kg rolls, whereas mechanical models need manual tightening every 10–15 lifts. Pro Tip: Inspect hydraulic hoses monthly for wear—pin-sized leaks can reduce grip force by 40%.
What safety protocols apply to clamp operations?
OSHA mandates load stability checks, clamp pressure calibrations, and operator certifications. Loads must stay within 85% of clamp capacity, with centering ±5cm deviation. Weekly inspections of hoses, arms, and pressure gauges are compulsory to prevent material-handling incidents.
Forklift clamp safety starts with load alignment. A 10cm off-center load increases mast torsion by 30%, risking tip-overs. Operators must test grip strength at 10% pressure before full engagement—uneven surfaces like dented drums require 20–30% higher pressure. Training should cover emergency release protocols: hydraulic clamps need auxiliary shutoff valves, while mechanical versions require manual disengagement. Consider a warehouse handling lubricant drums: over-clamping at 300 bar could deform steel lids, but 220 bar maintains integrity. Pro Tip: Use fluorescent markers on clamp arms to visualize wear—replace arms if cracks exceed 2mm depth.
Can clamps handle mixed load types simultaneously?
Most clamps are single-purpose, but multi-function clamps with interchangeable pads or arms exist. These hybrid models handle drums, bales, or boxes by switching attachments. However, capacity drops 15–20% vs. dedicated clamps, and setup takes 15–30 minutes per shift.
Universal clamps like the Cascade UCL-20 feature modular faces—polyurethane for boxes, serrated steel for bales. However, their pivot mechanisms add 50–80kg, reducing the forklift’s net capacity. Hydraulic lines may need reconfiguration when swapping attachments, increasing downtime. For mixed loads, dual-clamp forklifts (separate arms for boxes and rolls) offer better efficiency but cost 2–3x more. A beverage distributor might use combo clamps for morning pallet handling and afternoon barrel lifts, sacrificing 200kg capacity for versatility.
Clamp Type | Versatility | Capacity Loss |
---|---|---|
Dedicated | Low | 0% |
Multi-Function | High | 18% |
How do clamps impact forklift stability?
Clamps extend the load center, reducing lifting capacity by 10–25%. A 48” paper roll clamp shifts the center 15–20cm forward vs. standard forks. Operators must de-rate the forklift’s capacity using load charts and avoid lifting near max height to prevent instability.
Every clamp alters the forklift’s balance point. For example, a 1,000kg capacity forklift with standard forks might only lift 750kg with clamps at full height. The load center distance—critical in stability calculations—increases from 24” to 30” with clamps. Practically speaking, lifting a 800kg roll to 4m height requires 30% counterweight and sub-5 mph travel speed. A real-world example: Hyster H4.0FT with drum clamps loses 22% capacity at 3m lift height due to forward torque. Pro Tip: Use outriggers or stabilizer bars when handling top-heavy loads like vertical spools.
Redway Battery Expert Insight
FAQs
No—clamps require specific carriage mounts (Class II or III) and hydraulic flow rates (8–15 l/min). Consult OEM guidelines before purchasing.
Can clamps lift heavier loads than standard forks?
Rarely—clamps reduce capacity by 10–25% due to extended load centers. Prioritize grip precision over weight limits.
How to Access the Battery on a Toyota Forklift: A Complete Guide
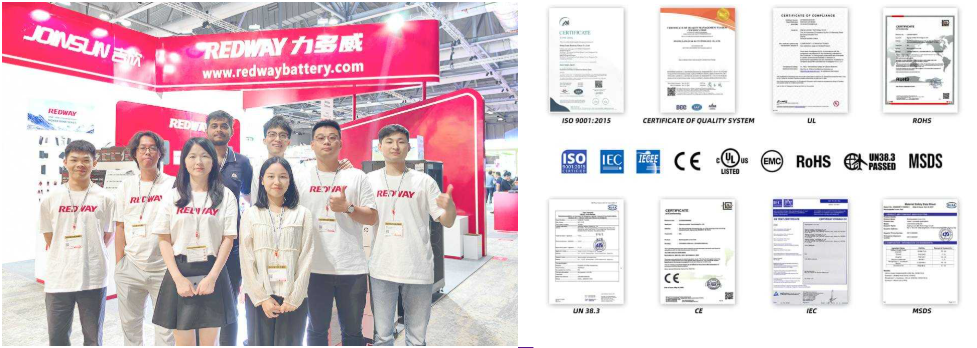