Forklift incidents commonly result from operator error, inadequate training, poor maintenance, environmental hazards, and overloaded cargo. Prevention requires comprehensive training programs, routine equipment inspections, clear workplace protocols, and adherence to safety regulations like OSHA standards. Implementing technology such as proximity sensors and fatigue monitoring systems further reduces risks.
What Are the Most Common Causes of Forklift Accidents?
The most frequent causes include tip-overs due to unbalanced loads, collisions with pedestrians or infrastructure, improper turning, lack of situational awareness, and mechanical failures. Overloading, speeding, and insufficient training exacerbate these risks, particularly in congested or poorly lit environments.
Wholesale lithium golf cart batteries with 10-year life? Check here.
How Does Operator Training Influence Forklift Safety?
Effective training reduces accident rates by 25–30%, according to OSHA. Programs should cover load management, hazard detection, emergency protocols, and equipment-specific operations. Refresher courses every three years—or after incidents—ensure skills remain current. Certified trainers emphasize hands-on practice in simulated workplace conditions.
Want OEM lithium forklift batteries at wholesale prices? Check here.
Advanced training methods, such as virtual reality (VR) simulations, are now being adopted to replicate high-risk scenarios without real-world consequences. For example, VR modules can train operators to navigate narrow aisles or react to sudden pedestrian movements. Additionally, mentorship programs pairing new operators with experienced colleagues have shown a 15% improvement in safety compliance. A study by the National Safety Council found that facilities implementing bi-annual skill assessments reduced load-handling errors by 42%. Training should also address psychosocial factors, such as stress management, since 18% of incidents occur during high-pressure tasks like meeting tight deadlines.
Training Component | Impact on Safety |
---|---|
VR Simulations | 27% Fewer Collisions |
Mentorship Programs | 15% Higher Compliance |
Stress Management | 18% Risk Reduction |
What Role Does Maintenance Play in Preventing Forklift Malfunctions?
Routine maintenance checks identify issues like hydraulic leaks, worn tires, brake failures, and battery degradation. Daily pre-operation inspections (e.g., testing horns, lights, and steering) are mandatory. Forklifts used in extreme temperatures or dusty environments require more frequent servicing to prevent overheating or component corrosion.
Predictive maintenance technologies, such as IoT-enabled diagnostic tools, are revolutionizing forklift upkeep. Sensors monitor vibration patterns and fluid levels, alerting technicians to potential failures before they occur. For instance, thermal imaging can detect overheating motors with 92% accuracy, allowing repairs during scheduled downtime. Companies using cloud-based maintenance logs report 35% fewer unexpected breakdowns. Seasonal adjustments are also critical—lubricants rated for sub-zero temperatures prevent hydraulic system failures in cold storage facilities, while dust filters in warehouses reduce engine wear by 50%.
Maintenance Task | Recommended Frequency |
---|---|
Hydraulic System Check | Weekly |
Battery Inspection | Daily |
Tire Pressure Review | Before Each Shift |
Why Are Workplace Design and Layout Critical to Forklift Safety?
Poorly designed aisles, inadequate signage, and cluttered pathways account for 22% of incidents. Optimized layouts feature clear pedestrian zones, mirrored blind-spot corners, and speed-limiting zones. Floor markings and anti-slip surfaces reduce collision risks, while proper lighting ensures visibility in loading docks and storage areas.
How Can Technology Mitigate Forklift Accident Risks?
IoT-enabled sensors detect proximity to obstacles and automatically reduce speed. Cameras provide 360-degree visibility, addressing blind spots. Telematics systems monitor operator behavior, flagging reckless driving patterns. Autonomous forklifts, though nascent, minimize human error in repetitive tasks but require infrastructure upgrades.
What Are the Legal Consequences of Non-Compliance with Forklift Regulations?
OSHA penalties for safety violations exceed $15,000 per incident, with repeat offenses costing up to $156,259. Companies face litigation costs, increased insurance premiums, and reputational damage following severe accidents. Compliance involves documenting training, maintaining inspection logs, and reporting near-misses within 24 hours.
How Does Fatigue Impact Forklift Operator Performance?
Fatigue slows reaction times by 40%, increasing collision risks during extended shifts. Employers should enforce mandatory break schedules, limit overtime, and use wearable tech to monitor alertness. Rotating tasks between operators reduces monotony-related lapses, while ergonomic seating minimizes physical strain.
Are Forklift Accidents More Common in Specific Industries?
Warehousing, construction, and manufacturing report 70% of incidents due to high equipment usage and time pressures. Retail distribution centers face unique risks from narrow aisles and rapid inventory turnover. Agriculture and mining industries contend with uneven terrain and outdoor hazards like mud or gravel.
Expert Views
“Proactive safety cultures reduce forklift incidents by up to 50%,” says Redway’s Chief Safety Officer. “Invest in predictive analytics to anticipate risks—like correlating accident data with shift times or weather conditions. Pair AI-driven insights with operator feedback loops to create adaptive protocols that address both human and systemic factors.”
Conclusion
Mitigating forklift incidents demands a holistic approach: rigorous training, predictive maintenance, smart workplace design, and technology integration. Prioritizing compliance and fatigue management further safeguards operations. Companies that adopt data-driven strategies and foster safety-first mindsets not only reduce accidents but also enhance productivity and employee morale.
FAQs
- Q: How often should forklift operators receive refresher training?
- A: OSHA mandates refresher training every three years, or after accidents, near-misses, or changes in equipment/workplace conditions.
- Q: What percentage of forklift accidents involve pedestrians?
- A: Approximately 20% of forklift accidents injure pedestrians, often due to limited visibility or absent separation barriers.
- Q: Can forklifts be modified for extreme environments?
- A: Yes—specialized tires, corrosion-resistant coatings, and explosion-proof components adapt forklifts for cold storage, chemical plants, or construction sites.
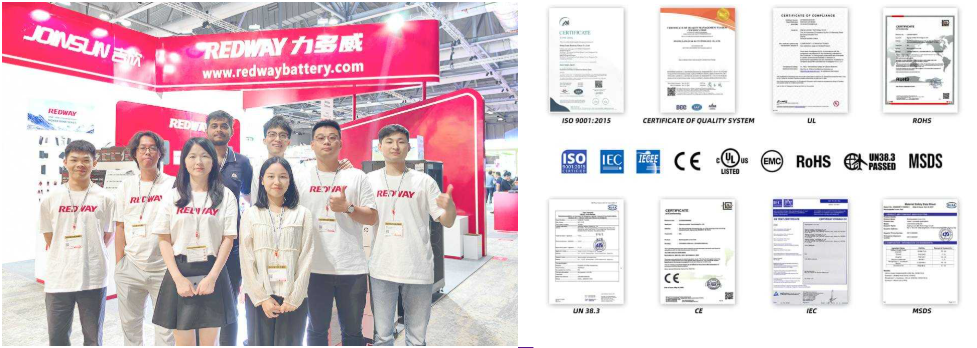