Lithium-ion (Li-ion) forklift batteries surpass lead-acid in lifespan (3,000–5,000 cycles vs. 1,500 cycles) and efficiency (95% vs. 70% energy use), with rapid charging and zero maintenance. However, lead-acid offers lower upfront costs. For high-intensity operations, Li-ion’s long-term ROI and fast partial charging make it superior, while lead-acid suits budget-conscious, low-use scenarios.
How Much Does a Forklift Battery Weigh?
What are the lifespan differences between lithium-ion and lead-acid batteries?
Lithium-ion batteries last 3–5x longer than lead-acid, enduring 3,000–5,000 cycles at 80% depth of discharge (DoD) versus 1,500 cycles at 50% DoD for lead-acid. Their cycle stability and minimal capacity degradation justify higher upfront costs for intensive operations.
Wholesale lithium golf cart batteries with 10-year life? Check here.
Practically speaking, Li-ion’s chemistry resists sulfation and corrosion—common lead-acid killers. A Li-ion pack operating 2 shifts daily can last 7–10 years, while lead-acid typically requires replacement every 3–4 years. Pro Tip: Avoid discharging lead-acid below 50% DoD—it halves cycle life. For example, a 600Ah lead-acid battery effectively offers 300Ah usable capacity, whereas Li-ion delivers 480Ah (80% of 600Ah) with less weight. Beyond longevity, consider total energy throughput: 600Ah Li-ion at 80% DoD provides 288,000Ah over 5,000 cycles, versus 90,000Ah for lead-acid.
Metric | Lithium-ion | Lead-acid |
---|---|---|
Cycle Life | 3,000–5,000 | 1,200–1,500 |
DoD Tolerance | 80–90% | 50% |
How do upfront costs compare to long-term savings?
Lithium-ion costs 2–3x more upfront ($12k vs. $5k for 600Ah), but slashes operational expenses by 30–60% through zero watering, faster charging, and no replacement costs for 8–10 years. High-throughput operations break even in 2–4 years.
Want OEM lithium forklift batteries at wholesale prices? Check here.
But what’s the real financial impact? Lead-acid requires $1,200/year in maintenance (watering, equalization), while Li-ion eliminates these. Add forklift downtime: 8-hour lead-acid charging versus 1–2 hours for Li-ion. For a warehouse running 3 shifts, that’s 6 extra hours daily. Example: A 10-forklift fleet saves 21,900 hours/year with Li-ion—equivalent to $328,500 in labor at $15/hour. Pro Tip: Use NPV calculations factoring energy efficiency (Li-ion uses 15–30% less kWh/cycle). Warning: Cheap Li-ion BMS can fail—opt for UL-certified packs with thermal safeguards.
What maintenance is required for each battery type?
Lead-acid demands weekly watering, terminal cleaning, and monthly equalization charges, consuming 15–30 mins/battery weekly. Li-ion needs zero maintenance—no fluid checks or equalization—since Battery Management Systems (BMS) auto-balance cells and prevent overcharging.
Why does lead-acid require such tedious upkeep? Sulfation occurs when batteries sit discharged, forming crystals that reduce capacity. Equalization dissolves these but shortens lifespan. Conversely, Li-ion’s sealed design prevents acid leaks and hydrogen emissions. A food warehouse using lead-acid must allocate dedicated watering stations, while Li-ion avoids spill risks. Pro Tip: Use deionized water for lead-acid—tap minerals cause corrosion. Transitional savings: Switching to Li-ion frees up 130–260 labor hours annually per battery.
How does energy efficiency impact operating costs?
Lithium-ion operates at 95% efficiency versus 70–85% for lead-acid, meaning 30% less energy waste per cycle. Fast charging also reduces kWh losses from prolonged absorption phases.
Forklift Battery Charging Station: A Comprehensive Guide
Imagine two 600Ah batteries: Li-ion delivers 570Ah net (95%), lead-acid 420Ah (70%). Over 5,000 cycles, Li-ion provides 2.85M Ah, lead-acid 630k Ah. But how does this translate to dollars? At $0.12/kWh, Li-ion consumes $11,232 versus $25,920 for lead-acid over 10 years. Pro Tip: Schedule lead-acid charging during off-peak hours to minimize demand charges. Table:
Metric | Lithium-ion | Lead-acid |
---|---|---|
kWh Lost per Cycle | 0.3 | 1.2 |
Annual Energy Cost (600Ah) | $864 | $3,456 |
What are the environmental impacts of each type?
Lithium-ion has a higher manufacturing footprint (60–100kg CO2/kWh) but offsets this via longevity and recyclability (95% materials recoverable). Lead-acid recycling rates hit 99%, but toxic lead and sulfuric acid pose handling risks.
While both are recyclable, Li-ion’s lower replacement frequency reduces mining impacts. A single Li-ion pack over 10 years equals 3 lead-acid packs—mining 300kg lead vs. 50kg lithium. However, irresponsible Li-ion disposal risks cobalt/nickel pollution. Pro Tip: Partner with certified recyclers—illegal dumping of lead-acid batteries incurs $10k+ fines. Transitional benefit: Li-ion’s weight (30% lighter) reduces forklift energy use, further cutting emissions.
Which battery suits high-intensity vs. low-use operations?
Lithium-ion excels in multi-shift operations needing rapid charging and 90%+ uptime. Lead-acid fits single-shift operations with budget constraints and scheduled downtimes for charging/maintenance.
For instance, a cold storage facility operating 24/7 benefits from Li-ion’s instant opportunity charging, whereas a small warehouse with 5-hour daily use can manage lead-acid’s 8-hour charge cycles. But what if demand fluctuates? Li-ion’s partial SOC flexibility avoids the memory effect plaguing lead-acid. Pro Tip: For mixed fleets, use Li-ion on high-utilization lifts and lead-acid on backups. Warning: Never mix battery types on same chargers—voltage mismatches cause fires.
Redway Battery Expert Insight
FAQs
Yes, Li-ion operates at -20°C to 60°C, but charging below 0°C requires heated cabinets. Lead-acid loses 50% capacity at -20°C.
Are lead-acid batteries safer than lithium-ion?
Lead-acid has lower fire risk but higher explosion risk from hydrogen off-gassing. Li-ion with proper BMS and venting is equally safe in industrial settings.
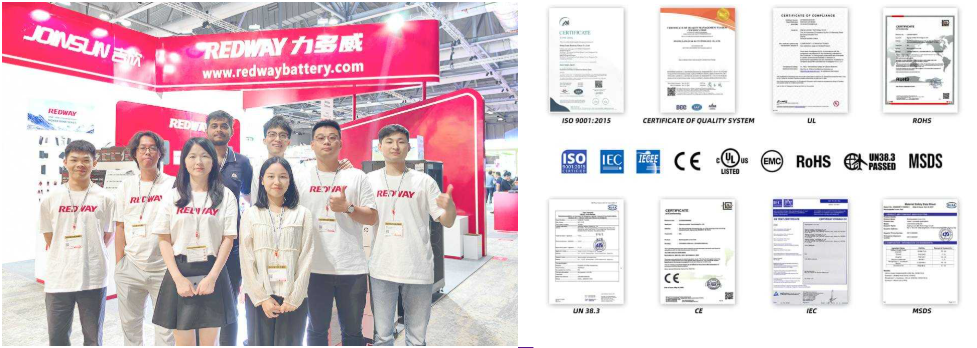