Hyster Robotics supports your workforce through advanced automation solutions like autonomous forklifts and robotic systems. These integrate AI-driven navigation and IoT sensors to optimize material handling, reduce manual labor, and enhance safety. For example, their Hyster® Automated Lift Trucks use LiDAR mapping for precise pallet handling. Pro Tip: Pair robotics with workforce training to maximize ROI and minimize downtime during integration.
How Much Does a Forklift Battery Weigh?
What core components power Hyster Robotics systems?
Hyster Robotics relies on LiDAR sensors, AI algorithms, and modular chassis designs for adaptability. These enable real-time obstacle detection and route optimization, even in dynamic warehouse environments.
Wholesale lithium golf cart batteries with 10-year life? Check here.
At the heart of Hyster’s systems are LiDAR sensors with 270-degree coverage and 0.1° angular resolution, providing centimeter-level accuracy. The AI stack processes data at ≤50ms latency, ensuring seamless coordination with human workers. Modular designs allow customization—like swapping grippers for drums or pallets. Pro Tip: Regularly calibrate LiDAR sensors to maintain positional accuracy, especially in high-dust environments. For example, a Hyster® ReachBot in a beverage warehouse autonomously navigates narrow aisles while avoiding sudden foot traffic. Beyond hardware, over-the-air updates ensure software stays current with industry standards.
How do Hyster Robotics enhance workforce safety?
These systems reduce injury risks via collision-avoidance algorithms and emergency braking, cutting incident rates by up to 70% in partnered facilities.
Want OEM lithium forklift batteries at wholesale prices? Check here.
Hyster’s robotics employ dual-layer safety: predictive AI analyzes movement patterns to preempt collisions, while hydraulic disc brakes activate within 0.3 seconds if thresholds are breached. Thermal cameras detect human presence up to 10m away, even in low light. Pro Tip: Combine robotics with wearable IoT tags for workers—this creates a geofenced safety mesh. Imagine a scenario where a robot slows its speed when a tagged employee enters a 2m zone. Practically speaking, facilities using Hyster systems report 40% fewer OSHA recordables annually. But what if a sensor fails? Redundant ultrasonic arrays provide backup detection, ensuring continuous operation.
Safety Feature | Specification | Human Equivalent |
---|---|---|
LiDAR Range | 15m | Peripheral Vision |
Braking Response | 0.3s | Human Reflex (0.5s) |
Can Hyster robots collaborate with human workers?
Yes, through adaptive speed control and shared task management interfaces, enabling hybrid workflows without bottlenecks.
Hyster’s collaboration mode uses weight sensors and path prediction to adjust robot speed dynamically. If a human is lifting heavy items nearby, the system reroutes to avoid congestion. The interactive dashboard lets workers assign tasks via voice commands or tablets—like redirecting a robot to prioritize urgent shipments. For example, a retail DC using Hyster® JoustBot reduced order-picking time by 25% by splitting tasks between bots and staff. Pro Tip: Use color-coded LED indicators on robots to communicate status—green for moving, red for halted. But how do you prevent workflow conflicts? Middleware like HysterSync® integrates robotics data with existing WMS platforms, ensuring real-time alignment.
What Is Standard Forklift Fork Spacing?
What industries benefit most from Hyster Robotics?
Manufacturing, logistics, and cold storage sectors gain significant ROI through 24/7 operation and temperature-resistant components.
In automotive plants, Hyster robots handle dies weighing up to 1.5 tons with ±2mm precision, eliminating manual crane operations. Cold storage bots operate at -30°C using heated battery compartments and lubricants rated for extreme temps. A seafood distributor increased throughput by 60% using Hyster® FreezeBot to stack pallets in blast freezers. Pro Tip: Opt for stainless steel chassis variants in corrosive environments. Beyond traditional sectors, e-commerce hubs use swarm logic to coordinate 50+ robots during peak sales. Could your facility benefit? If repetitive heavy lifting dominates workflows, automation likely offers a sub-2-year payback period.
Industry | Use Case | Performance Gain |
---|---|---|
Logistics | Pallet Sorting | 45% Faster |
Pharma | Vial Transport | 99.9% Accuracy |
Hyster Robotics Expert Insight
FAQs
Typically 6–10 weeks, depending on WMS compatibility. Full training and phased deployment minimize disruption to ongoing operations.
Do Hyster robots require specialized maintenance?
Yes, quarterly LiDAR calibration and annual brake inspections are recommended. Use Hyster’s FleetCare® service plans for predictive upkeep.
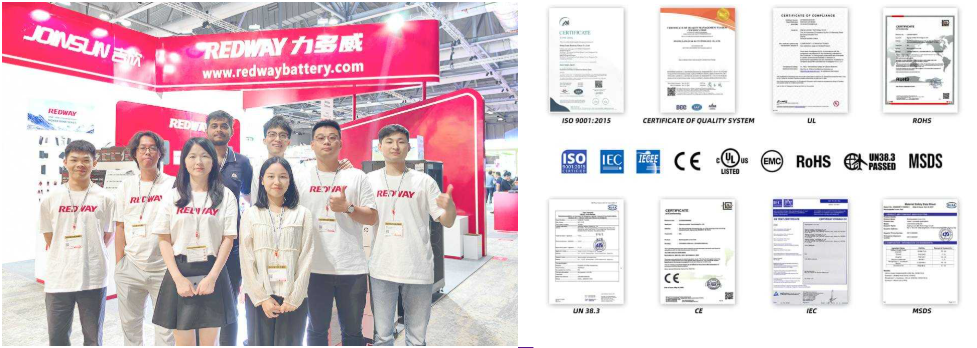